Hexbasher
Well-Known Member
- Joined
- Sep 24, 2007
- Messages
- 73
- Reaction score
- 1
Haven't seen any posts about them here, though, not useful for flatness for engine building, but good for making tooling, fixtures and for surface finish for models
Finally made one today that i've been wanting to make for a while now, 6 hours of relaxed work
(^^^notice those precision 6inch scale parallels)
(^^^after grinding)
(i didnt take many pics cus i cant take a nice picture while the VMC is running)
first step was tossing the piece of cast iron on the lathe and faced both sides
second was to mill the two little steps on the sides. these are here for two reasons, 1 to have better bite to clamp with the vise while milling the serrations. 2 to have something to clamp nicely and solid in a bench vise while actually using the plate for lapping
next was the face mill and do the serrations on the cnc mill...the serrations can be done with no problems on a manual horz mill with a 90 deg duel angle cutter, or on a vert mill with a 90 deg end mill...i used a 1/4 solid carbide chamfering tool. ran at 6000 RPM and 3.0 IPM....took 1 3/4 hours to mill the serrations on the cnc....a horz mill or a shaper wouldn't take long at all
next was to surface grind the back side then the top side (side with the serrations)....surface grinding is very important to give it flatness if you want to lap accurately...a fly cutter or a 'good lathe' will give you acceptable flatness for lapping for good surface finishing
when grinding cast iron (or iron in general) use al ox. with a soft bond and reasonably coarse grit...if ya don't (all i had was a al ox. wheels with a med grit and hard bond) grind dry, rough at 0.001 and finish 0.0005 or less...dress the wheel as often as possible
mine was made from class 3 grey iron ('cast' is the best, nice and soft for the compound to get embedded, any material with 'embedibility' properties will work, but cast iron is the most practical for plates, but brass and bronze are great for making cylindrical laps for holes, i'll post up nice time i make one of those, prob great for lapping cylinder bores)
my plate is 6.25 dia and the serrations are 0.025 deep (x 90 deg = 0.050 wide) with a 0.25 step over....and the backside also serves as a small surface plate
Finally made one today that i've been wanting to make for a while now, 6 hours of relaxed work
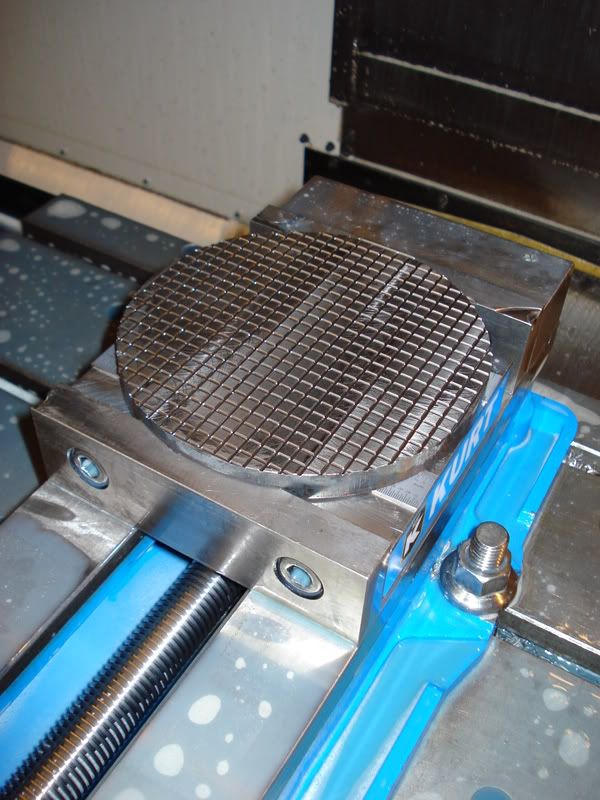
(^^^notice those precision 6inch scale parallels)
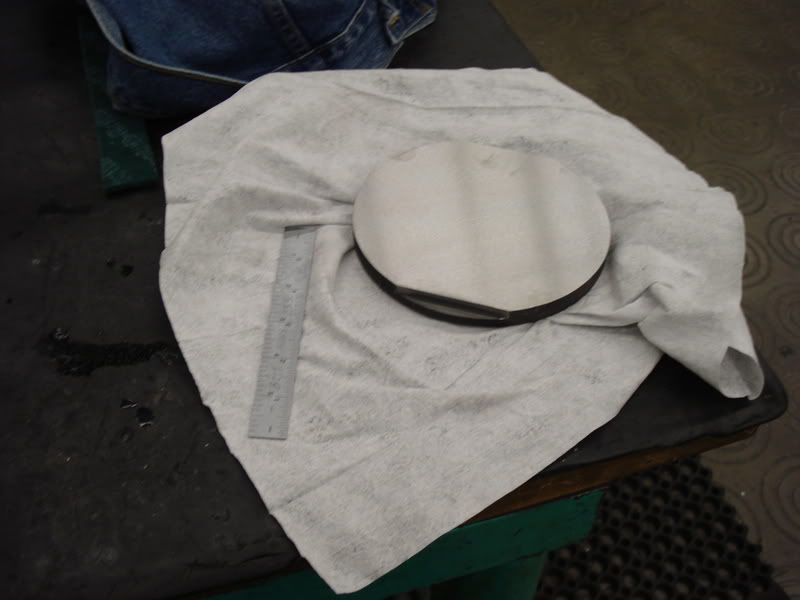
(^^^after grinding)
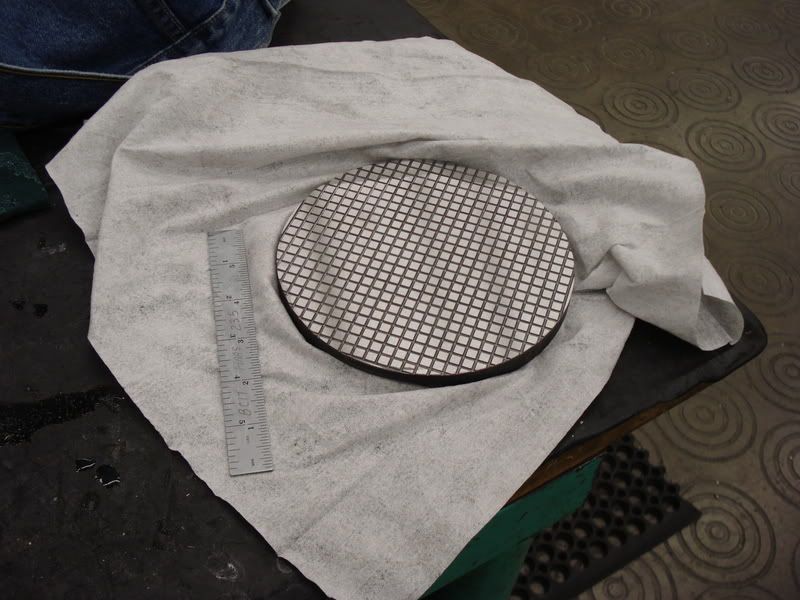
(i didnt take many pics cus i cant take a nice picture while the VMC is running)
first step was tossing the piece of cast iron on the lathe and faced both sides
second was to mill the two little steps on the sides. these are here for two reasons, 1 to have better bite to clamp with the vise while milling the serrations. 2 to have something to clamp nicely and solid in a bench vise while actually using the plate for lapping
next was the face mill and do the serrations on the cnc mill...the serrations can be done with no problems on a manual horz mill with a 90 deg duel angle cutter, or on a vert mill with a 90 deg end mill...i used a 1/4 solid carbide chamfering tool. ran at 6000 RPM and 3.0 IPM....took 1 3/4 hours to mill the serrations on the cnc....a horz mill or a shaper wouldn't take long at all
next was to surface grind the back side then the top side (side with the serrations)....surface grinding is very important to give it flatness if you want to lap accurately...a fly cutter or a 'good lathe' will give you acceptable flatness for lapping for good surface finishing
when grinding cast iron (or iron in general) use al ox. with a soft bond and reasonably coarse grit...if ya don't (all i had was a al ox. wheels with a med grit and hard bond) grind dry, rough at 0.001 and finish 0.0005 or less...dress the wheel as often as possible
mine was made from class 3 grey iron ('cast' is the best, nice and soft for the compound to get embedded, any material with 'embedibility' properties will work, but cast iron is the most practical for plates, but brass and bronze are great for making cylindrical laps for holes, i'll post up nice time i make one of those, prob great for lapping cylinder bores)
my plate is 6.25 dia and the serrations are 0.025 deep (x 90 deg = 0.050 wide) with a 0.25 step over....and the backside also serves as a small surface plate