DICKEYBIRD
Well-Known Member
- Joined
- Sep 27, 2007
- Messages
- 653
- Reaction score
- 46
My project for the weekend was supposed to be a tangential toolholder for the QCTP like John Moran shows on his site but I didn't have a dovetail cutter.
Using the info on his and Bob Warfield's sites I made my own from a chunk of 4140 pre-hard I had on hand and a cheap TCMT insert I got from CDCO.
You have to be patient with the 4140 but it came out nice and the finished tool cut the dovetails real nicely in 6061 aluminum. It remains to be seen how it does in steel.
Using the info on his and Bob Warfield's sites I made my own from a chunk of 4140 pre-hard I had on hand and a cheap TCMT insert I got from CDCO.
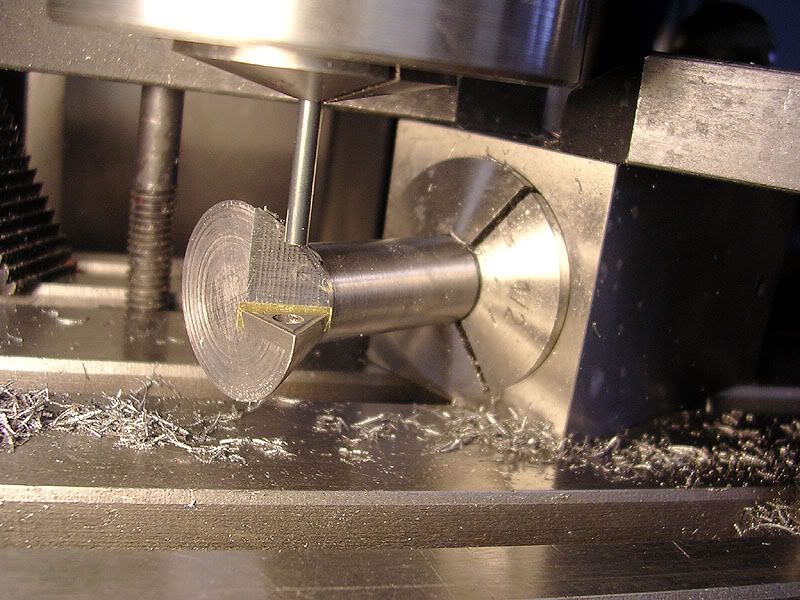
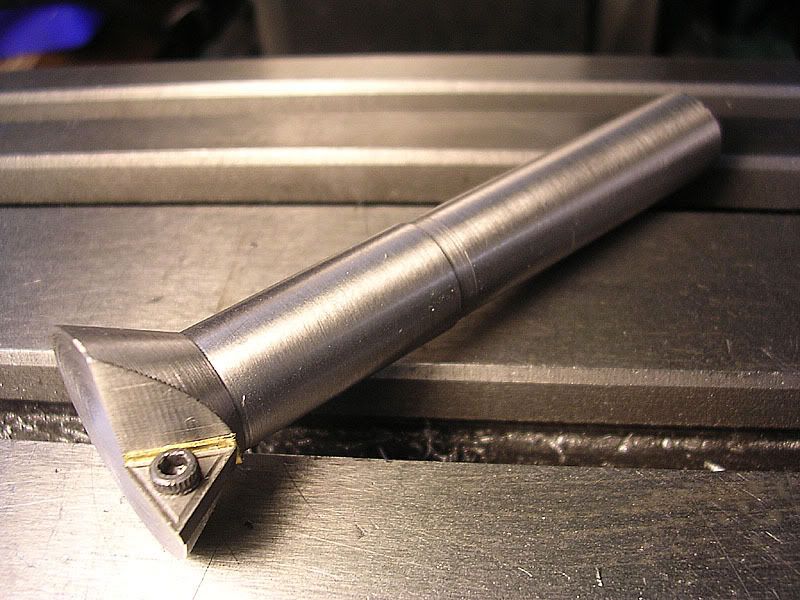
You have to be patient with the 4140 but it came out nice and the finished tool cut the dovetails real nicely in 6061 aluminum. It remains to be seen how it does in steel.
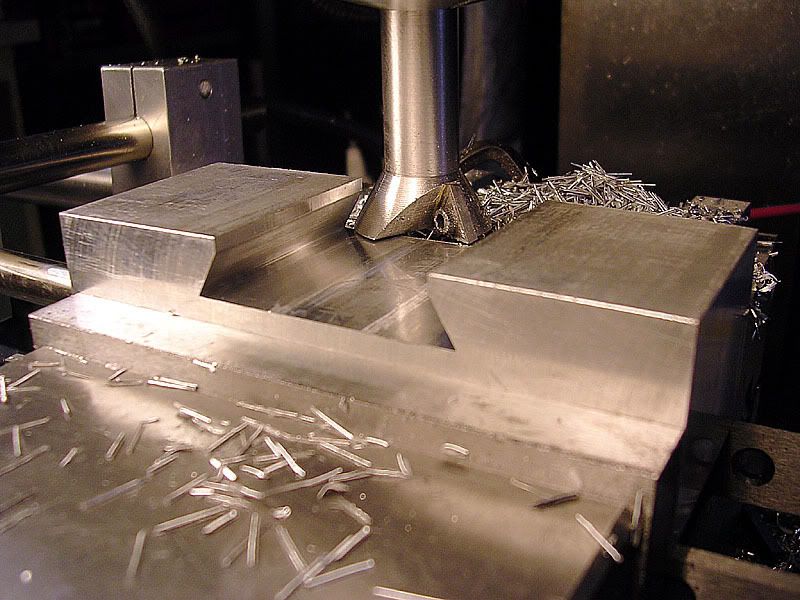