I started to make the patterns for the mill a couple of days ago. So far the main bed and the spindle tower are made. I may do some casting in the next couple of days.
The patterns are made from fiber board there is no grain to worry bout the stuff is easy to cut and sand. I use wood glue and staples to hold the parts together.
For miss matched parts I use bondo to fix the problems. I paint the parts in water based varnish 2 coats then coat the part in 2 coats of Johnson's paste wax, hand rubbing them for a fairly slick finish.
I made the bases tonight just put the first coat of varnish on, they should be ready to use Saturday, so I'll be doing some casting as long as it don't rain,it never rains here in the Texas panhandle unless you want to go ride the motorcycle or cast metal???? Living in tornado alley can be pretty hair raising at times.
Norman
the base and the spindle patterns.
the spindle pattern is a split pattern. I like casting these it's more fun to see if I can get it out of the sand with out messing it up.
The patterns are made from fiber board there is no grain to worry bout the stuff is easy to cut and sand. I use wood glue and staples to hold the parts together.
For miss matched parts I use bondo to fix the problems. I paint the parts in water based varnish 2 coats then coat the part in 2 coats of Johnson's paste wax, hand rubbing them for a fairly slick finish.
I made the bases tonight just put the first coat of varnish on, they should be ready to use Saturday, so I'll be doing some casting as long as it don't rain,it never rains here in the Texas panhandle unless you want to go ride the motorcycle or cast metal???? Living in tornado alley can be pretty hair raising at times.
Norman
the base and the spindle patterns.
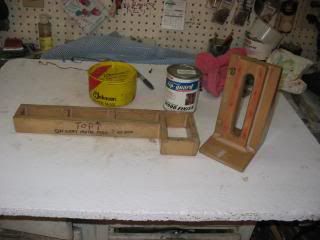
the spindle pattern is a split pattern. I like casting these it's more fun to see if I can get it out of the sand with out messing it up.
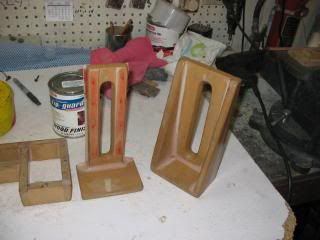