- Joined
- Jan 17, 2009
- Messages
- 887
- Reaction score
- 81
The three point steady as delivered with my lathe when new a few years back now has a lot to be desired I don't like its design and build quality at all, but I didn't worry too much about it at the time as its one bit of kit you don't use a lot, in fact the one and only time I've used one was way back in my apprentice days.
But I now need one to trim the 3 3/8 dia copper tube down to length for my boiler, it has to be square and neat.
Here's the steady.
What wrong with it well for a start when it's clamped on the lathe it wobbles more than Dolly Parton on a bad bra day, the hinge is very sloppy the clamp doesn't pull up tight on the lathe bed, and those pointed steadies are just not right, I don't think the frame is substantial enough, I cant do anything about the frame but the other things I can.
To fix the hinge I opened the hole up from 8mm to 3/8" first with a letter U drill then a 3/8 hand reamer, and fitted a 1mm copper spacer to take up the slide slop.
The rusty pin is the one that was supplied.
The points on the steadies are just brass I thought they would be screwed in but No they were glued in place, once I worked that out I managed to nock them out. Then turned up some new ones that will give a nice supporting area and fixed them in place with supper glue.
As the new brass bits have a larger diameter than the rods they have to be assembled from the inside, they wouldn't assemble as the bars had just bin left as parted off no chamfer, back in the lathe and a chamfer was added: job sorted, the build standard of some Chinese made parts have a lot to be desired its a great pity as people remember the bad things and not the good.
I'll make some new clamping blocks to fix it firmly to the lathe, but thats a job for tomorrow.
Cheers
Stew
But I now need one to trim the 3 3/8 dia copper tube down to length for my boiler, it has to be square and neat.
Here's the steady.
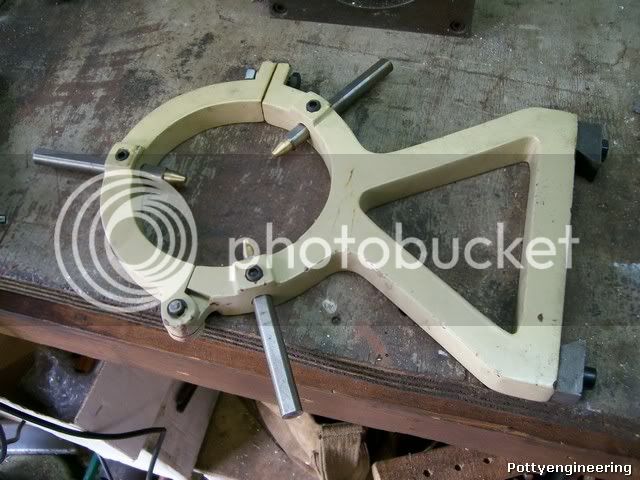
What wrong with it well for a start when it's clamped on the lathe it wobbles more than Dolly Parton on a bad bra day, the hinge is very sloppy the clamp doesn't pull up tight on the lathe bed, and those pointed steadies are just not right, I don't think the frame is substantial enough, I cant do anything about the frame but the other things I can.
To fix the hinge I opened the hole up from 8mm to 3/8" first with a letter U drill then a 3/8 hand reamer, and fitted a 1mm copper spacer to take up the slide slop.
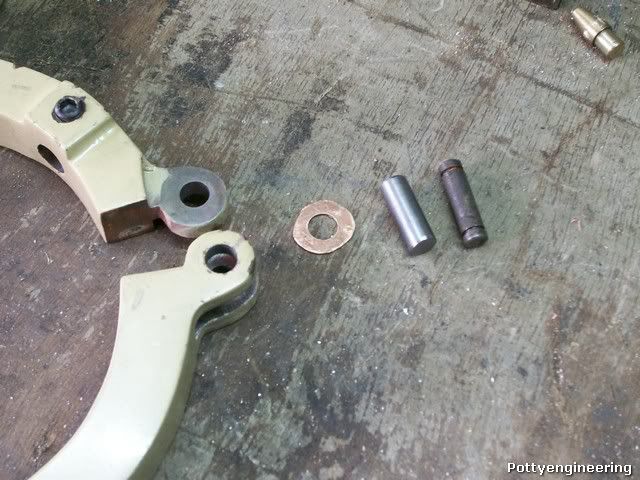
The rusty pin is the one that was supplied.
The points on the steadies are just brass I thought they would be screwed in but No they were glued in place, once I worked that out I managed to nock them out. Then turned up some new ones that will give a nice supporting area and fixed them in place with supper glue.
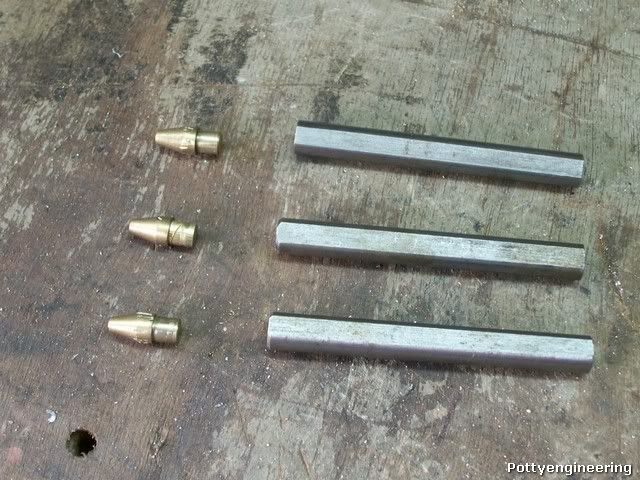
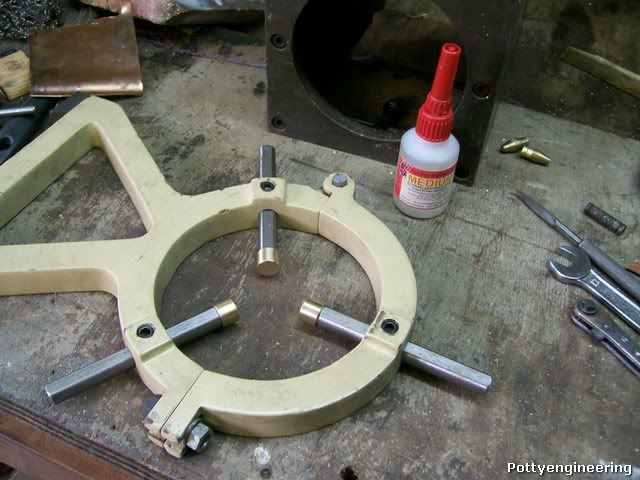
As the new brass bits have a larger diameter than the rods they have to be assembled from the inside, they wouldn't assemble as the bars had just bin left as parted off no chamfer, back in the lathe and a chamfer was added: job sorted, the build standard of some Chinese made parts have a lot to be desired its a great pity as people remember the bad things and not the good.
I'll make some new clamping blocks to fix it firmly to the lathe, but thats a job for tomorrow.
Cheers
Stew