I have a couple of old short stroke air cylinders left over from a job I did a few years ago. They are 1 3/8" bore x 3/4" stroke. I got thinking the other day about using one of them to build a bell-crank actuated steam/air engine. The more I thought about it, the more I wondered "Why not build a double ended bell crank mechanism, and use both cylinders?" As one cylinder extends under air pressure, the other engine could be retracting under air pressure. This would give double the power, and the valving would still be relatively simple--the two lines running from the valve would split and go to opposite ends of the two cylinders. Only one valve would actually be required to run both of the cylinders simultaneously. This would in effect require a valve similar to the one on the beam engine I designed a couple of years ago, which had one double acting cylinder. --Only difference would be that instead of the valve bore being in the same block as the cylinder, it would become a "stand alone" unit with one constant pressure airline feeding it and two airlines leaving it which would alternate the flow to either the rod end or the cap end of a single cylinder---or in this case, each line would split to deliver air to opposite ends of the two cylinders. I spent a couple of hours "fleshing out" the design this morning. I haven't given any real design time to the valve, but did design and model whats been buzzing about in the back of my brain. Then of course, not being able to leave well enough alone, I animated the model and saved a video clip of the animation. Interesting concept, isn't it.----Brian
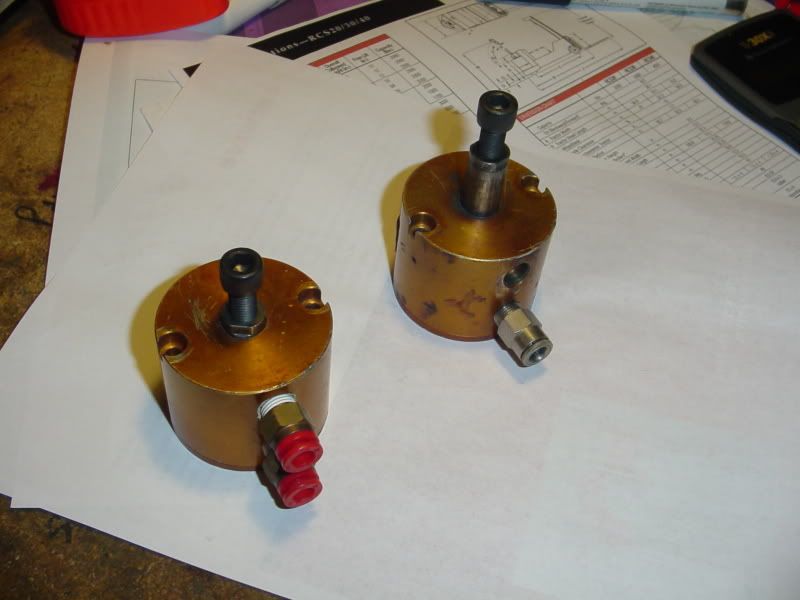