or..... how the hell do I do it?
I jumped in tonight and it was a case of sink or swim.... I sank...... :fan:
The problem is simple... I have had great success with flat surface milling using the shaper and thought this going to be a straight forward process also. Not so. :wall:
I have hit 2 snags and I think I have them both solved but now wonder what else am I about to encounter?
First one was I didnt know I needed to lock the clapper and as it lifted on the back stroke it damaged the edge of the surface I was cutting (you can see the damage on the thin edge of the taper in the pic below, it looks all ragged thanks to the tool dragging back over it).
The second was I had trouble getting the tool to cut efficiently on both sides of the 58 degree cutter, I ground it to 58 and not 60 so I could take light cuts off each face of the taper and have a clearance angle on the other. I experimented with this and think that I have it ok now but I wouldnt mimd seeing what others have done.
I have the feed set at 30 deg from vertical to give me the 60 deg dovetail and have experimented with canting the tool holder at some extreme angles combined with various (corresponding) angle ground onto the cutter. Please ignore the cutter shape (and excessive tool angle and extension) in this pic, its was a wild experiment while I was frustrated.
My question is this... Would it be possible for those who have cut dovetails with the shaper to share their experience or technique? Please..... stickpoke *discussion*
Rob
I jumped in tonight and it was a case of sink or swim.... I sank...... :fan:
The problem is simple... I have had great success with flat surface milling using the shaper and thought this going to be a straight forward process also. Not so. :wall:
I have hit 2 snags and I think I have them both solved but now wonder what else am I about to encounter?
First one was I didnt know I needed to lock the clapper and as it lifted on the back stroke it damaged the edge of the surface I was cutting (you can see the damage on the thin edge of the taper in the pic below, it looks all ragged thanks to the tool dragging back over it).
The second was I had trouble getting the tool to cut efficiently on both sides of the 58 degree cutter, I ground it to 58 and not 60 so I could take light cuts off each face of the taper and have a clearance angle on the other. I experimented with this and think that I have it ok now but I wouldnt mimd seeing what others have done.
I have the feed set at 30 deg from vertical to give me the 60 deg dovetail and have experimented with canting the tool holder at some extreme angles combined with various (corresponding) angle ground onto the cutter. Please ignore the cutter shape (and excessive tool angle and extension) in this pic, its was a wild experiment while I was frustrated.
My question is this... Would it be possible for those who have cut dovetails with the shaper to share their experience or technique? Please..... stickpoke *discussion*
Rob
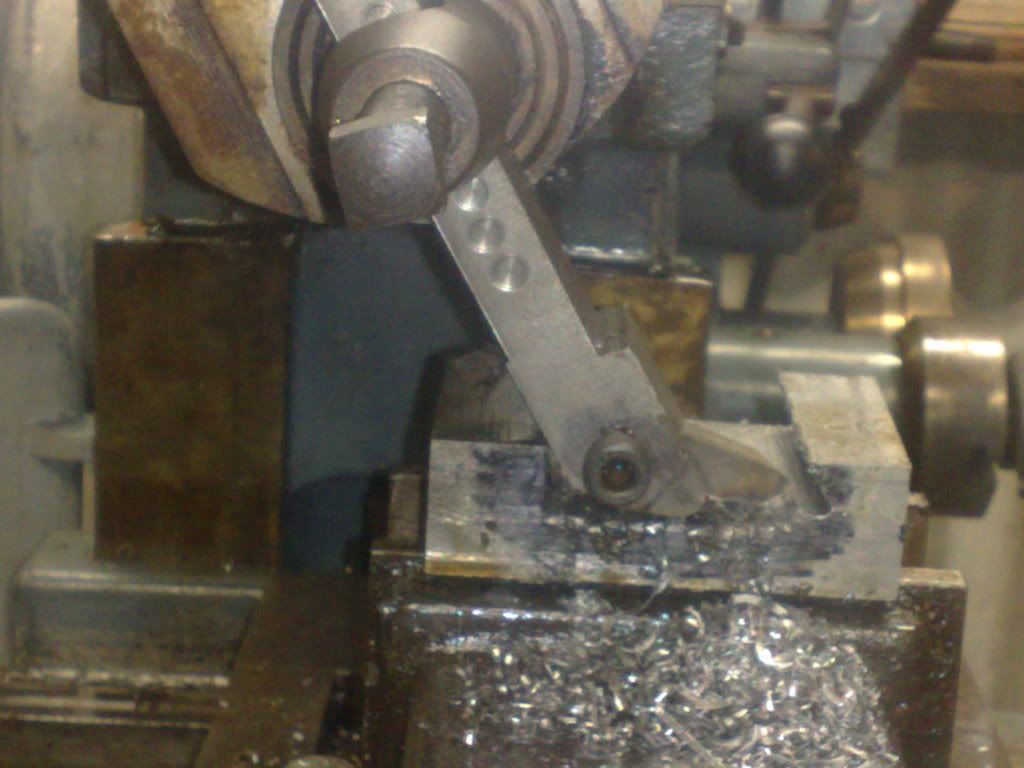