[Edited to allow playback within the forum]
Well I finally got back to building the PM research engine lathe.
I needed to cut a 4" long keyway in a .187" OD shaft 4" long. I think Marv used a slitting saw and Chili used a tiny 1/32" end mill to cut this keyway on their model PM lathes. Well I had neither tool handy so I thought why not just do it like a shaper would. So I ground a 1/8" square HSS bit to a width of .031", gave it some clearance angles and used a fine grit diamond hone to give it a razors edge. Installed it in a collet and used my spindle quill clamp to lock the spindle tight from rotation.
16 passes taking .002" DOC's resulted in a beautifully cut mini keyway for the feed shaft.
A couple pics and a short movie showing how nice it cut. I'll definitely use this method again in the future.
http://i109.photobucket.com/player.swf?file=http://s109.photobucket.com/albums/n48/S_J_H/keyway-1.flv
Well I finally got back to building the PM research engine lathe.
I needed to cut a 4" long keyway in a .187" OD shaft 4" long. I think Marv used a slitting saw and Chili used a tiny 1/32" end mill to cut this keyway on their model PM lathes. Well I had neither tool handy so I thought why not just do it like a shaper would. So I ground a 1/8" square HSS bit to a width of .031", gave it some clearance angles and used a fine grit diamond hone to give it a razors edge. Installed it in a collet and used my spindle quill clamp to lock the spindle tight from rotation.
16 passes taking .002" DOC's resulted in a beautifully cut mini keyway for the feed shaft.
A couple pics and a short movie showing how nice it cut. I'll definitely use this method again in the future.
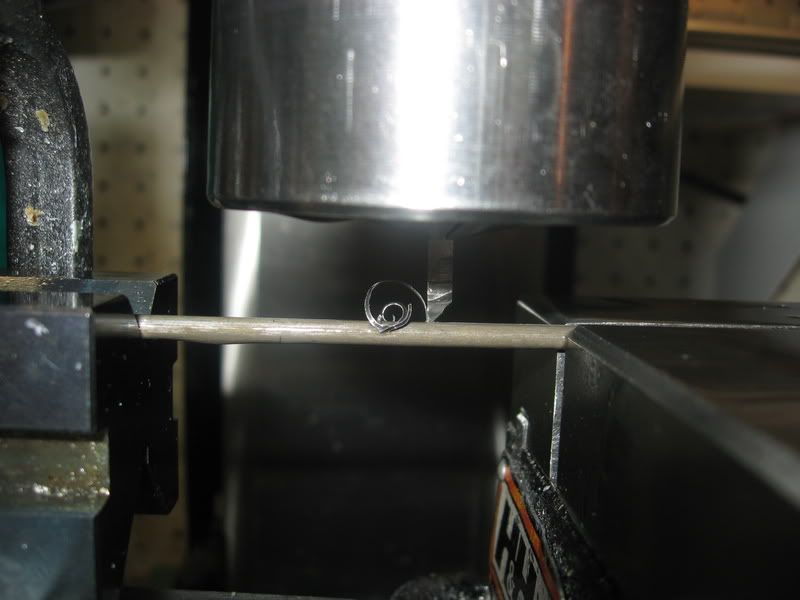
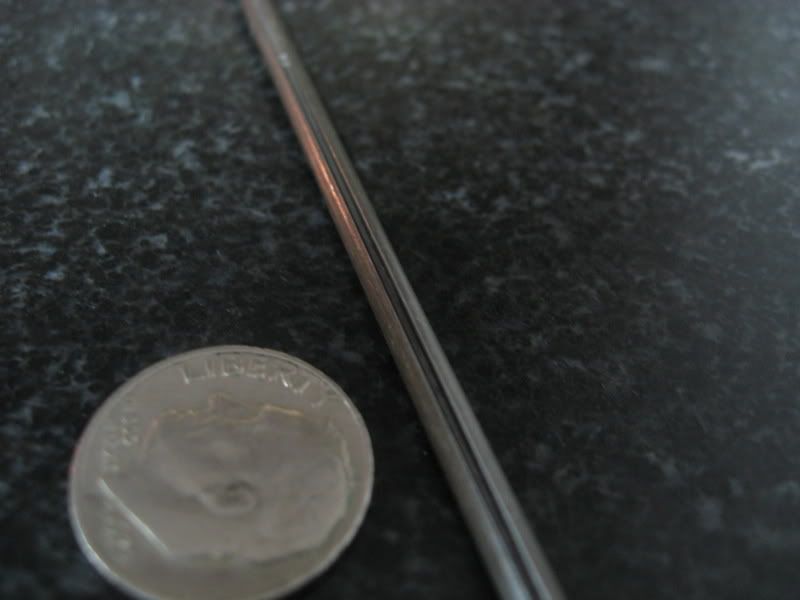
http://i109.photobucket.com/player.swf?file=http://s109.photobucket.com/albums/n48/S_J_H/keyway-1.flv