This engine was started a while ago and I just had to experiment with the crankshaft as it seemed that everyone said they were difficult. I posted my attempt here :-
http://www.homemodelenginemachinist.com/index.php?topic=11472.0
It turned out so well that it was good enough for this compressed air V8. The air porting was to be in and out like my Scrap Bin Motor (Thanks for all the interest) but Chuck Fellows showed how he had made his porting with a ball and spring. This is so elegantly simple that I had to copy this idea for the V8, so that meant I had to rethink my ideas. The Twin D/A Oscillator took up some of my spare time so the V8 has been on hold.
However I am back to it now. It will be 12mm bore 12mm stroke with the "camshaft" in the middle of the V driven at the same speed as the crankshaft by nylon gears at the front. On an air engine of this size, three bearings should be enough, ball races front and rear and a split plain bearing in the middle. The experimental pistons will be made from PEEK which is a high temperature plastic which turns easily is harder than nylon and does not have the same water absorption problems. It is expensive but I managed to strike lucky on Ebay.
Here is the "Proof of Concept" drawing :-
It will be made from brass bar stock. The finning is just bling. Lots of detailing to do yet, exhaust should be 4 into one both sides, so I am hoping that it will sound interesting!
Ian
http://www.homemodelenginemachinist.com/index.php?topic=11472.0
It turned out so well that it was good enough for this compressed air V8. The air porting was to be in and out like my Scrap Bin Motor (Thanks for all the interest) but Chuck Fellows showed how he had made his porting with a ball and spring. This is so elegantly simple that I had to copy this idea for the V8, so that meant I had to rethink my ideas. The Twin D/A Oscillator took up some of my spare time so the V8 has been on hold.
However I am back to it now. It will be 12mm bore 12mm stroke with the "camshaft" in the middle of the V driven at the same speed as the crankshaft by nylon gears at the front. On an air engine of this size, three bearings should be enough, ball races front and rear and a split plain bearing in the middle. The experimental pistons will be made from PEEK which is a high temperature plastic which turns easily is harder than nylon and does not have the same water absorption problems. It is expensive but I managed to strike lucky on Ebay.
Here is the "Proof of Concept" drawing :-
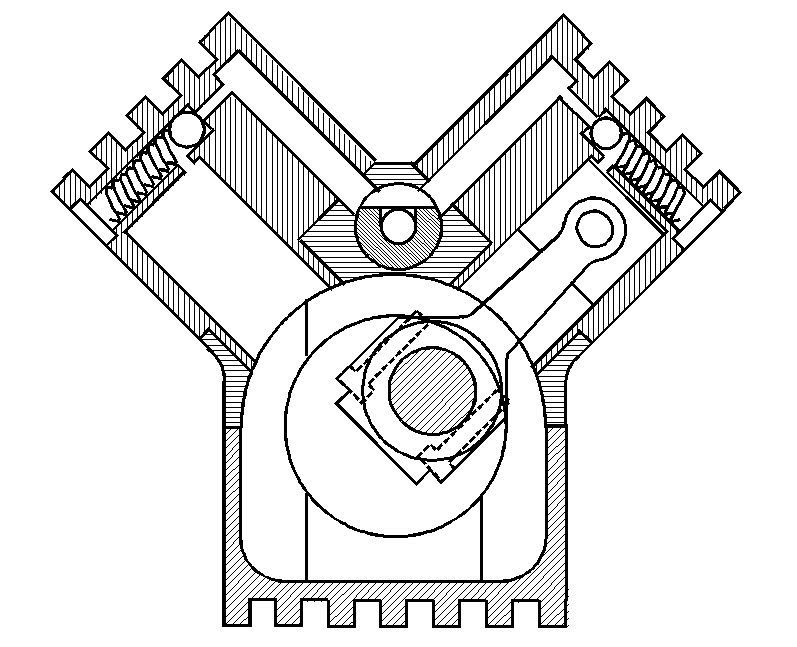
It will be made from brass bar stock. The finning is just bling. Lots of detailing to do yet, exhaust should be 4 into one both sides, so I am hoping that it will sound interesting!
Ian