PolskiFran
Well-Known Member
- Joined
- Dec 7, 2007
- Messages
- 61
- Reaction score
- 0
Part 1
I have had a few requests to post more pics of my small J&H drillpress. I thought I would post the pics of the restoration process that I went through on this project. Some of this information may be useful if you are going to restore one of the "original" antique engines, or if you are looking to put one of your small engines to "work".
The drillpress was manufactured by J&H Metal Products of Rochester NY. I believe it was produced sometime between the late 1930's to early 1950's. This is the type of drill that was sold to the home machinst / hobbyist of that era. They were probably sold through advertisements in Popular Mechanics type magazines of that time.
The drillpress was purchased at a swap meet for $1.00. At this point it was rusty, corroded, dirty, and bent. Every joint and shaft wobbled and there were chunks missing from the wooden pulleys.
I put penetrating oil on all the joints and screws and disassembled everthing carefully. The screws were removed by loosening 1/4 turn then tightening 1/4 turn to work the rust loose and reform the threads on the screw ends. The rivets that held the quill feed lever and linkage were carefully ground off at the peened end with a dremel grinder. All the removed parts were put in a box for safe keeping.
Frank
I have had a few requests to post more pics of my small J&H drillpress. I thought I would post the pics of the restoration process that I went through on this project. Some of this information may be useful if you are going to restore one of the "original" antique engines, or if you are looking to put one of your small engines to "work".
The drillpress was manufactured by J&H Metal Products of Rochester NY. I believe it was produced sometime between the late 1930's to early 1950's. This is the type of drill that was sold to the home machinst / hobbyist of that era. They were probably sold through advertisements in Popular Mechanics type magazines of that time.
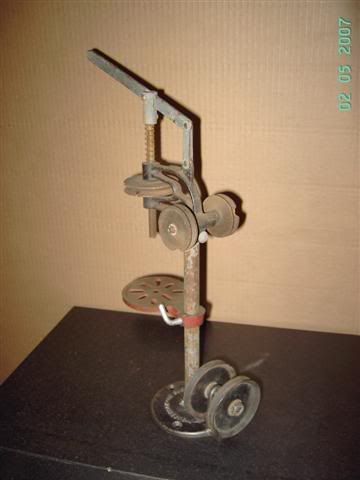
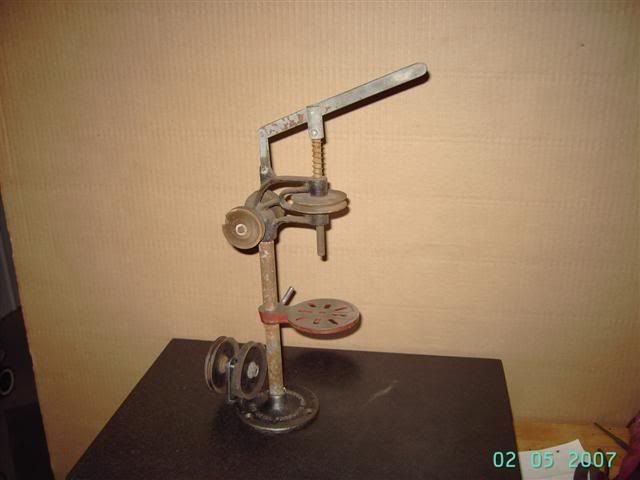
The drillpress was purchased at a swap meet for $1.00. At this point it was rusty, corroded, dirty, and bent. Every joint and shaft wobbled and there were chunks missing from the wooden pulleys.
I put penetrating oil on all the joints and screws and disassembled everthing carefully. The screws were removed by loosening 1/4 turn then tightening 1/4 turn to work the rust loose and reform the threads on the screw ends. The rivets that held the quill feed lever and linkage were carefully ground off at the peened end with a dremel grinder. All the removed parts were put in a box for safe keeping.
Frank