Sshire
Well-Known Member
- Joined
- Jun 29, 2011
- Messages
- 936
- Reaction score
- 259
All dressed up.
The Bridgeport has been at home for 5 days and I've been busy.
First I sat down at the mill with the manual and went through every procedure.
UPS has been busier than usual here. Packages every day.
After installing the VFD, I bolted on:
DRO (2-axis; glass scales)
Quill DRO
X-axis power feed (Servo Dynamo)
Finally, my shoulder was hurting big time from reaching up to the drawbar. The stepstool was a PIA and it seemed as if I were tripping over it every 2 minutes. Here's the solution. It's not one of the butterfly wrench conversions but designed from the ground up as a power drawbar. Heavy chunk of machinery, built beautifully, great directions and MADE in the USA.
One more project. Clean out the Bijur One-shot oiler and make sure all lines are clear. Then, back to Elmer's Pumping Engine.
The Bridgeport has been at home for 5 days and I've been busy.
First I sat down at the mill with the manual and went through every procedure.
UPS has been busier than usual here. Packages every day.
After installing the VFD, I bolted on:
DRO (2-axis; glass scales)
Quill DRO
X-axis power feed (Servo Dynamo)
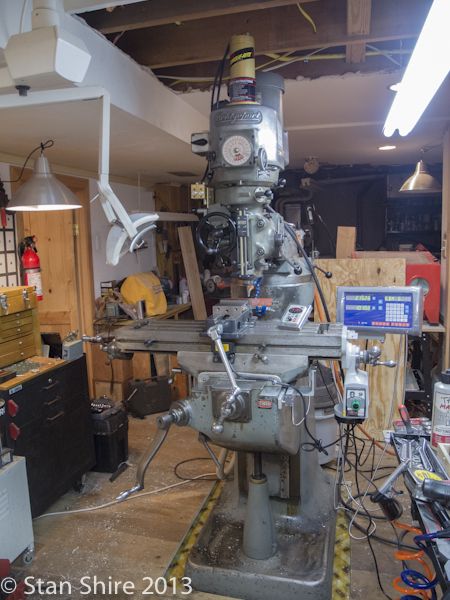
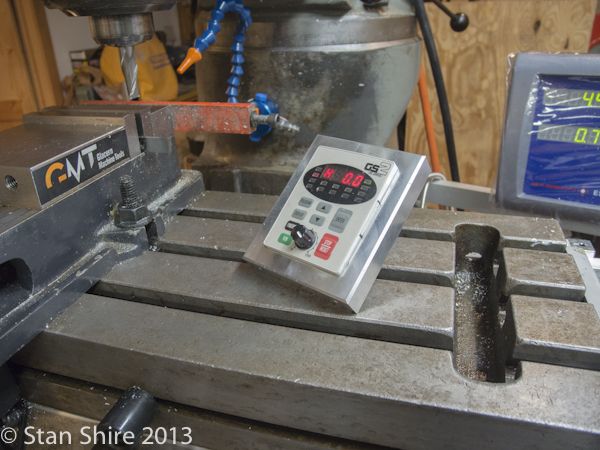
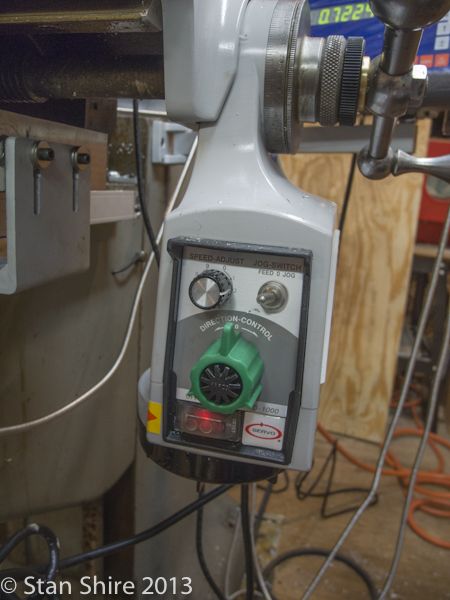
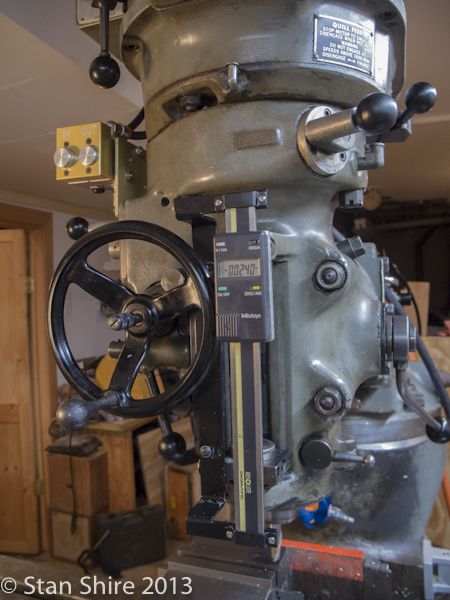
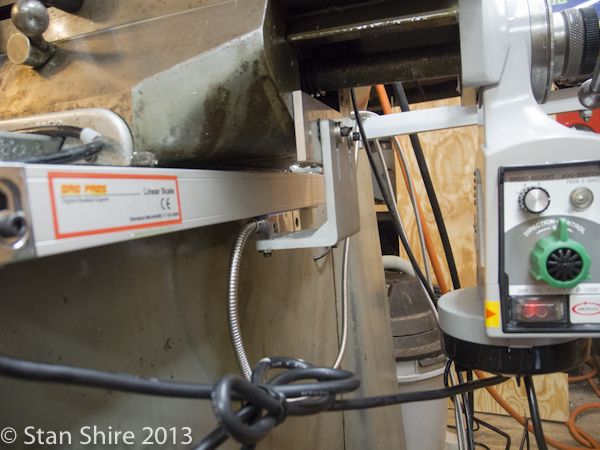

Finally, my shoulder was hurting big time from reaching up to the drawbar. The stepstool was a PIA and it seemed as if I were tripping over it every 2 minutes. Here's the solution. It's not one of the butterfly wrench conversions but designed from the ground up as a power drawbar. Heavy chunk of machinery, built beautifully, great directions and MADE in the USA.
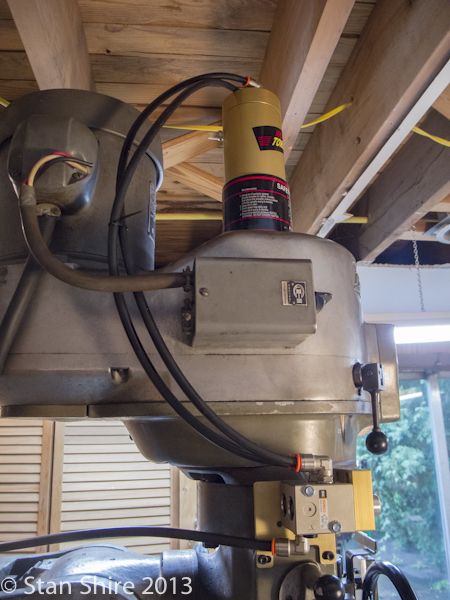
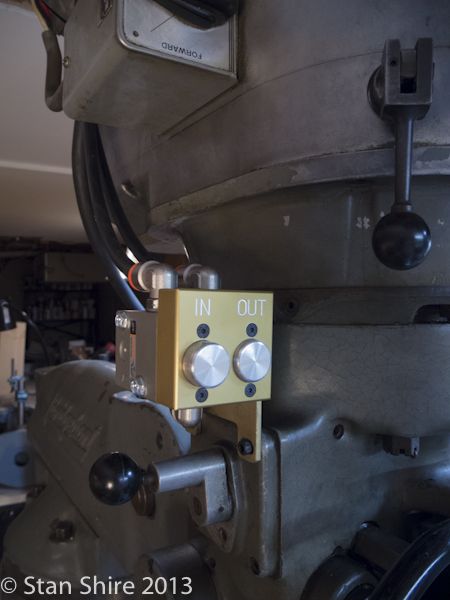
One more project. Clean out the Bijur One-shot oiler and make sure all lines are clear. Then, back to Elmer's Pumping Engine.