- Joined
- Dec 12, 2012
- Messages
- 2,220
- Reaction score
- 1,285
My next project,still in my head and on the back of a cigarette packet
The manual RT I made works well and I use it a lot but the indexing is limited
I thought I would make some thing better and maybe have a go at cutting gears,just for experience ,nothing in particular at this moment.So its build as you go and we will see what pops out at the end.Build has just started so any input would be most welcome
The manual RT I made works well and I use it a lot but the indexing is limited
I thought I would make some thing better and maybe have a go at cutting gears,just for experience ,nothing in particular at this moment.So its build as you go and we will see what pops out at the end.Build has just started so any input would be most welcome

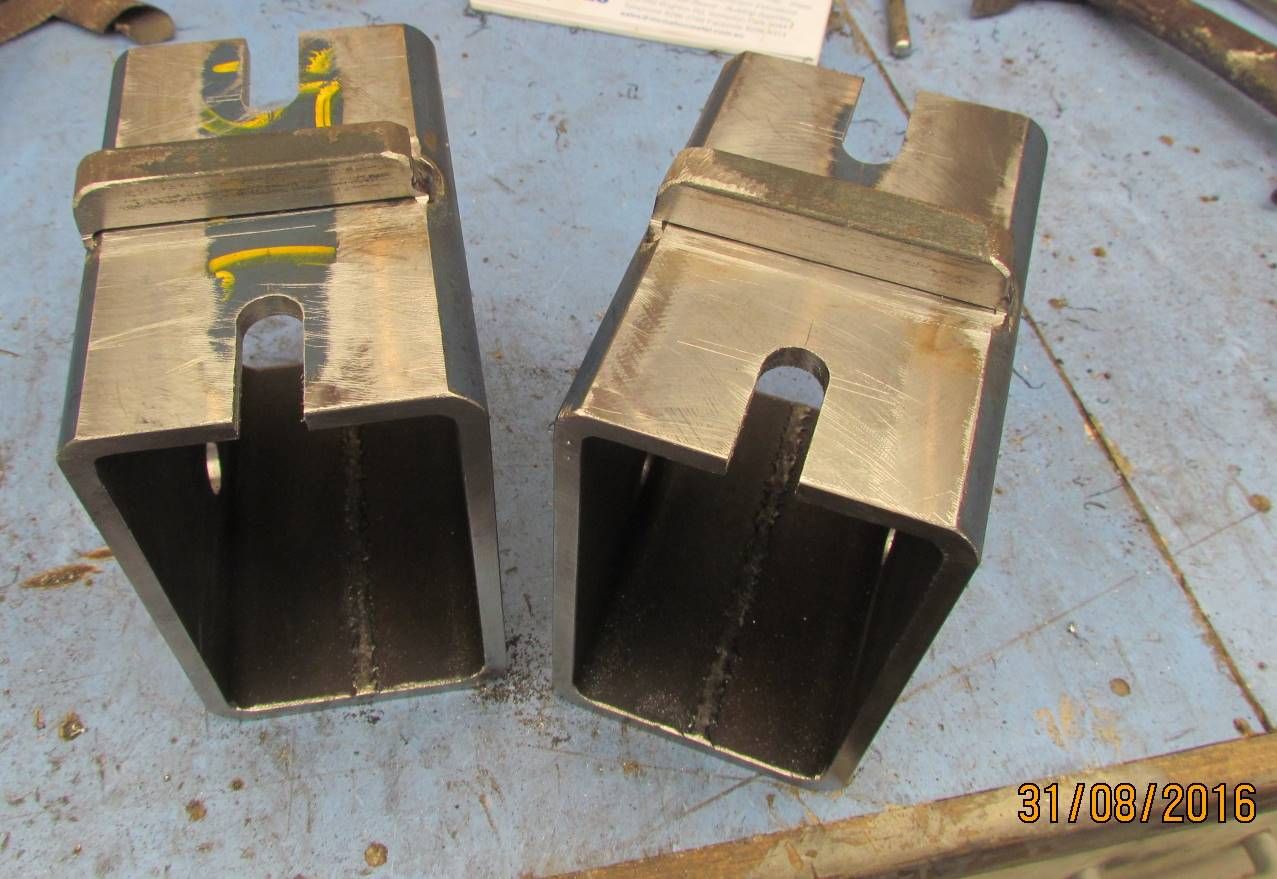
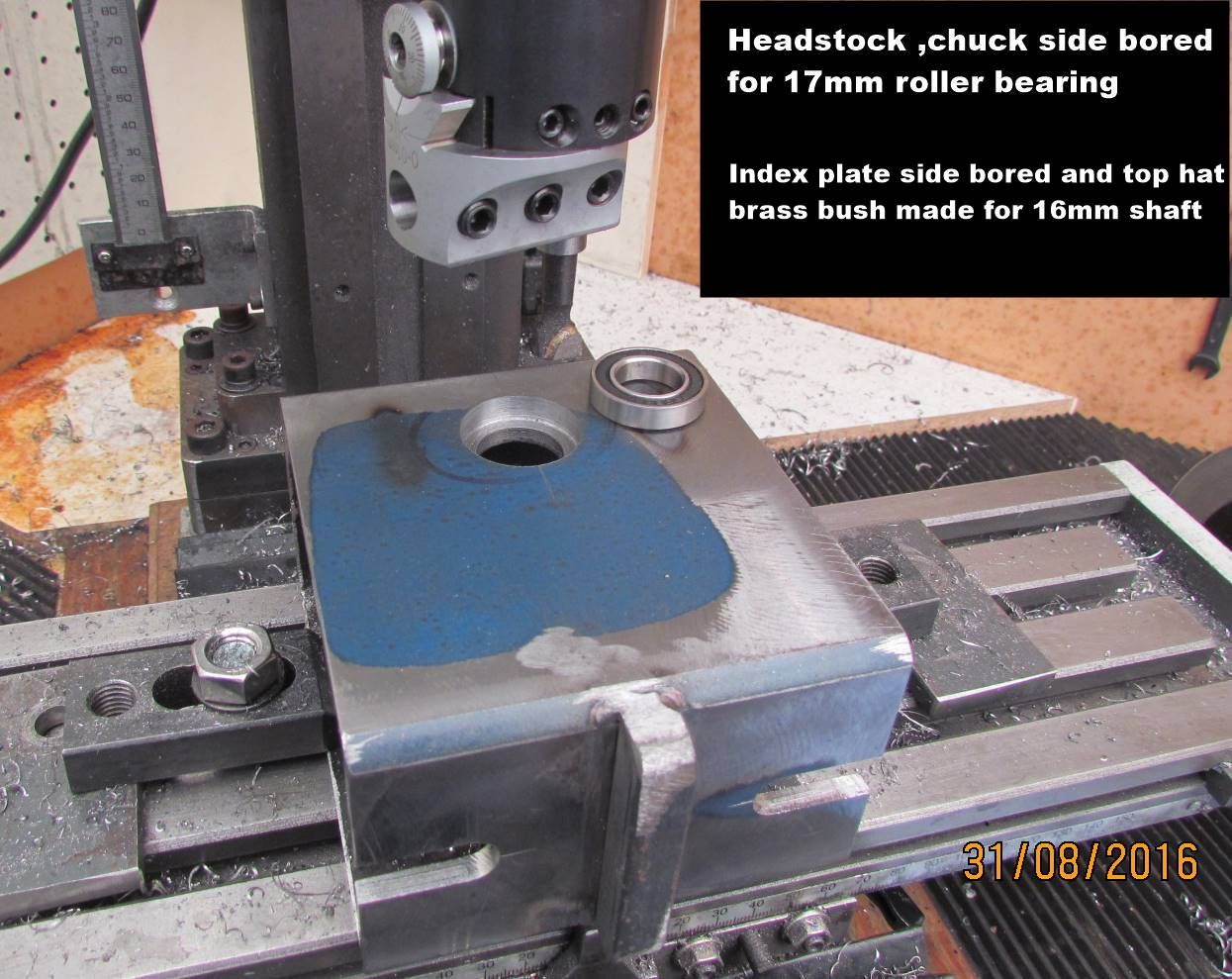
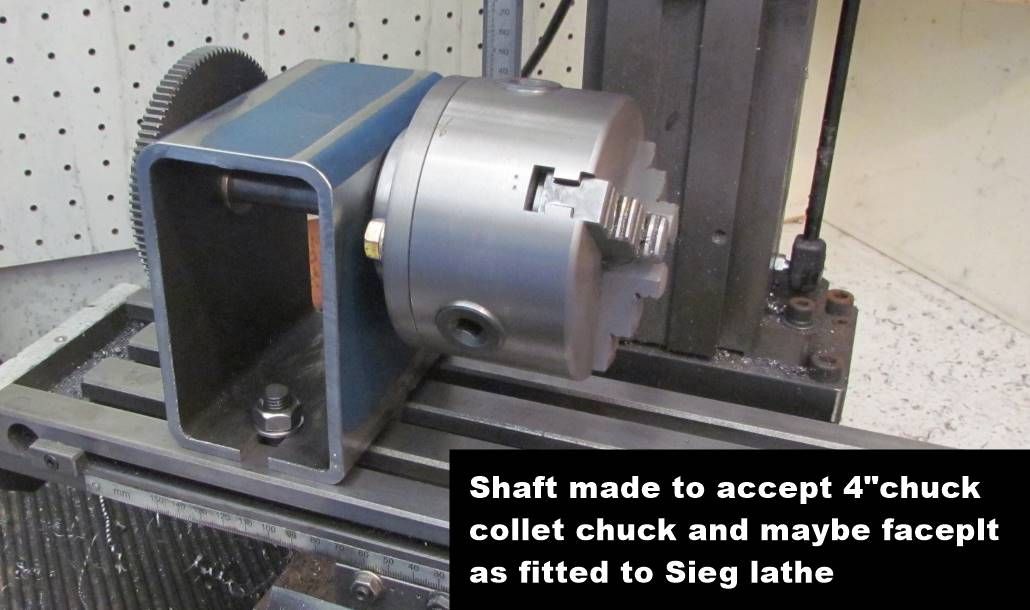
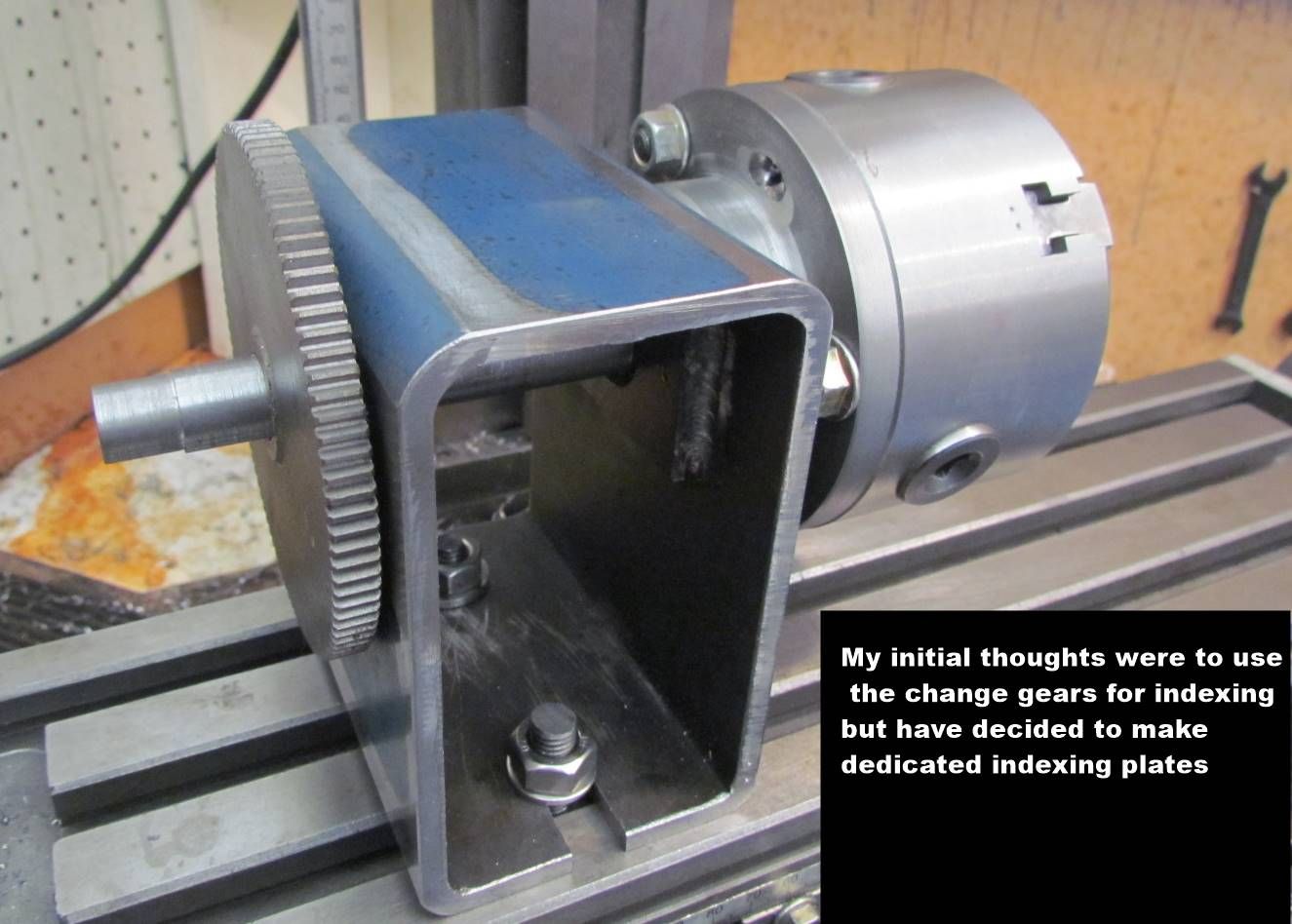