This is not a big mistake, blunder or boo boo, but it is another day in the life of using a light weight CNC mill to make parts. Having a CNC mill is very empowering in that complex parts are taken from design to reality. The down side is once the "go" button is pushed, you better hope everything is planned out correctly and the set up is right. The photo below is my first attempt at the rear bearing housing for the Whittle V8 I'm trying to make. A not too close of an examination will reveal something changed during to course of running the part. So far, the only thing I have been able to figure out is the machine lost steps because I mistakenly set up a climb mill operation and overwhelmed the steppers. All is not lost though. I have a couple of practice parts for the flip side of the housing and I did get the bore diameter for the bearing "spot on" without having to fret about ruining the part!
Sometimes the glass just has to be half full of lemonade. :big: :big:
Steve C.
Sometimes the glass just has to be half full of lemonade. :big: :big:
Steve C.
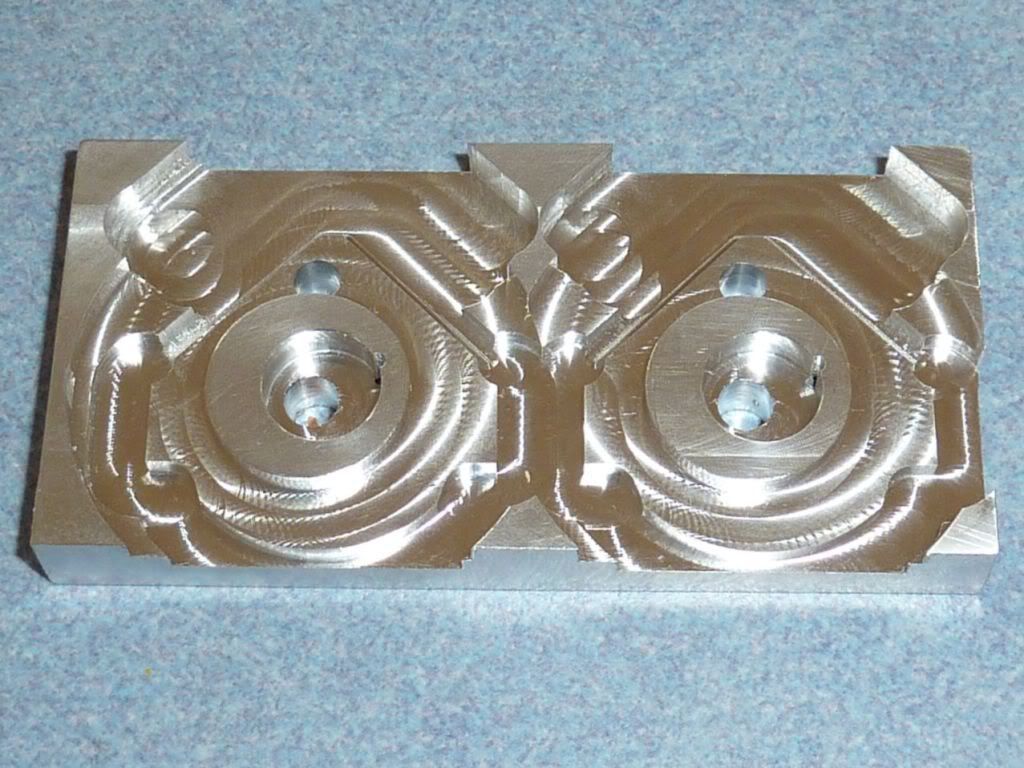