Teza
Well-Known Member
- Joined
- Nov 11, 2011
- Messages
- 48
- Reaction score
- 2
Hi Guys,
I bought a QCTP on eBay for my lathe, some small mods to the "T" nut saw it fitted.
Decided I needed a better way change the angle instead of a shifter on the large hex nut, turned and threaded a some 5/8" round for a handle then onto the shaper to cut some flats for a spanner
Some 1" bored and threaded for the ball handles
Generated co-ordinates to incremental cut the balls
I bought a QCTP on eBay for my lathe, some small mods to the "T" nut saw it fitted.
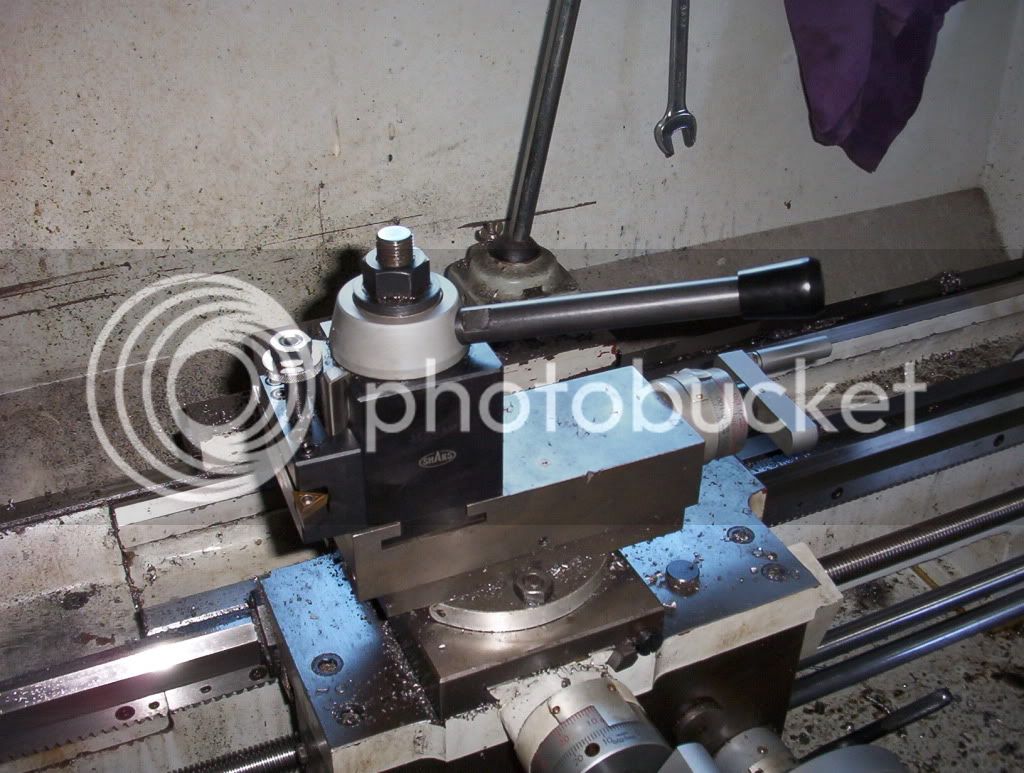
Decided I needed a better way change the angle instead of a shifter on the large hex nut, turned and threaded a some 5/8" round for a handle then onto the shaper to cut some flats for a spanner
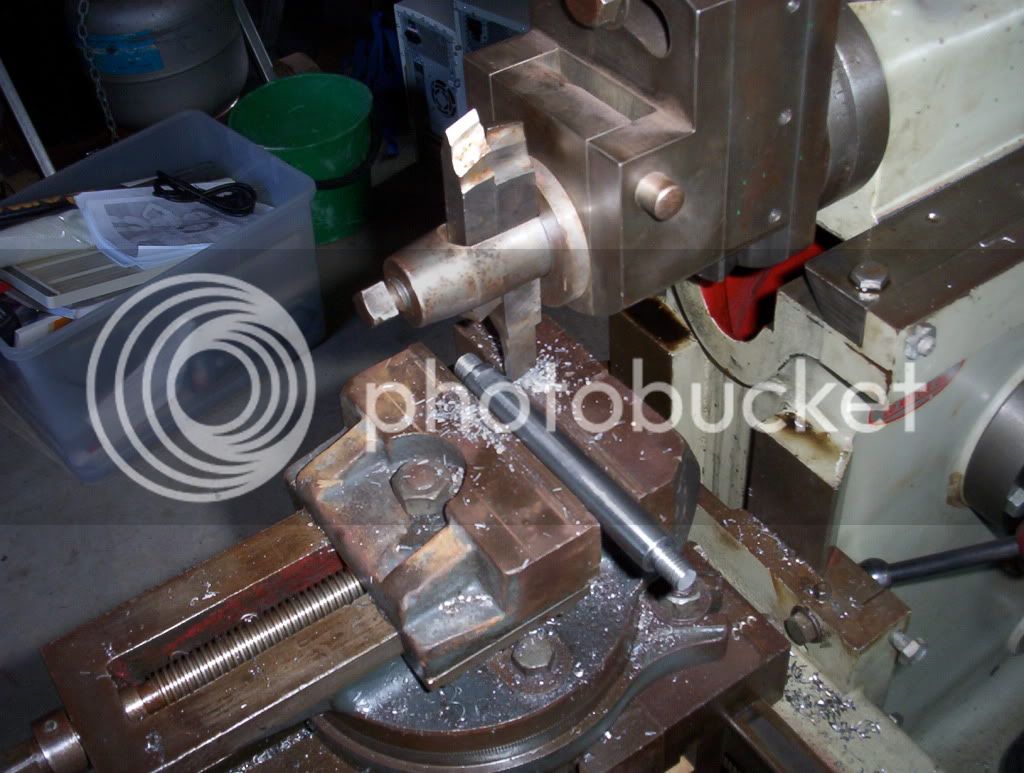
Some 1" bored and threaded for the ball handles
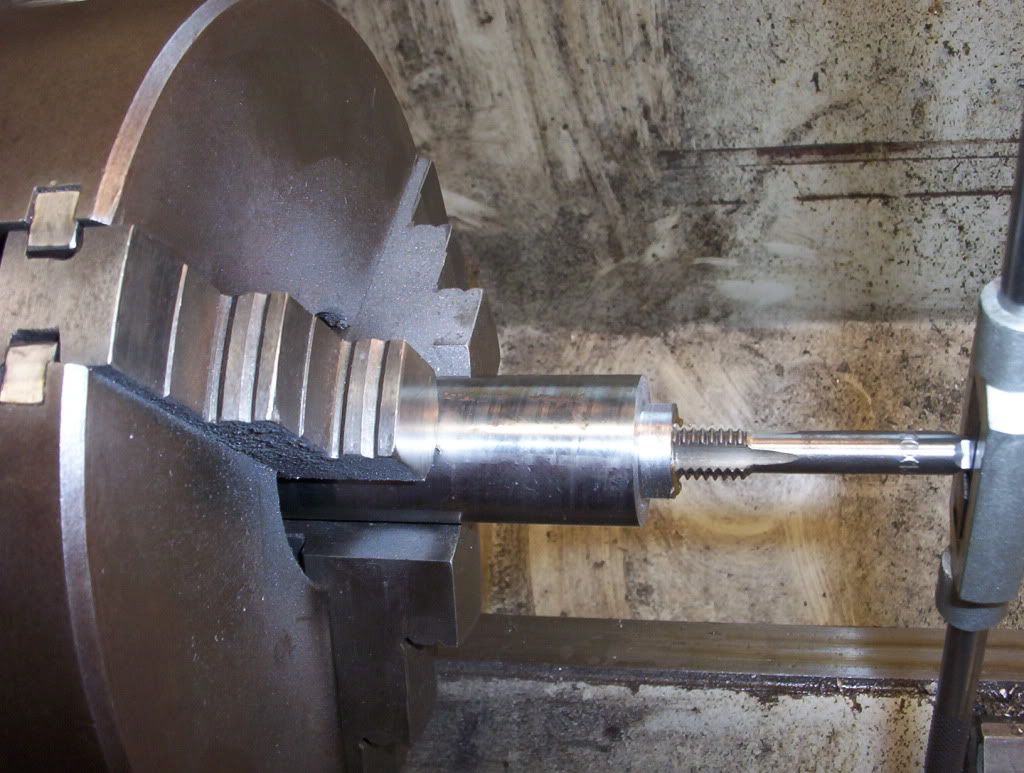
Generated co-ordinates to incremental cut the balls
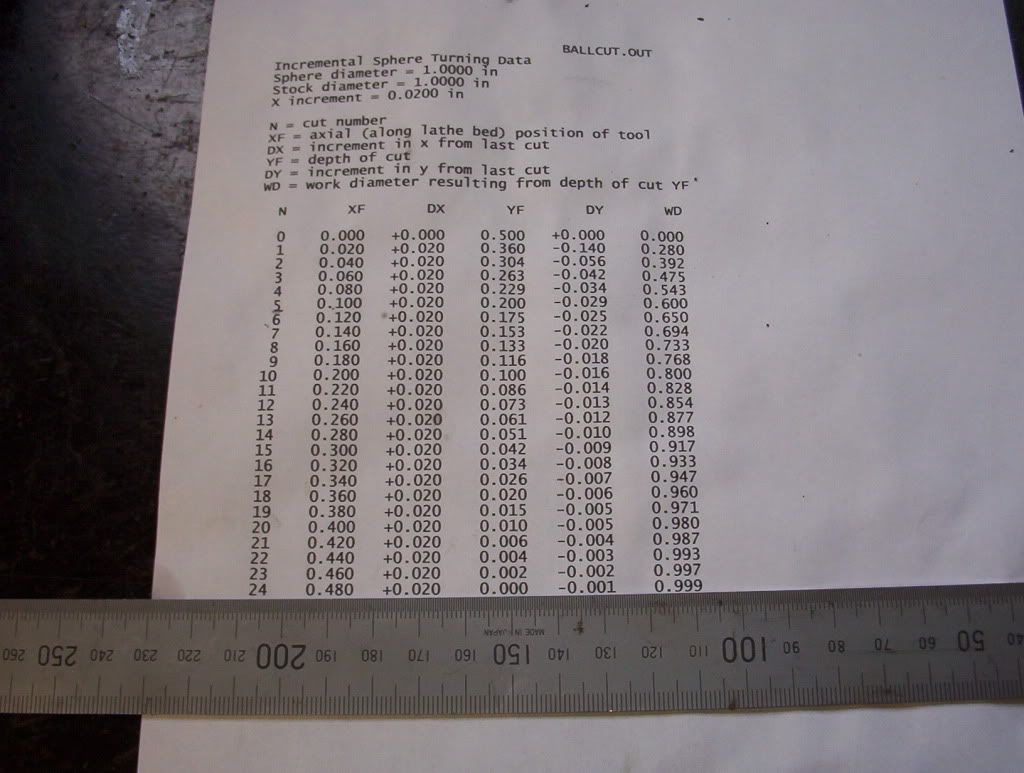