- Joined
- Dec 14, 2007
- Messages
- 1,181
- Reaction score
- 31
I made a couple of pieces for Paul's "Pug" which can be found in the uploads section and here;
http://www.homemodelenginemachinist.com/index.php?topic=5161.0
I'd like to have an engine running on my desk and allready have the pump.
I started with the cylinder and valve chest which I think I can make out one piece by drilling the valve holes and inserting plugs then bore the valve passage;
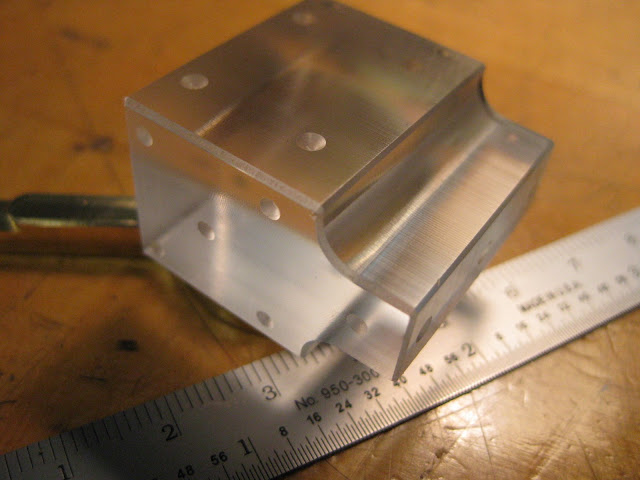
Then screwed a brass blank for the eccentric strap onto a sacrificial plate and faced it to thickness, Then roughed out the outer profile;
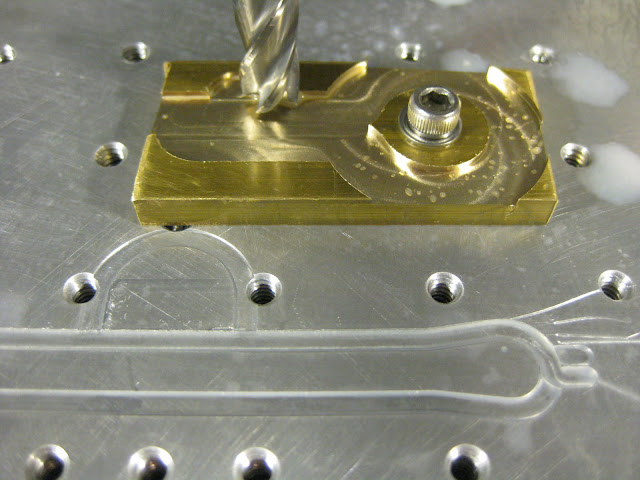
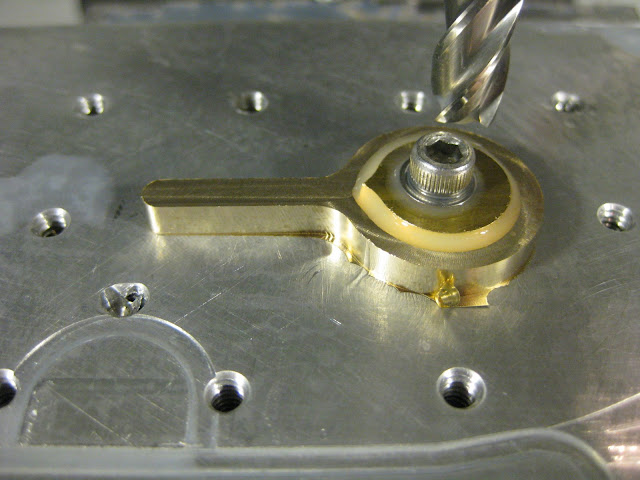
And finished the outside;
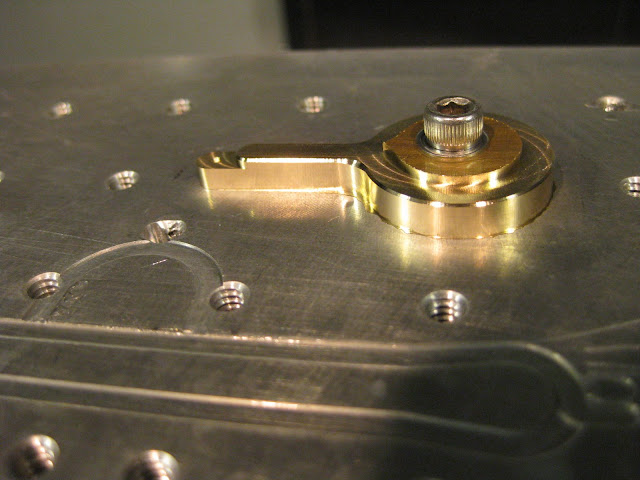
before removing the centre screw I installed clamps then milled out the ID;
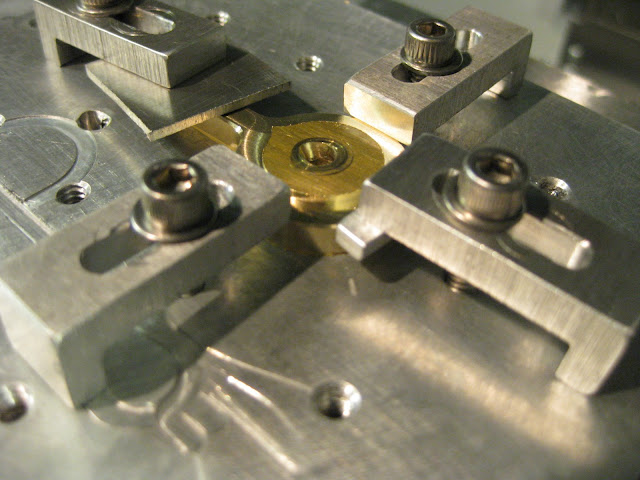
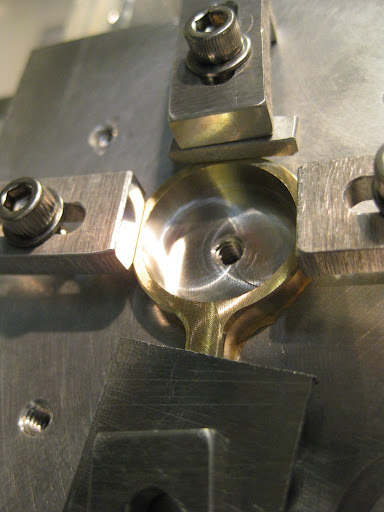
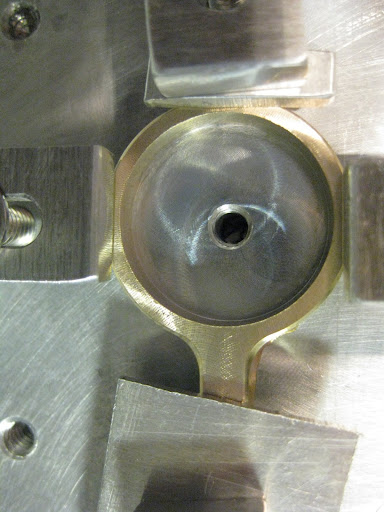
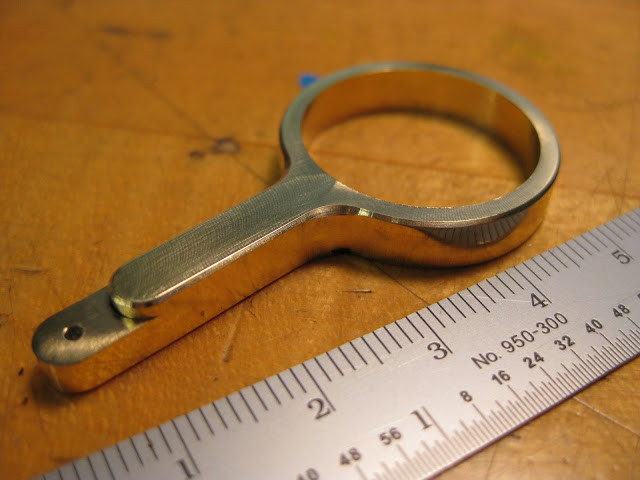
Next came the flywheel;
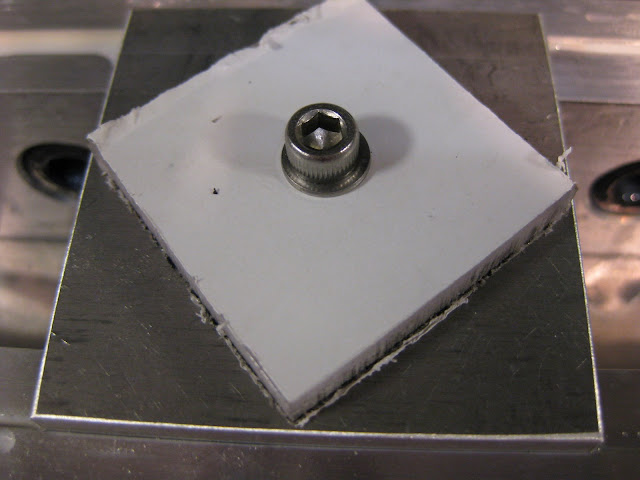

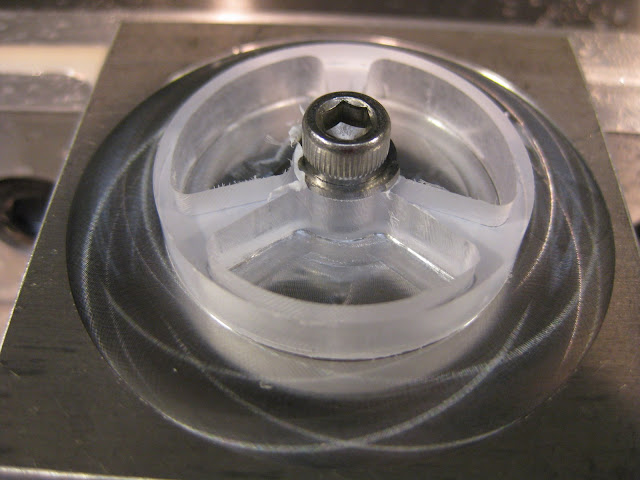

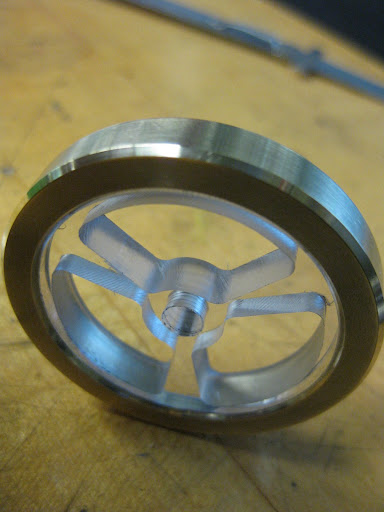
Thanks for the design Paul!
Have fun,
-Kevin.