With the intentions of lowering the minimum lathe speed, of 150rpm, and some serious doubts about where all this will lead, I machined a 25mm o.d. motor pulley in replacement of the stock 35mm o.d. stock one.
This is the tool I used to make it: that triangular insert was fitting the V groove into the original pulley so nicely I decided to give it a try by mounting it (look at the overhang ) into a toolholder I had made to hold rhombic ones.
With a bit of care, it worked.
Now I had the V groove and the 10mm hole, I tried to cut the keyway by broaching on the lathe. Definitely a no-go.
Either flex in the tool, the gummy material or else, I could make two or three .05mm passes and then got a dig-in.
Retract the tool, again .05mm passes till I got past the material raised by the dig-in, some steps forward, another dig in.
Getting to this point took hours, and the grove is still undersized and not deep enough.
When the going gets tough
Left: a 10mm holder for 6mm HSS mill shanks.
Center: 10mm dia. handle purposely made to aid sharpening very short HSS bits on the bench grinder.
Right: a recalcitrant pulley.
The first bit came out too little, the second was judged OK (but later I made a third)
A round base pres fitted square to the shank, to help keeping things straight and square
.the toughs (hydraulic press) get going
1 minute!!
Now I have the new pulley, I want to have the means of removing it, too.
Added a couple of horizontal tapped holes to the extractor I had made few days ago, to fit the holes drilled into the pulley
Among the doubts I had when I started this mod, I had one about the eventual capacity of the belt tightening mechanism of getting rid of the increased slack in the belts, due to the lower pulley diameter.
Was right about that: a quick trip to the nearest hardware store to buy a shorter belt did not help solving it, they had none readily available.
Had a second serious doubt, the one about the belt slipping on the pulley, due the much shorter contact area with the pulley, if compared with the original one.
I did not want to wait for a shorter belt to arrive.
Heres the parts of a free pulley purposely made (ball bearings graciously offered by a discarded laser printer)
Fitted in place.
While I was at it, I took the time to add a knurled ring to the tensioning screw (barely visible behind the large pulley on the left) and (it was about time!!) a hinge to the gear cover.
Time to test the mod.
As I had feared, as soon as I took the cutting loads above a (very low) minimum, I had the chuck stopping and belt slipping sounds coming from the gear end of the lathe.
Had I drilled the hole for the free pulley a few millimeters further on the left, things would probably be OK, as the primary and secondary belts have definitely different tensions.
The quicker solution came through machining another free pulley, of larger diameter.
With that, I could successfully part off the Bernay heads from their 45 mm steel rod at about 2/3 of the previous minimum speed.
Marcello
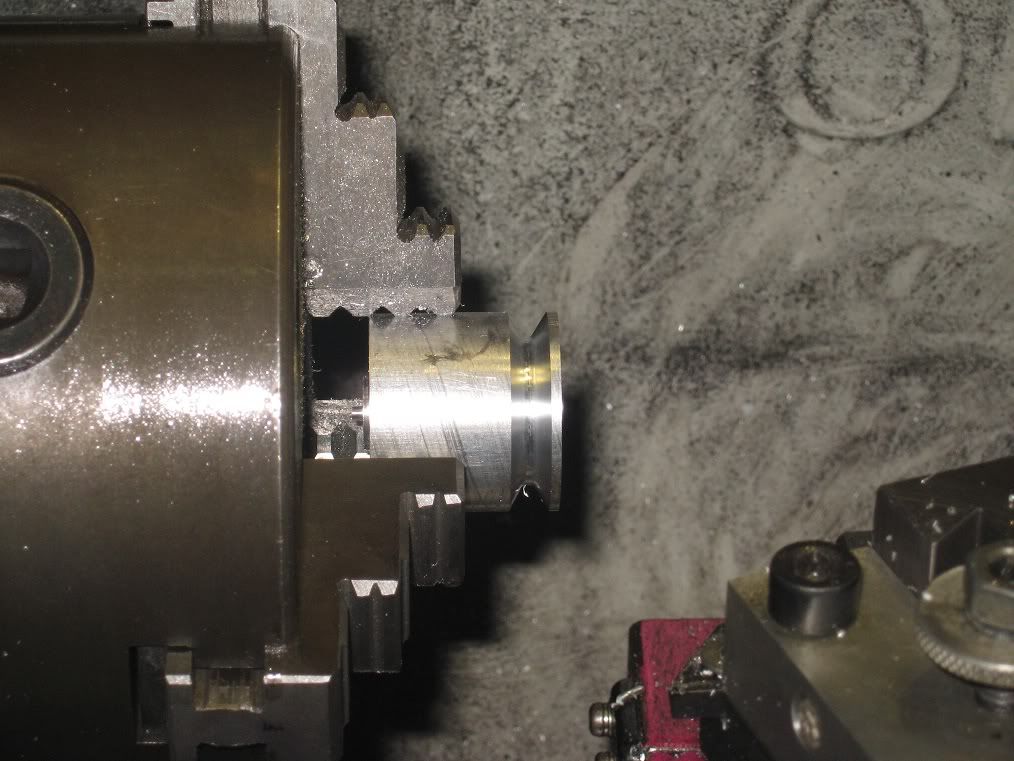
This is the tool I used to make it: that triangular insert was fitting the V groove into the original pulley so nicely I decided to give it a try by mounting it (look at the overhang ) into a toolholder I had made to hold rhombic ones.
With a bit of care, it worked.
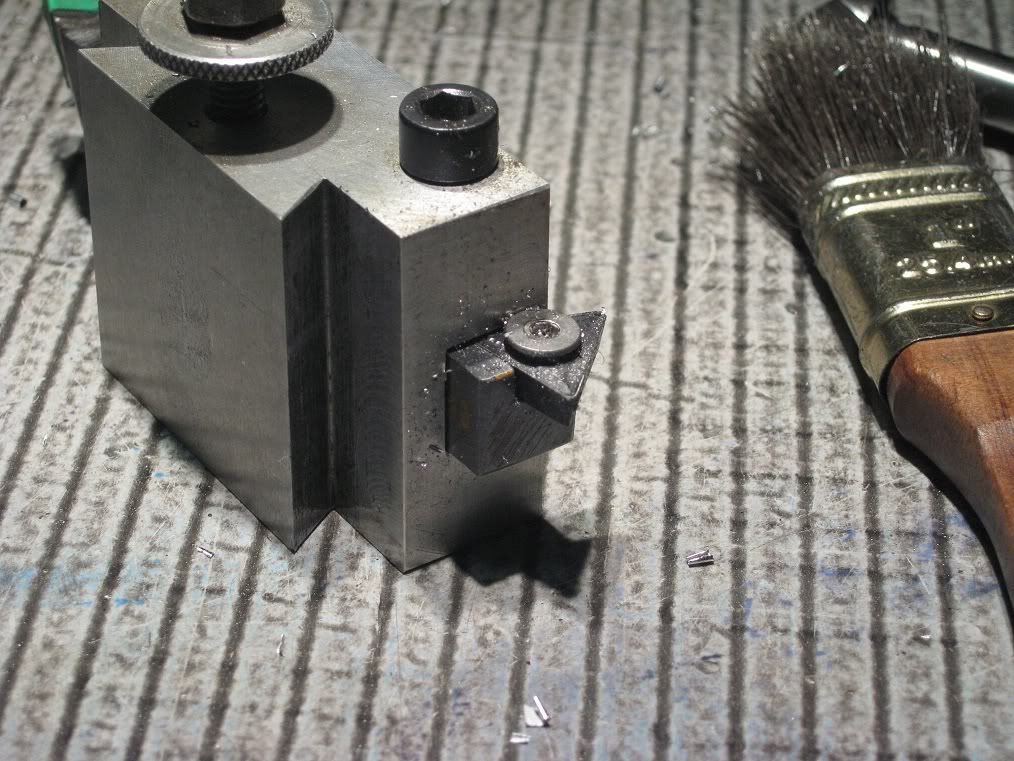
Now I had the V groove and the 10mm hole, I tried to cut the keyway by broaching on the lathe. Definitely a no-go.
Either flex in the tool, the gummy material or else, I could make two or three .05mm passes and then got a dig-in.
Retract the tool, again .05mm passes till I got past the material raised by the dig-in, some steps forward, another dig in.
Getting to this point took hours, and the grove is still undersized and not deep enough.
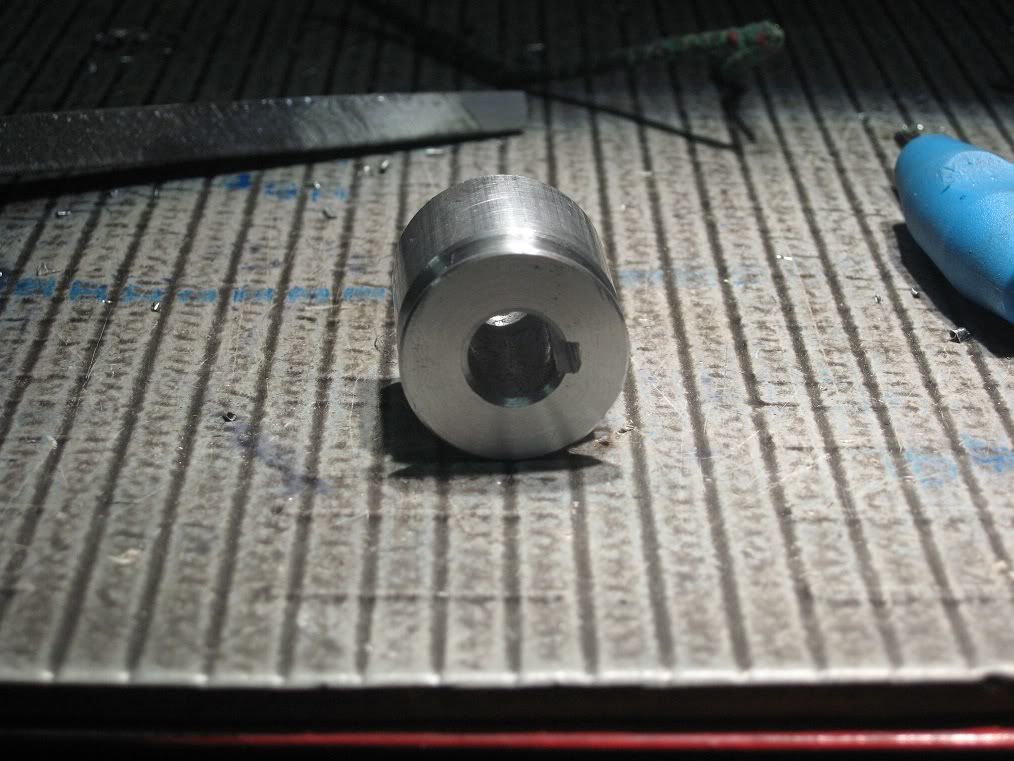
When the going gets tough
Left: a 10mm holder for 6mm HSS mill shanks.
Center: 10mm dia. handle purposely made to aid sharpening very short HSS bits on the bench grinder.
Right: a recalcitrant pulley.
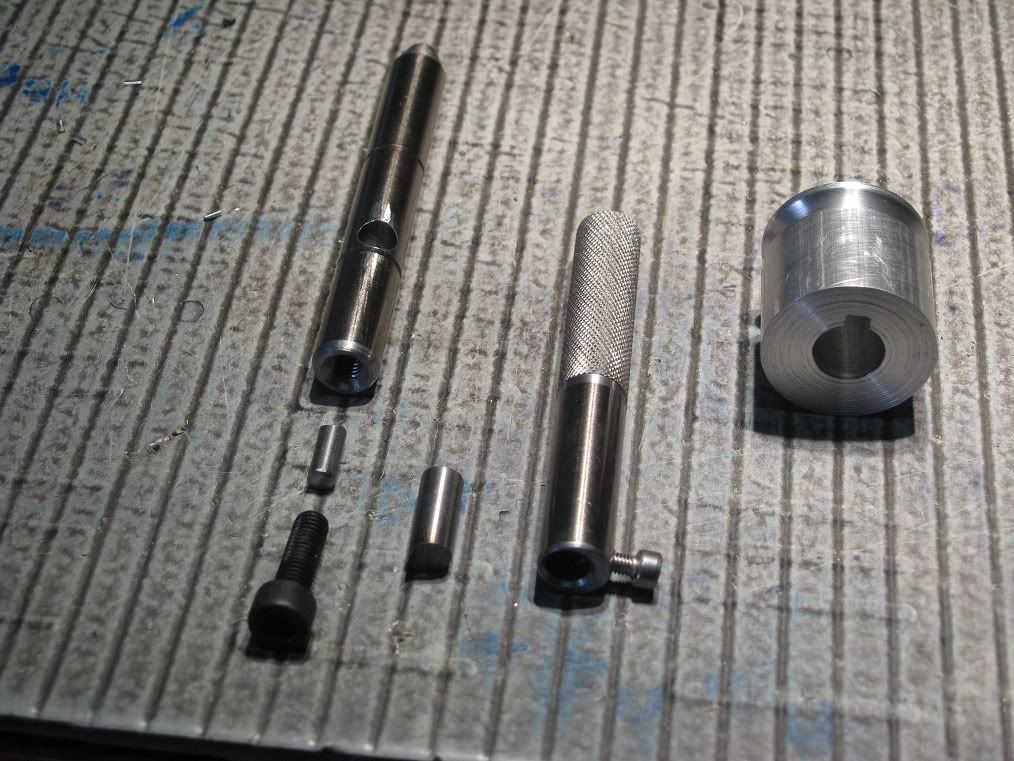
The first bit came out too little, the second was judged OK (but later I made a third)
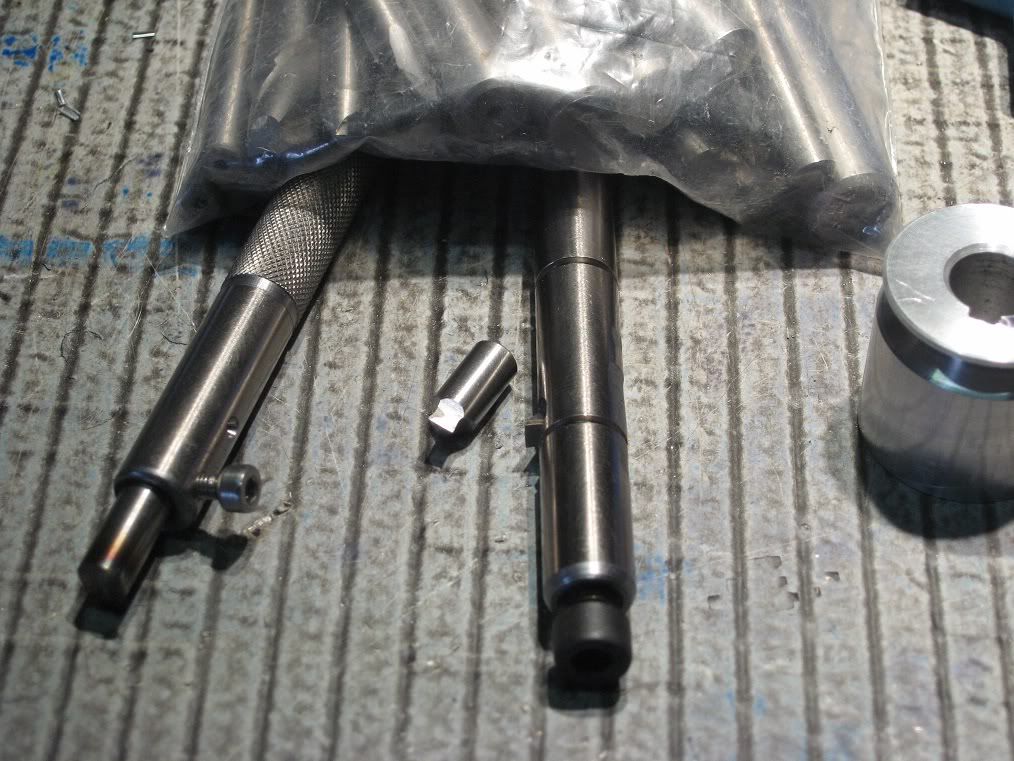
A round base pres fitted square to the shank, to help keeping things straight and square
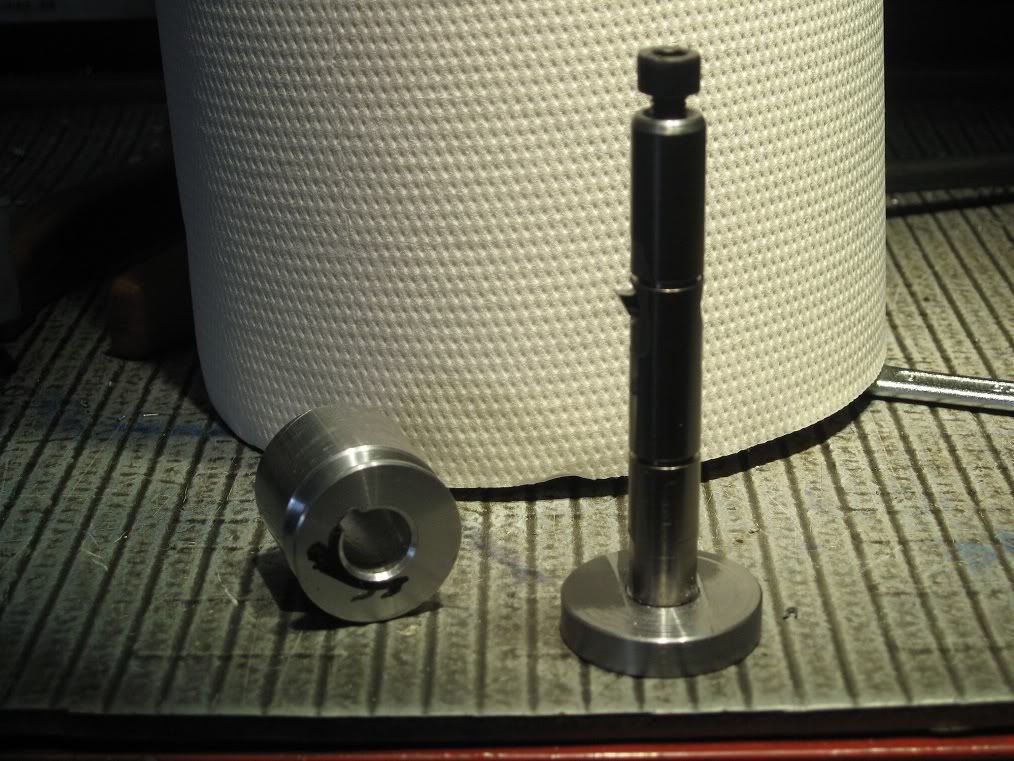
.the toughs (hydraulic press) get going
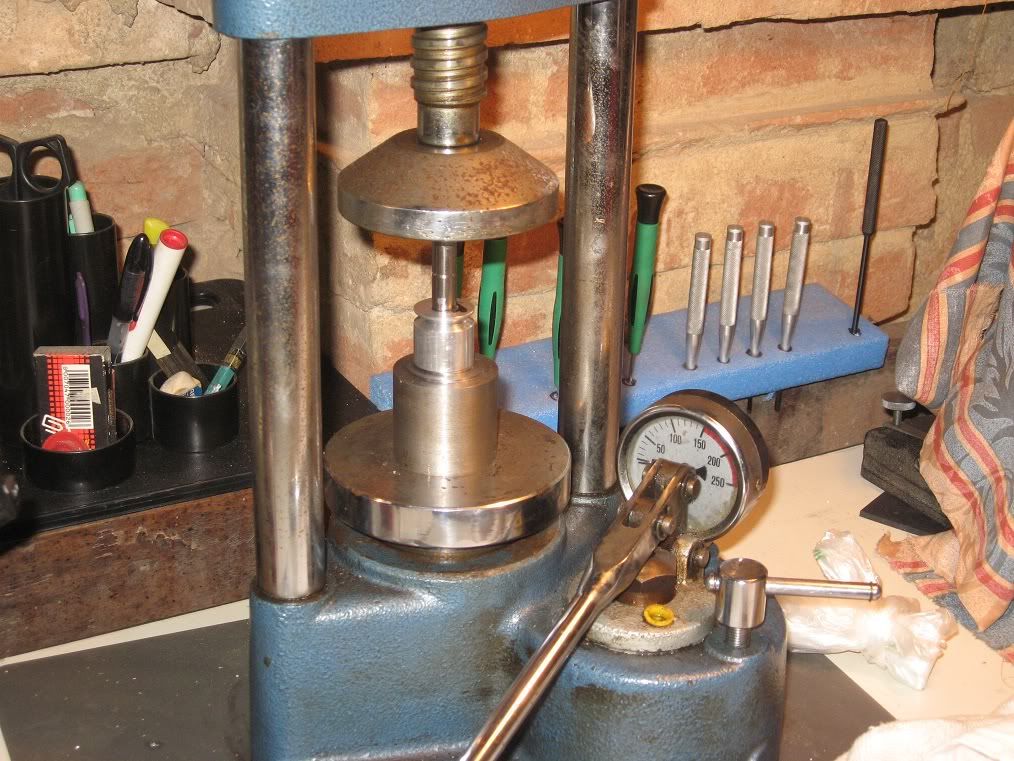
1 minute!!
Now I have the new pulley, I want to have the means of removing it, too.
Added a couple of horizontal tapped holes to the extractor I had made few days ago, to fit the holes drilled into the pulley
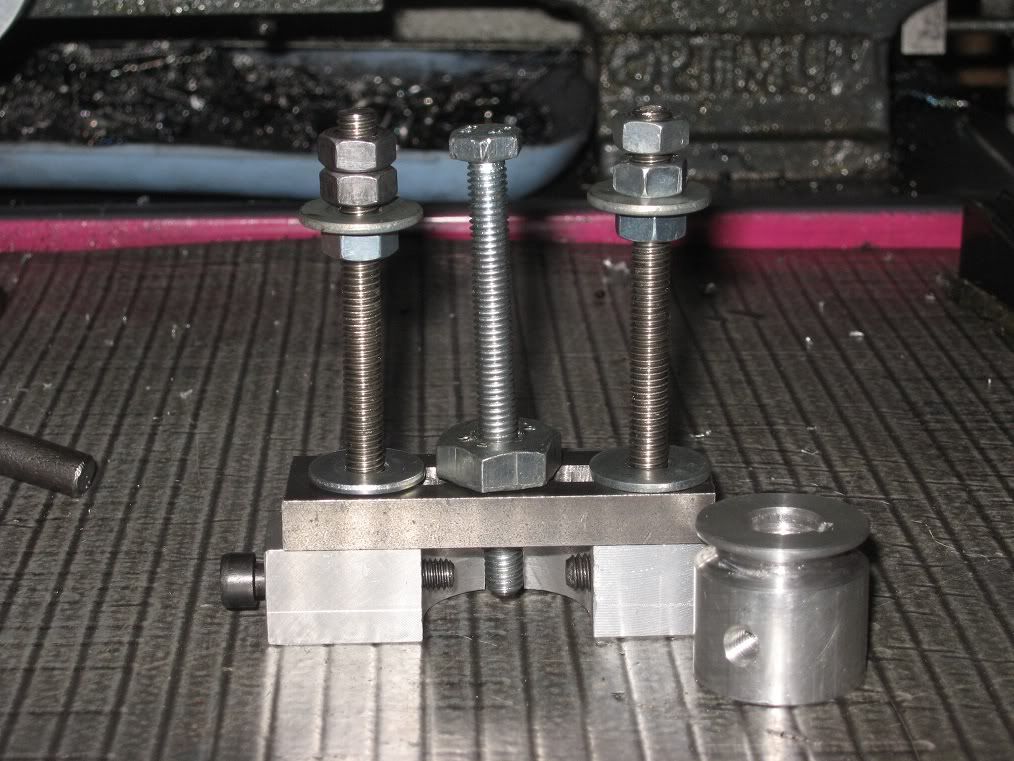
Among the doubts I had when I started this mod, I had one about the eventual capacity of the belt tightening mechanism of getting rid of the increased slack in the belts, due to the lower pulley diameter.
Was right about that: a quick trip to the nearest hardware store to buy a shorter belt did not help solving it, they had none readily available.
Had a second serious doubt, the one about the belt slipping on the pulley, due the much shorter contact area with the pulley, if compared with the original one.
I did not want to wait for a shorter belt to arrive.
Heres the parts of a free pulley purposely made (ball bearings graciously offered by a discarded laser printer)
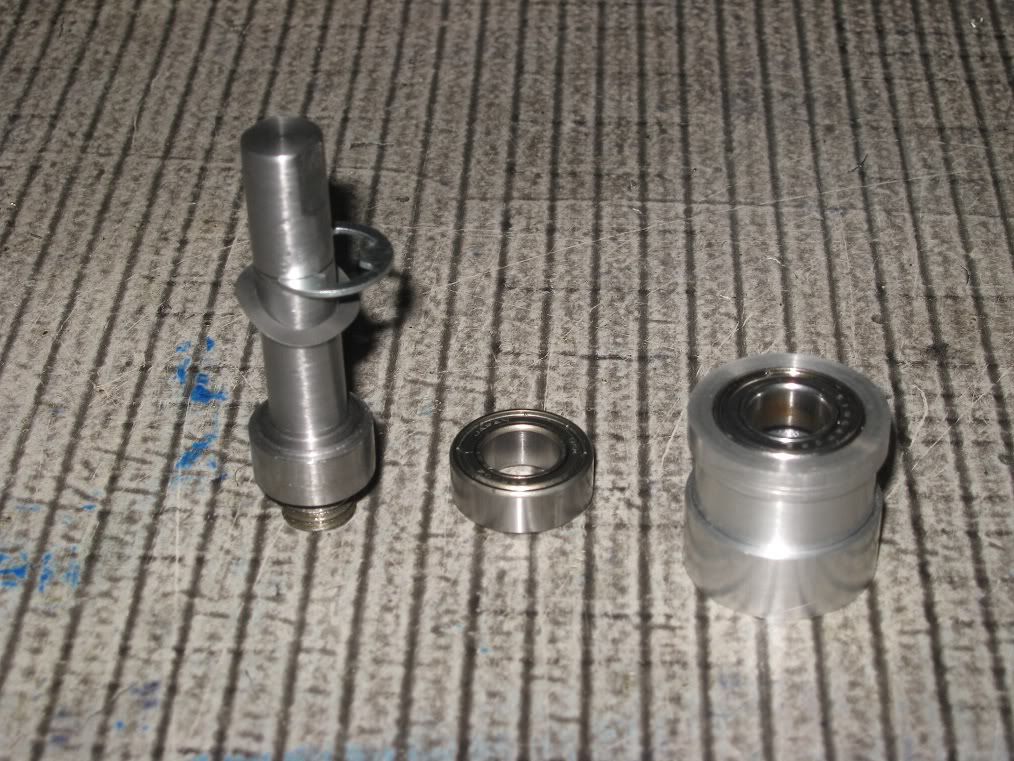
Fitted in place.
While I was at it, I took the time to add a knurled ring to the tensioning screw (barely visible behind the large pulley on the left) and (it was about time!!) a hinge to the gear cover.
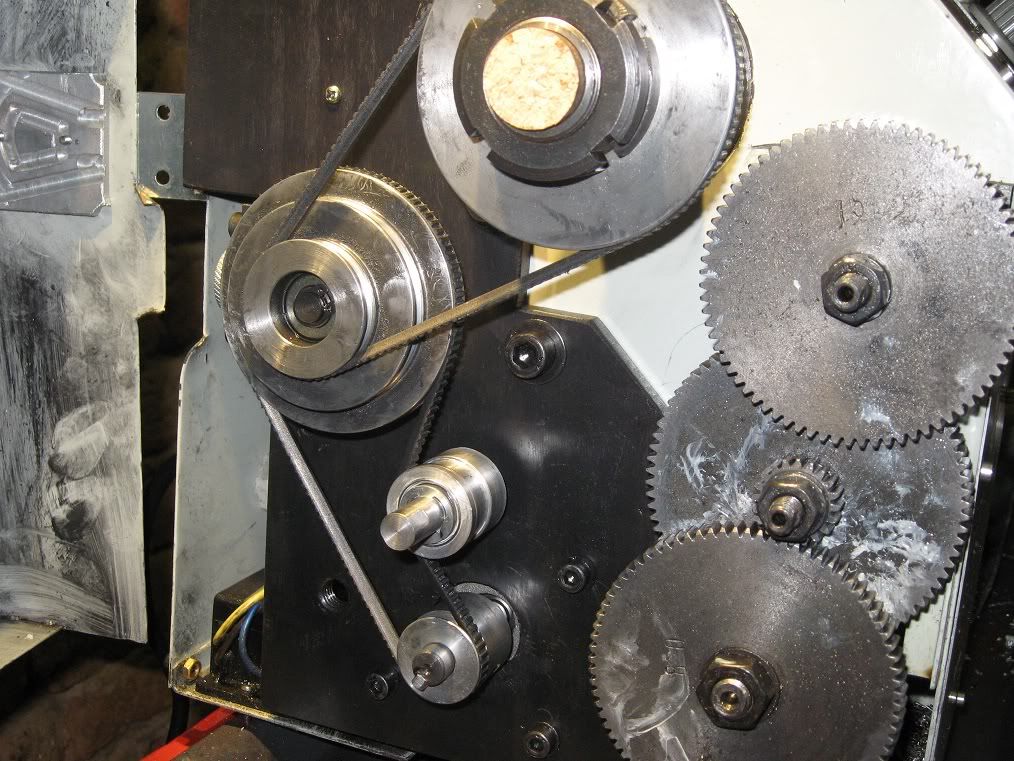
Time to test the mod.
As I had feared, as soon as I took the cutting loads above a (very low) minimum, I had the chuck stopping and belt slipping sounds coming from the gear end of the lathe.
Had I drilled the hole for the free pulley a few millimeters further on the left, things would probably be OK, as the primary and secondary belts have definitely different tensions.
The quicker solution came through machining another free pulley, of larger diameter.
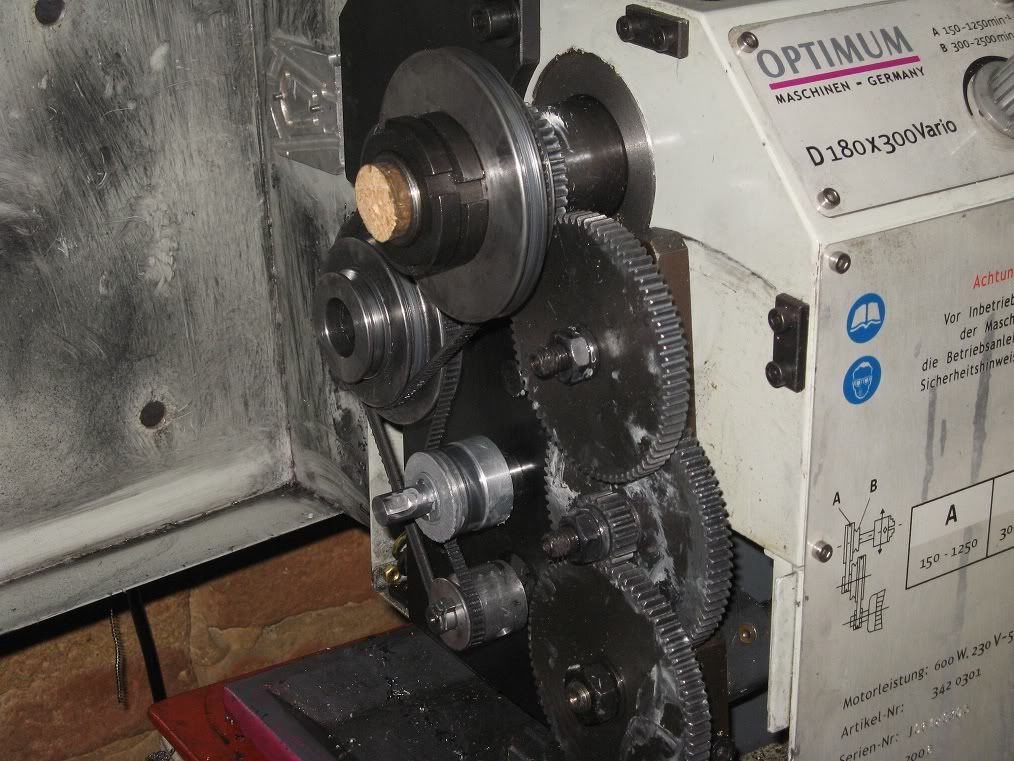
With that, I could successfully part off the Bernay heads from their 45 mm steel rod at about 2/3 of the previous minimum speed.
Marcello