I hope I'm getting this is the right place....
I'm just getting started on the 10V. I don't have a mill, so I'm doing the facing in the lathe. It took a long time because my four jaw chuck is not turning true. I found I had to do a lot of shimming and ended up finishing the soleplate on the face plate after I trued it up. I lapped the top and bottom surfaces.
Next up, I have to prepare the bearing seats. The book suggests doing it with a file but I don't look forward to that and welcome any suggestions.
I'm just getting started on the 10V. I don't have a mill, so I'm doing the facing in the lathe. It took a long time because my four jaw chuck is not turning true. I found I had to do a lot of shimming and ended up finishing the soleplate on the face plate after I trued it up. I lapped the top and bottom surfaces.
Next up, I have to prepare the bearing seats. The book suggests doing it with a file but I don't look forward to that and welcome any suggestions.
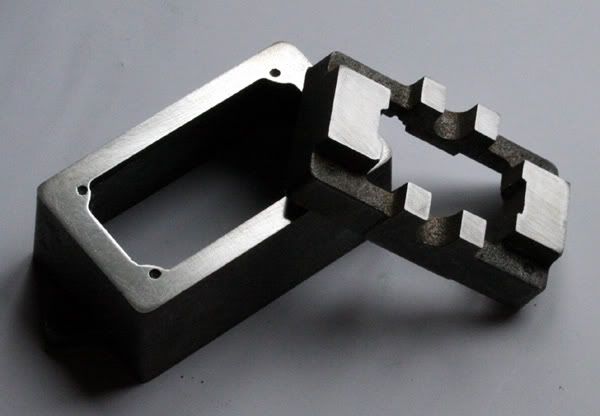