CallMeAL
Member
- Joined
- Mar 29, 2008
- Messages
- 118
- Reaction score
- 40
Well to celebrate the 4th, I cranked up the foundry and poured the base for my 3rd engine project (I'm not counting the exploding finger engine for the recent contest). 
I turned out OK, considering there wasn't much in draft angles in a few places. Also, didn't get much in the way of porosities.
This whole engine being designed around a piece I found at the scrap yard! :
Here is the wood pattern:
Here is the cast base fresh from the flasks with sprues cut off. Needs a little clean up:
I should make some progress this 3 day weekend and will post more...
Have a great 4th!!
The other Al
I turned out OK, considering there wasn't much in draft angles in a few places. Also, didn't get much in the way of porosities.
This whole engine being designed around a piece I found at the scrap yard! :
Here is the wood pattern:
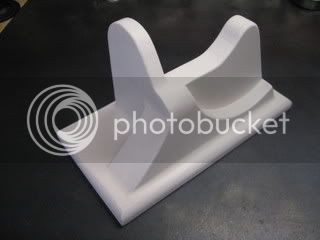
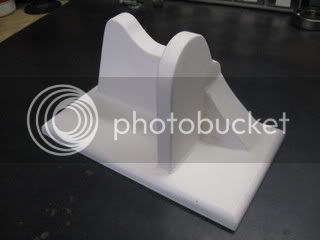
Here is the cast base fresh from the flasks with sprues cut off. Needs a little clean up:
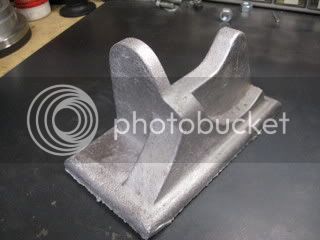
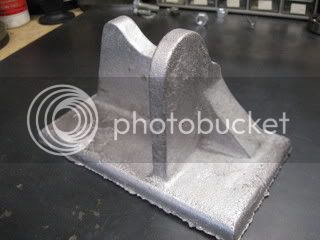
I should make some progress this 3 day weekend and will post more...
Have a great 4th!!
The other Al