I just discover this little trick:
This work when you have a irregular piece and make a first cut in one face, and want to cut to 90° the next face
1) put the piece in the vise and tighten just a little to prevent the piece from falling, but make sure you still can move the piece in the jaws (with reasonable strength)
then put the machinist square in the bottom of the vise (make sure to clean with a finger the bottom of the vise to remove chips and dust), then push the square against the bottom to make sure that the surfaces are in full contact.
2) now move the square to the right with a 45° degree force vector, this prevent a loose of alineation between the square and the vise bottom
move the square until reach the piece and start to push it, move all the necesary way to make sure that all the straight edge is in full contact with the square, in this point start to tighten the vise slowly until you cant push the piece no more with the square, then full tight the vise
now your workpiece is in 90° respect the previus cut, and in just a seconds
dont know if a common practice , but is very usefull! at least for me ;D
saludos!
This work when you have a irregular piece and make a first cut in one face, and want to cut to 90° the next face
1) put the piece in the vise and tighten just a little to prevent the piece from falling, but make sure you still can move the piece in the jaws (with reasonable strength)
then put the machinist square in the bottom of the vise (make sure to clean with a finger the bottom of the vise to remove chips and dust), then push the square against the bottom to make sure that the surfaces are in full contact.
2) now move the square to the right with a 45° degree force vector, this prevent a loose of alineation between the square and the vise bottom
move the square until reach the piece and start to push it, move all the necesary way to make sure that all the straight edge is in full contact with the square, in this point start to tighten the vise slowly until you cant push the piece no more with the square, then full tight the vise
now your workpiece is in 90° respect the previus cut, and in just a seconds
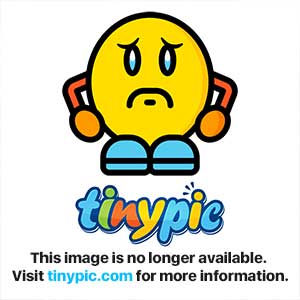
dont know if a common practice , but is very usefull! at least for me ;D
saludos!