Tormach CNC Mill
Experience level: none
I want to build a Stirling. I've got the plans from Jan Ridders and the more I looked at them the more I realized how much I don't know. I decided to start with Machinists wax and post the process here in hopes I will hear a better way of doing things.
Here is a pic of day one:
My steps today were:
Cut a 1" thick block of wax
One side was flat to I put it flat side down, in a vice, and faced a 0.0100" off of the uneven side to even it up. That was enough to take a bit off of the entire surface.
I then worked in a CAD program and cut what you see.
My plan for the next steps are:
Turn it over in the vice (using the center hole for alignment) and face down until it matches the first side. I cut the gaps between the spokes full depth so I would not have to worry about them not lining up.
I guess then I will have to carefully mount it independent of the vice so I can make the big circular cut and allow the stock material to fall away. This seems weird but I don't see another way?
Experience level: none
I want to build a Stirling. I've got the plans from Jan Ridders and the more I looked at them the more I realized how much I don't know. I decided to start with Machinists wax and post the process here in hopes I will hear a better way of doing things.
Here is a pic of day one:
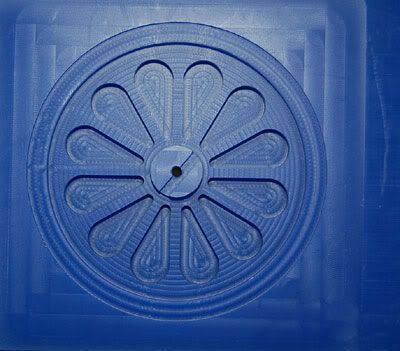
My steps today were:
Cut a 1" thick block of wax
One side was flat to I put it flat side down, in a vice, and faced a 0.0100" off of the uneven side to even it up. That was enough to take a bit off of the entire surface.
I then worked in a CAD program and cut what you see.
My plan for the next steps are:
Turn it over in the vice (using the center hole for alignment) and face down until it matches the first side. I cut the gaps between the spokes full depth so I would not have to worry about them not lining up.
I guess then I will have to carefully mount it independent of the vice so I can make the big circular cut and allow the stock material to fall away. This seems weird but I don't see another way?