BobWarfield
Well-Known Member
- Joined
- Dec 27, 2007
- Messages
- 1,151
- Reaction score
- 1
I confess: most of the time I slap the workpiece in the Kurt Vise and go for it. Usually it works. An exotic setup for me would be using a v-block to clamp a round in the vise, or getting really exotic would be to drag out my 5C collet blocks. Recently I was working on the table for my disc sander and needed to expand my repertoire. One setup worked well and the other didn't. First thing to note is this is a job machining plate, which can be awkward.
Let's start with the setup that worked. In order to finish the long edges of the table, I clamped the plate vertically in my vise:
The 2-4-6 blocks help support things better. Before I had them I did some platework and noticed how badly the edges could ring or vibrate if you couldn't support them. The big blocks were a good purchase, and this was a trick I learned from the Widgitmaster over on CNCZone.
Now for the setup that didn't work so well. I wanted to mill a 45 degree bevel on one edge to act as a relief when I tilt the table. Dickeybird did something similar on his sander:
He had a nice tilting table setup ala Mr Ishimura. Lacking such niceties and not wanting to start yet another project before finishing my sander, I looked at what I had. I could tram the mill head 45 degrees, but I lack enough Y-travel for one pass, so it would be a real pain to get it to come out well. My next thought was to use an indexable chamfering cutter. The TPG inserts produced a really nasty finish and it was going to take forever to get a big enough chamfer too. So, I came up with the brilliant idea of using some big ole v-blocks I had and some Kant-Twist clamps:
This appeared to work fine right up until it didn't. Two bad things got me this result:
The first bad thing is that an endmill is a screw that exerts a vertical upward force. You can see the edge is uneven because the plate shifted. This led to the next bad thing which is that I didn't have a good enough clamping surface and the shift eventually caused the Kant-Twist clamps to pop loose, which led to the gouges. DOH!
This was not for lack of torque nor for being too aggressive on the feeds and speeds. In all, I had the plate slip twice and I set it up 3 times before I got through the process holding my breath on the final light passes.
What would I do differently?
Ideally, I'd have a tilting table like Dickeybird's. Plan B would be to deal with tramming the head over and fooling around. Plan C was to drill and tap the V-blocks. That probably would have worked out okay, but I was too impatient. Plan D (yes, lots of time for analysis after the emergency has passed!) would have been to make a special set of jaws for the Kurt to hold the plate the way I have it with the v-blocks. I rather liked that last concept and went looking for a block of aluminum, but alas I had none big enough. Maybe next time.
All ended reasonably well as I cut the table:
It's a nice heavy table that has a "machine tool feel" about it. I did the tooling slot to match the slot on my HF tool grinder so I can exchange tooling between the two. I wish I had my Blanchard grinder going as a nice ground finish on the table would be the icing on the cake. All in good time, LOL!
Cheers,
BW
Let's start with the setup that worked. In order to finish the long edges of the table, I clamped the plate vertically in my vise:
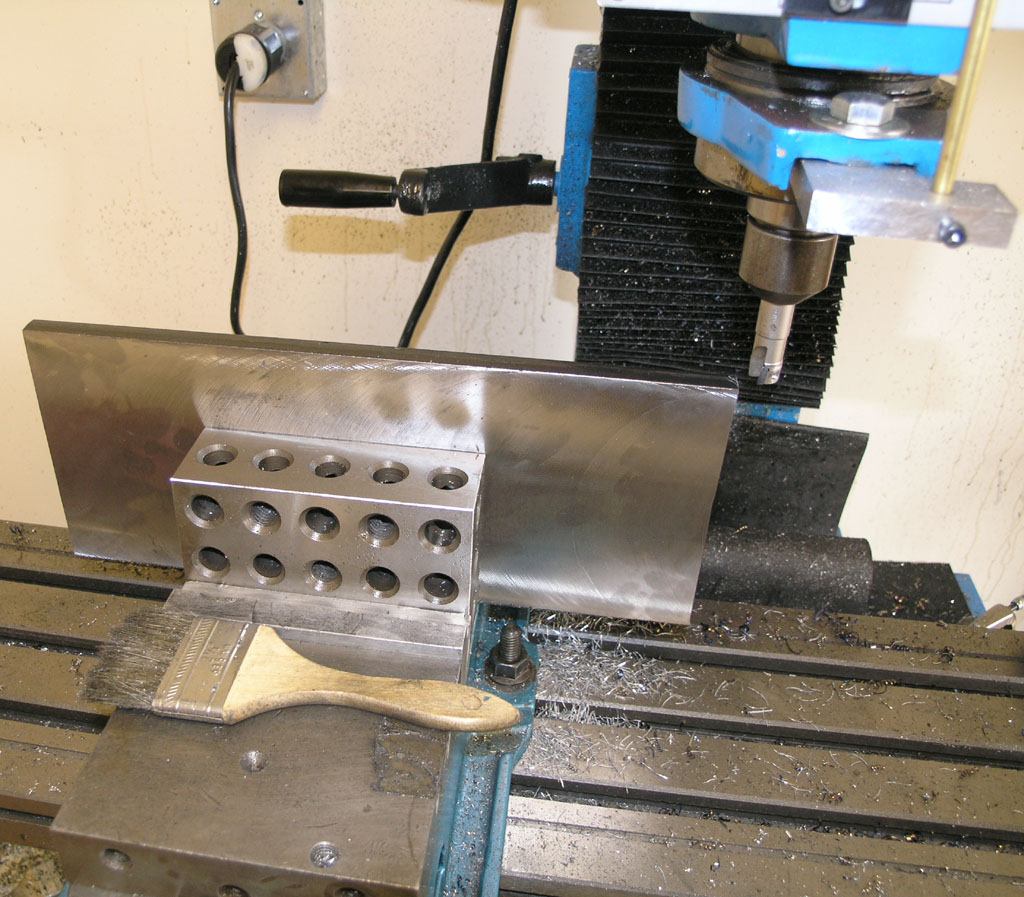
The 2-4-6 blocks help support things better. Before I had them I did some platework and noticed how badly the edges could ring or vibrate if you couldn't support them. The big blocks were a good purchase, and this was a trick I learned from the Widgitmaster over on CNCZone.
Now for the setup that didn't work so well. I wanted to mill a 45 degree bevel on one edge to act as a relief when I tilt the table. Dickeybird did something similar on his sander:
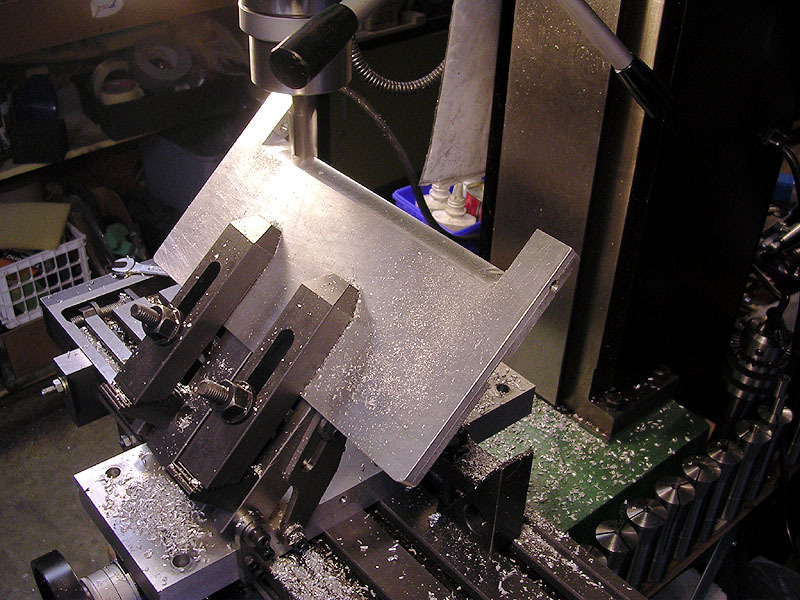
He had a nice tilting table setup ala Mr Ishimura. Lacking such niceties and not wanting to start yet another project before finishing my sander, I looked at what I had. I could tram the mill head 45 degrees, but I lack enough Y-travel for one pass, so it would be a real pain to get it to come out well. My next thought was to use an indexable chamfering cutter. The TPG inserts produced a really nasty finish and it was going to take forever to get a big enough chamfer too. So, I came up with the brilliant idea of using some big ole v-blocks I had and some Kant-Twist clamps:

This appeared to work fine right up until it didn't. Two bad things got me this result:

The first bad thing is that an endmill is a screw that exerts a vertical upward force. You can see the edge is uneven because the plate shifted. This led to the next bad thing which is that I didn't have a good enough clamping surface and the shift eventually caused the Kant-Twist clamps to pop loose, which led to the gouges. DOH!
This was not for lack of torque nor for being too aggressive on the feeds and speeds. In all, I had the plate slip twice and I set it up 3 times before I got through the process holding my breath on the final light passes.
What would I do differently?
Ideally, I'd have a tilting table like Dickeybird's. Plan B would be to deal with tramming the head over and fooling around. Plan C was to drill and tap the V-blocks. That probably would have worked out okay, but I was too impatient. Plan D (yes, lots of time for analysis after the emergency has passed!) would have been to make a special set of jaws for the Kurt to hold the plate the way I have it with the v-blocks. I rather liked that last concept and went looking for a block of aluminum, but alas I had none big enough. Maybe next time.
All ended reasonably well as I cut the table:

It's a nice heavy table that has a "machine tool feel" about it. I did the tooling slot to match the slot on my HF tool grinder so I can exchange tooling between the two. I wish I had my Blanchard grinder going as a nice ground finish on the table would be the icing on the cake. All in good time, LOL!
Cheers,
BW