Darren English
Member
- Joined
- Apr 27, 2012
- Messages
- 70
- Reaction score
- 8
After looking around the site, asking a few questions and searching the net I've decided to make J. Jonkman's Stirling 60 as my first engine.
Had a hunt around the workshop today and found some materials so I made a start.
this is the smallest lathe i have at work so this is what I'll be using for most of the turning work
This is what I'll be using for most of my milling
power cylinder after turning and with bore
My first finished components of the project, I'm getting a bit excited now!
You'll have to excuse the large pictures, can't work out how to re-size pics in photobucket yet.
Had a hunt around the workshop today and found some materials so I made a start.
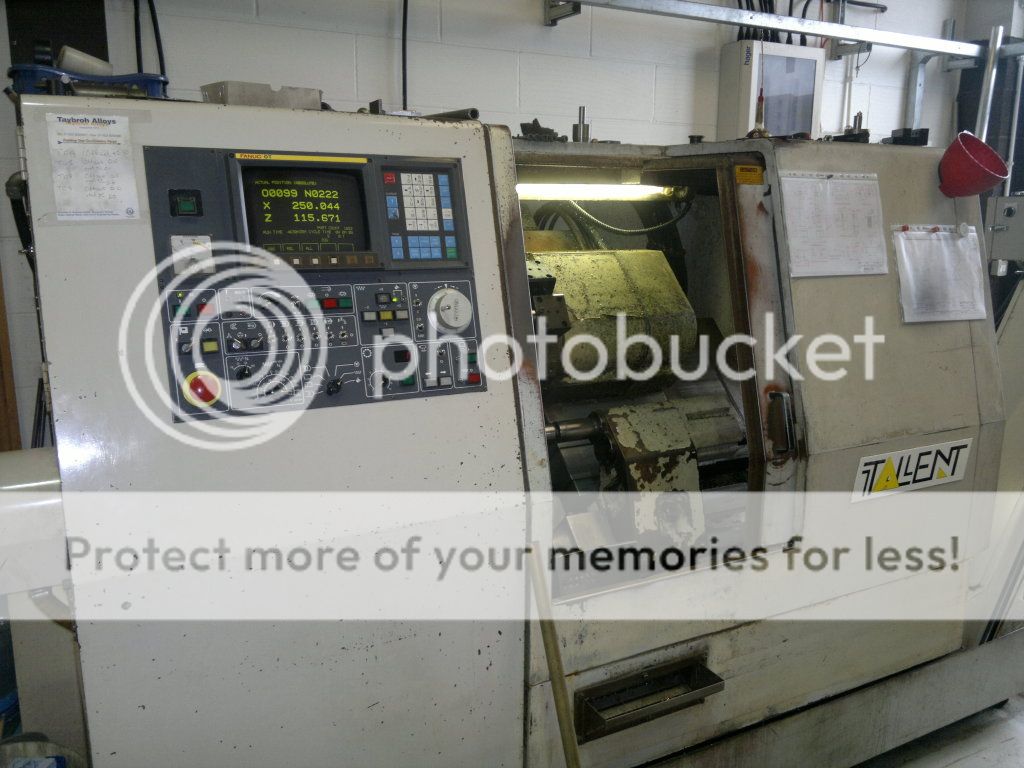
this is the smallest lathe i have at work so this is what I'll be using for most of the turning work
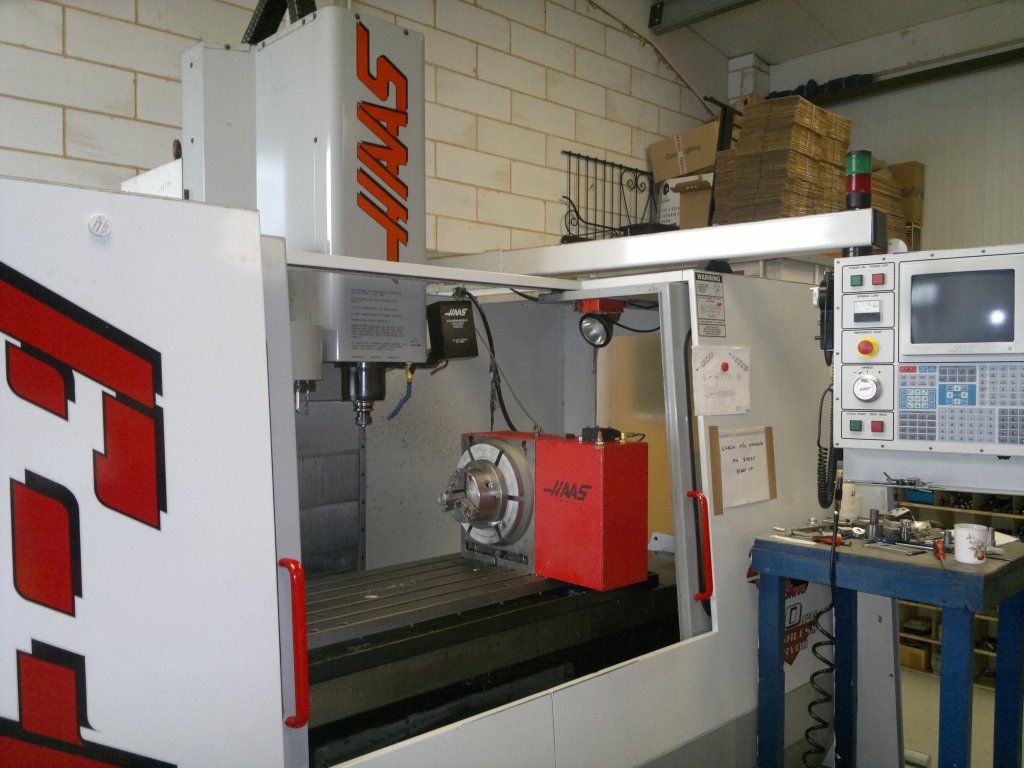
This is what I'll be using for most of my milling
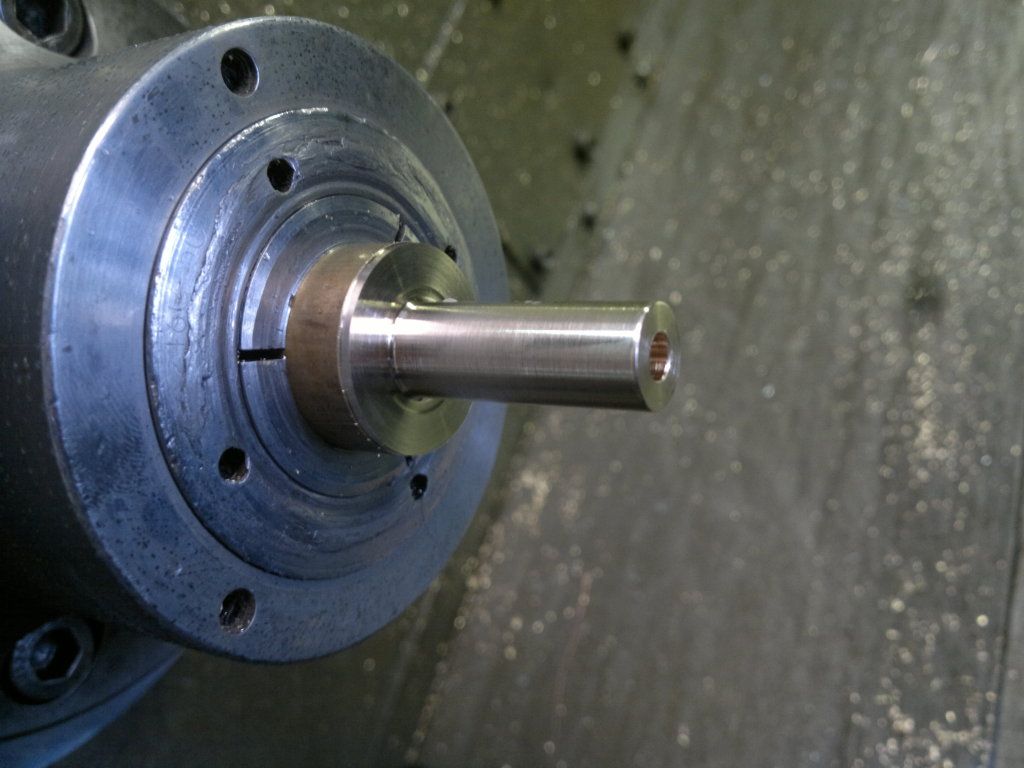
power cylinder after turning and with bore
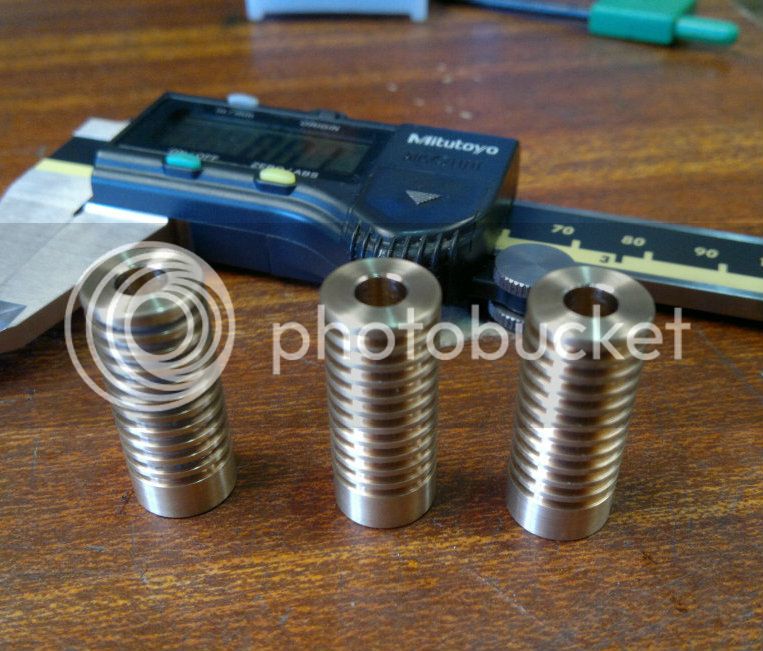
My first finished components of the project, I'm getting a bit excited now!
You'll have to excuse the large pictures, can't work out how to re-size pics in photobucket yet.