I have a milling machine but my dad does not. He had been talking about buying a milling attachment for his lathe and I took it as a good opportunity to make a gift and test my skills as well as learn something new. My first engine was the MLA-17 (barstock model diesel) so I was aware of the milling attachment kit offered by "Metal Lathe Accessories".
Side note:
This little business is run by Andy Lofquist. As a side note his kits are very nice and he has been very helpful to me on several occasions. He is usually at "Cabin Fever" and "NAMES". I have no business connection with him. I am just a satisfied customer.
http://www.statecollegecentral.com/metallathe/index.html
Back to the regulary scheduled program -
Following are some images of the raw castings as received. These are nice, heavy, cast iron casting with enough material for machining. I have not included any pictures on the plans, but they are very nice large size plans. He also includes some notes and suggestions to help during the build.
I must apologize at this point. I didn't take as many pictures during the build as I should have. I get caught up in the build and forget about documenting the process.

NOTE: More to come in a couple of minutes. The attachment is done but I'm just now getting to post info to the web.
Side note:
This little business is run by Andy Lofquist. As a side note his kits are very nice and he has been very helpful to me on several occasions. He is usually at "Cabin Fever" and "NAMES". I have no business connection with him. I am just a satisfied customer.
http://www.statecollegecentral.com/metallathe/index.html
Back to the regulary scheduled program -
Following are some images of the raw castings as received. These are nice, heavy, cast iron casting with enough material for machining. I have not included any pictures on the plans, but they are very nice large size plans. He also includes some notes and suggestions to help during the build.
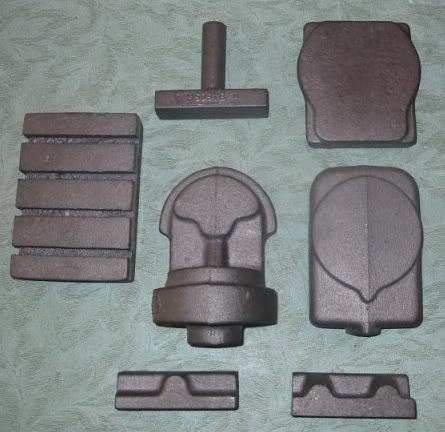
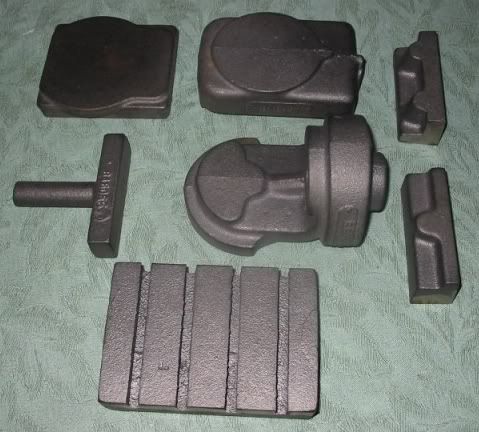
I must apologize at this point. I didn't take as many pictures during the build as I should have. I get caught up in the build and forget about documenting the process.
NOTE: More to come in a couple of minutes. The attachment is done but I'm just now getting to post info to the web.