deere_x475guy
Well-Known Member
Hi everyone, I need your help here. I am going to machine the connecting rod next for my Webster engine. I am having trouble getting it in my head how I am going to machine this part. I have looked at the plans dozens of times and just cant picture what I am going to do with it. I have a rotary table, and figure I will be using it and the mill. Or face plate on the lathe? Or a combo of both mill work and lathe work. How about posting some ideas to help my lost thinking out here? Any pics of set-ups, work holding or drawings will help, because in spite of this mental block I am a visual kind of guy.
Here is the page with the connecting rod drawing.
Here is the page with the connecting rod drawing.
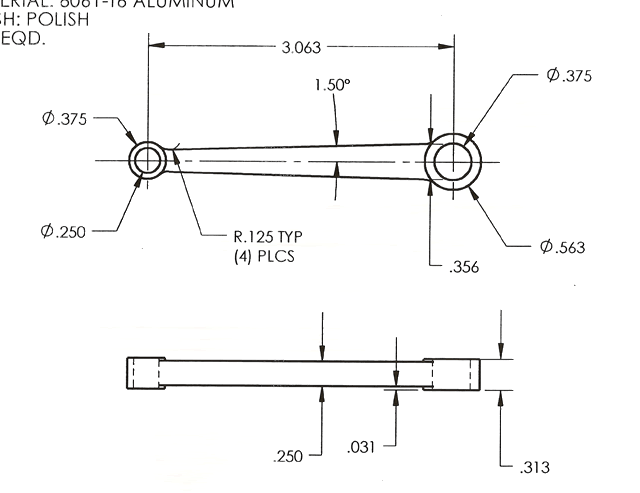