deere_x475guy
Well-Known Member
Well I needed to come up with a .098 wide grove tool today for the fins I need to machine on my next engine. My parting tool is .058 and I probably could have gotten away with using that but I have a surface grinder and plenty of HHS blanks so set out this morning to grind up a tool that was as close to .098 as I could get it.
Here you see that I have blocked in the HHS bit so that it doesn't move. It's always a good idea to use bigger blocks of steel to try to stop the little parts from moving around. If you don't there is always a chance it could move or worse yet go flying across the room.
oops.....I am .0003 under....oh well it's going to have to work...

And I guess I am showing to tools on this thread. I built that micrometer stand probably a year ago or so...heck everything to me is a year ago a so anymore.....dang memory...
Here you see that I have blocked in the HHS bit so that it doesn't move. It's always a good idea to use bigger blocks of steel to try to stop the little parts from moving around. If you don't there is always a chance it could move or worse yet go flying across the room.
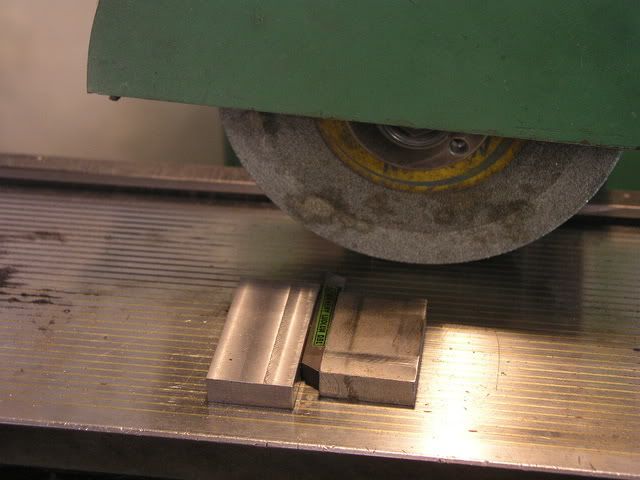
oops.....I am .0003 under....oh well it's going to have to work...
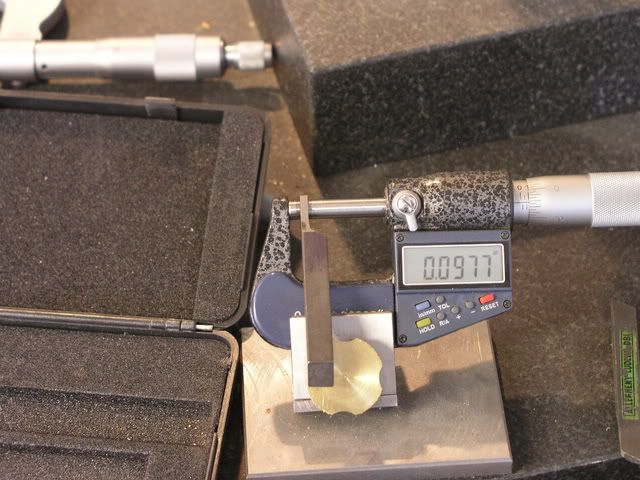
And I guess I am showing to tools on this thread. I built that micrometer stand probably a year ago or so...heck everything to me is a year ago a so anymore.....dang memory...