BobWarfield
Well-Known Member
- Joined
- Dec 27, 2007
- Messages
- 1,151
- Reaction score
- 1
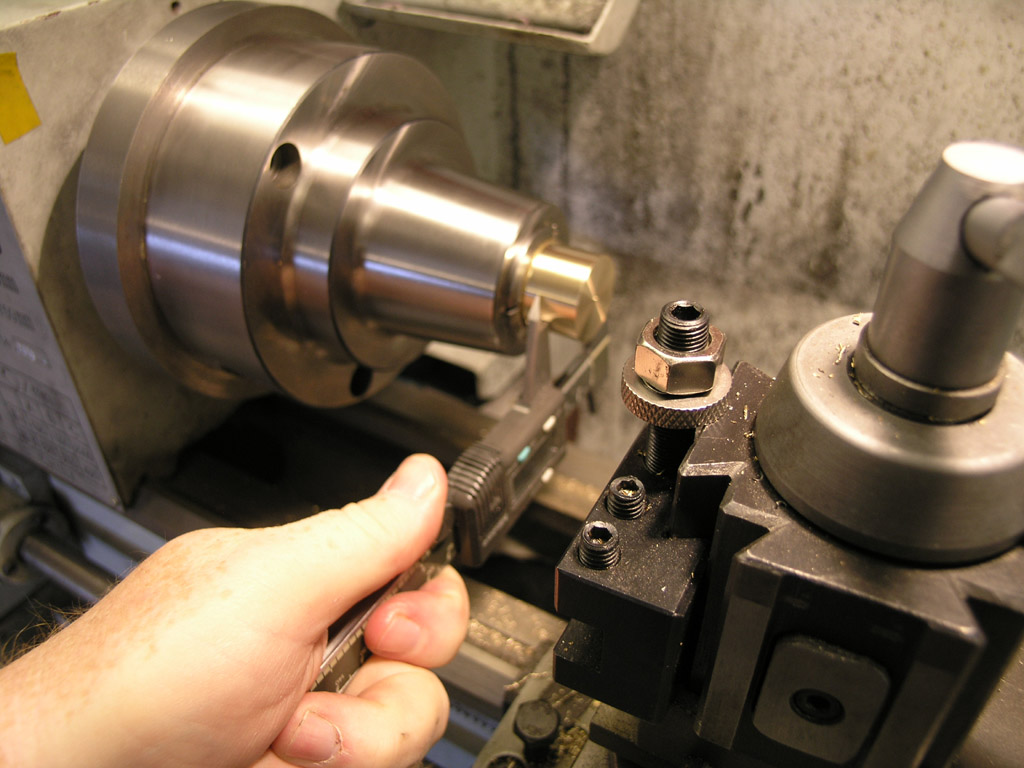
Take your digital calipers and get a rough sense of where you are. I'm shooting for a 1" diameter and my measurements were typically 1.050-1.090 or so. Based on that measurement, I ran the dials until I thought I was within a couple of thou...
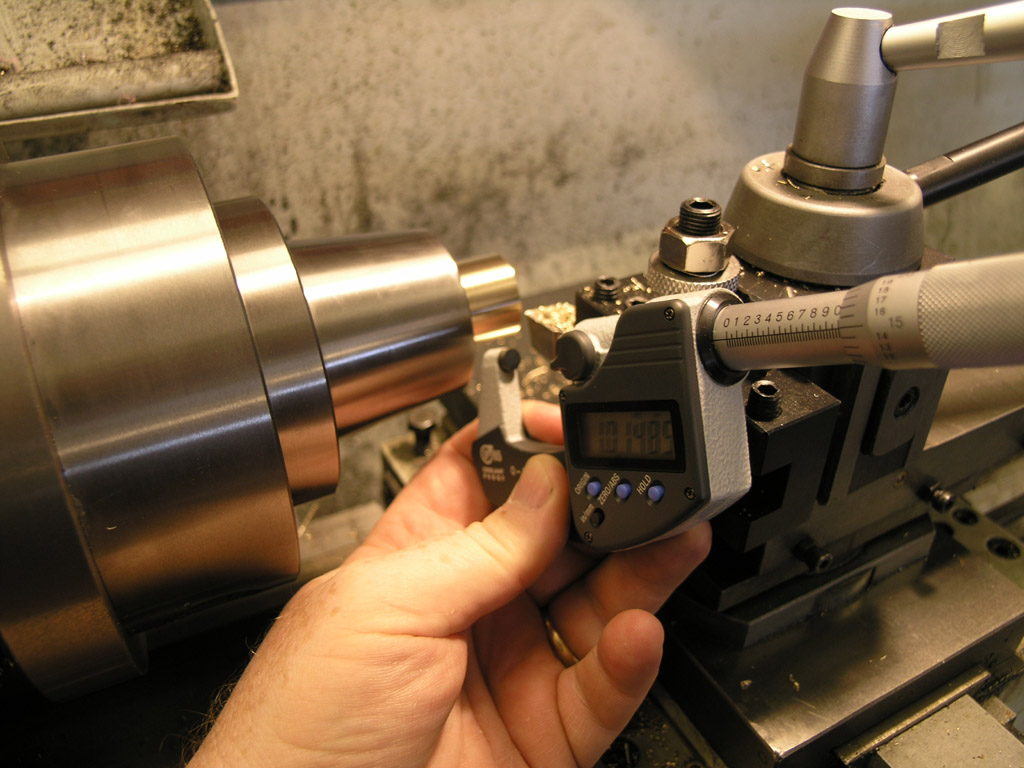
Check the last couple thou with the mic, do the finish pass, and mic again to be sure. A habit that saves me time is when I retract the cross slide, I retract exactly one revolution from wherever I was. That way it's easy to remember how to get back to cutting...
And yes, Virginia, with the sharp inserts I was using, I could take as little as half a thou off this brass.
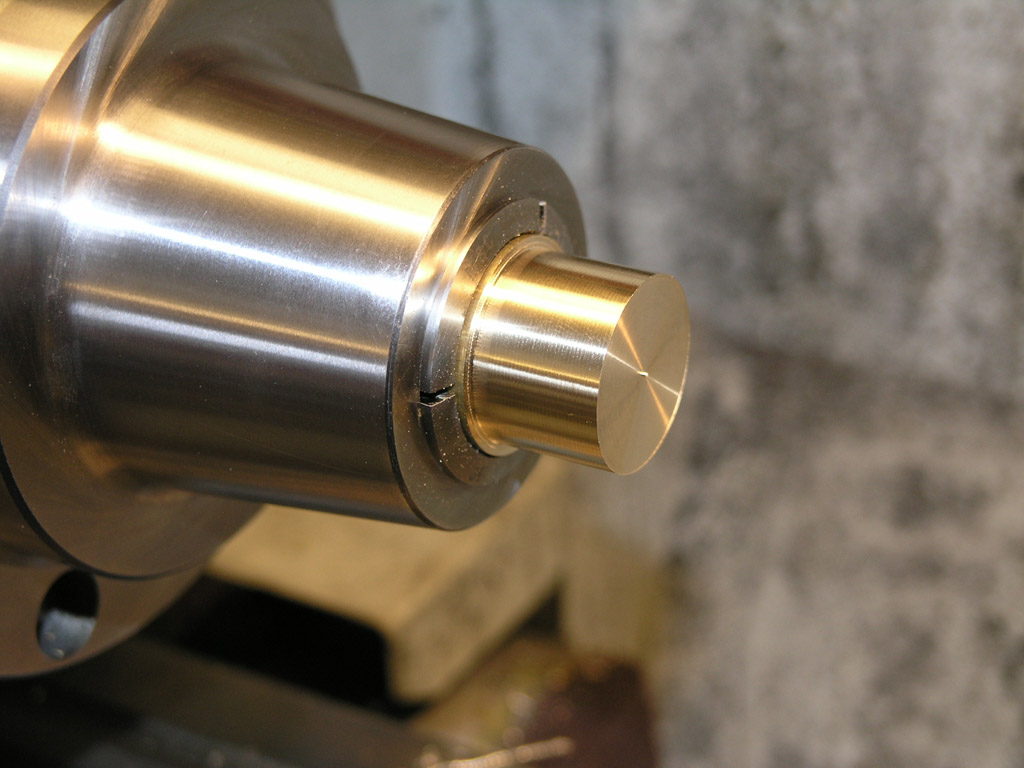
Faced and turned to 1" diameter, +0.003", -0.000". I was aiming slightly for the high side as polish will take off up to a thou based on my experiments.
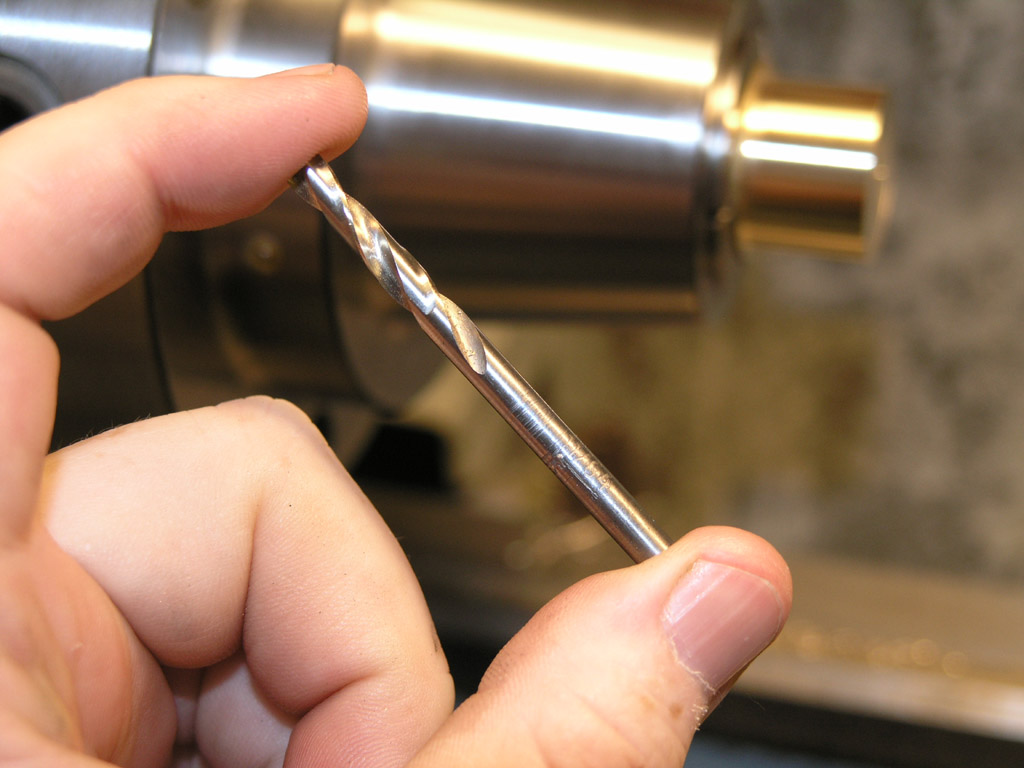
Next I am using a screw machine-length twist drill for the shaft bore. The screw machine length is more rigid than normal jobber length and with a minimal facing nub you can go right in without a center drill, thus saving a step...
<continued>