BobWarfield
Well-Known Member
- Joined
- Dec 27, 2007
- Messages
- 1,151
- Reaction score
- 1
Got busy today and finished up the project. I'm very pleased with the result:
I couldn't resist loading up the disc a bit by round the sharp edges on my table brackets. It took less than a minute per bracket, freehand. I was pushing hard to see if I could bog it down, but the 3/4 HP motor never slowed a bit that I could see. I think the 3400 rpm really contribute to aggressive metal removal too.
"Before" bracket:
"After" bracket:
I think I'm going to like having this thing around a lot!
Full details of the build are on my web site (more than you wanted to know, probably!): http://www.cnccookbook.com/CCDiscSander.htm
Thanks to Dickeybird and others for providing the inspiration. Your efforts are credited in the article as well.
Cheers,
BW
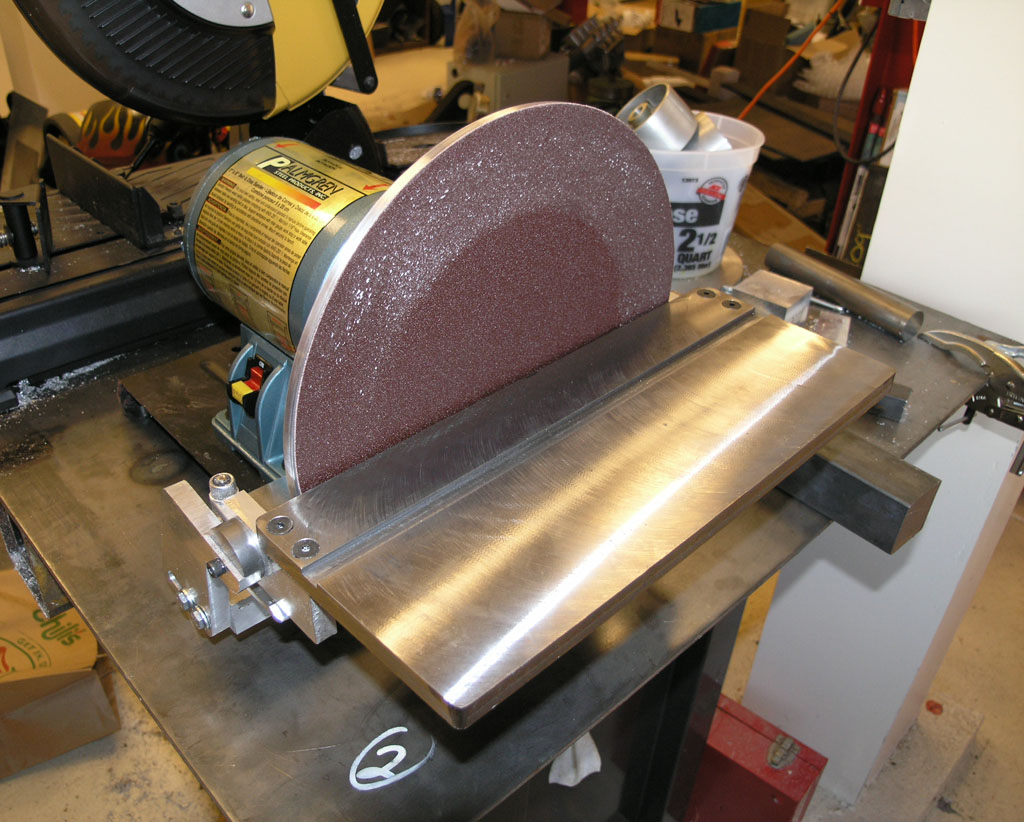
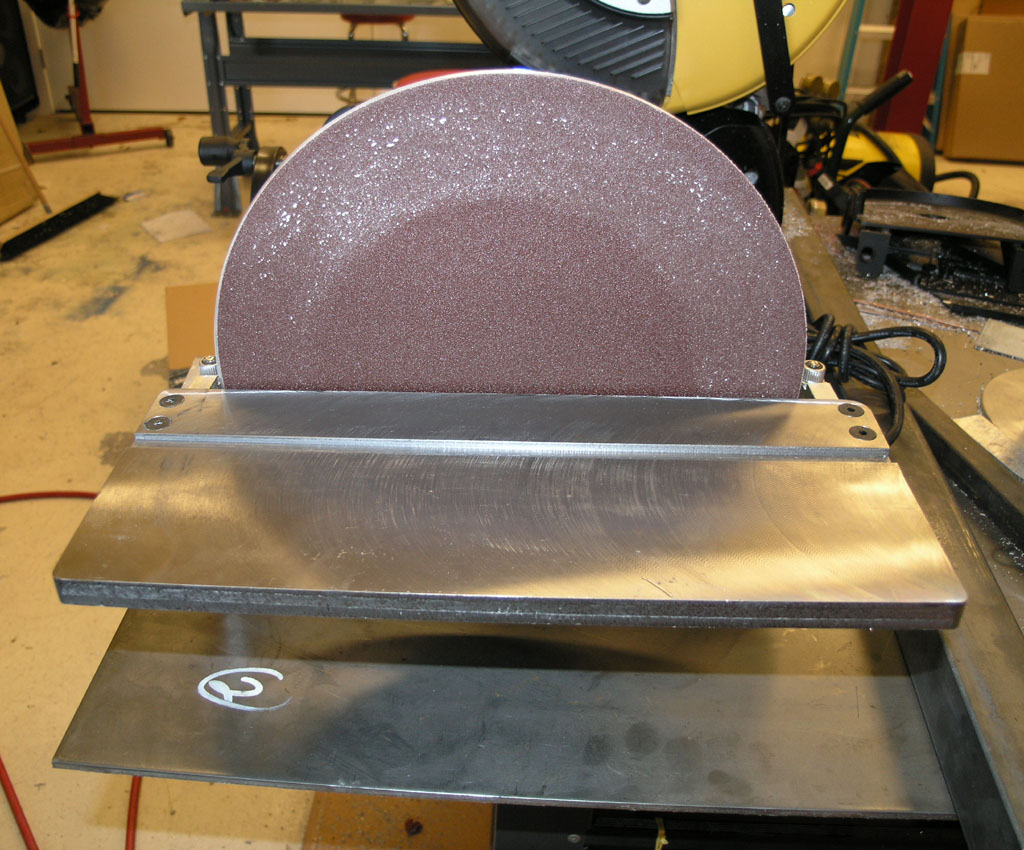
I couldn't resist loading up the disc a bit by round the sharp edges on my table brackets. It took less than a minute per bracket, freehand. I was pushing hard to see if I could bog it down, but the 3/4 HP motor never slowed a bit that I could see. I think the 3400 rpm really contribute to aggressive metal removal too.
"Before" bracket:
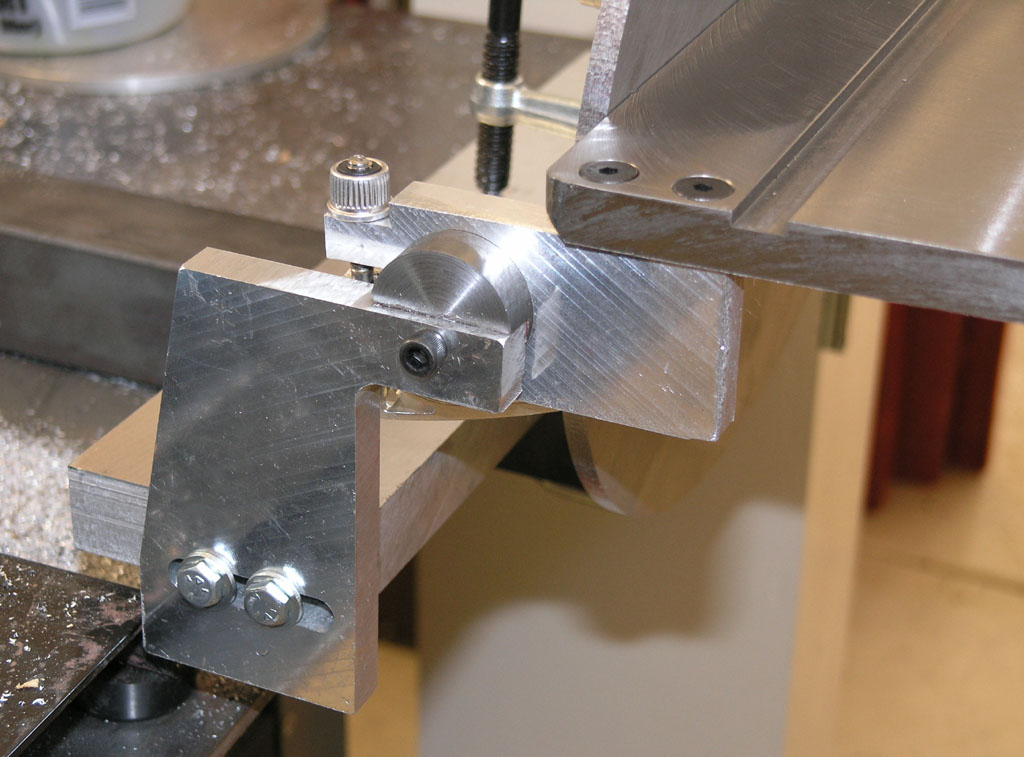
"After" bracket:
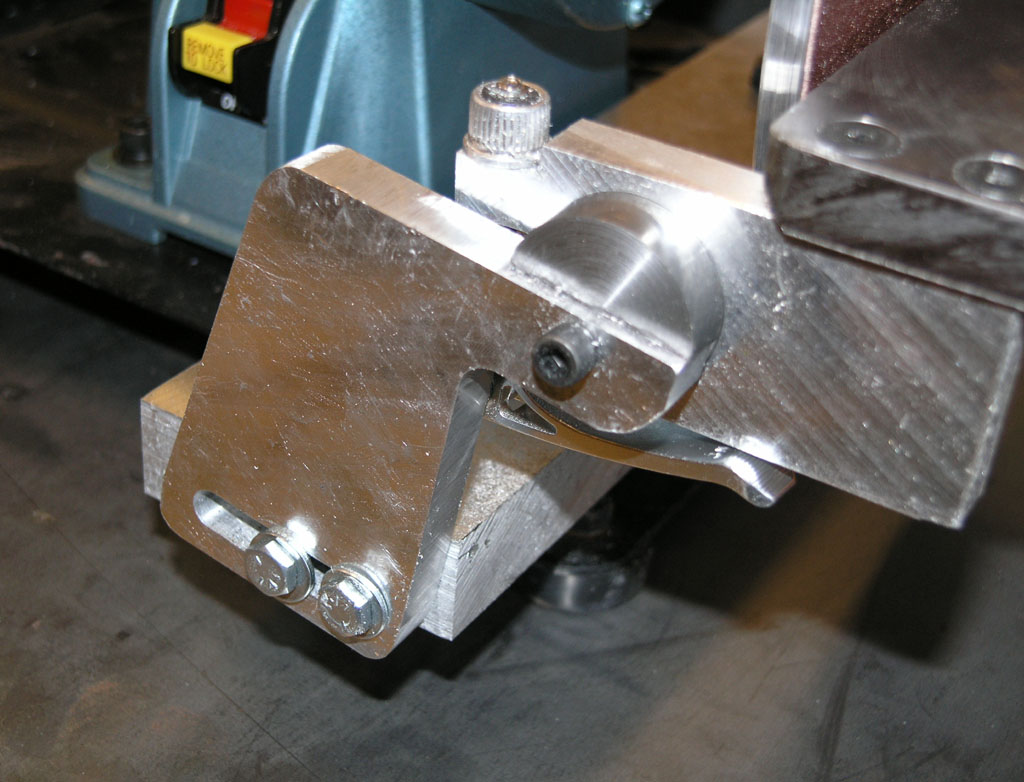
I think I'm going to like having this thing around a lot!
Full details of the build are on my web site (more than you wanted to know, probably!): http://www.cnccookbook.com/CCDiscSander.htm
Thanks to Dickeybird and others for providing the inspiration. Your efforts are credited in the article as well.
Cheers,
BW