BobWarfield
Well-Known Member
- Joined
- Dec 27, 2007
- Messages
- 1,151
- Reaction score
- 1
I got a knock-off of the Blake Coaxial Indicator from Shars and got a chance to try it out today. Man, what a cool gadget!
Here it is in action as I center the spindle over that hole so I can use my boring head to make a shoulder on the hole:
If you've never tried one, they work like this. Picture that long feeler as being sort of like a very exagerated finger from a dial test indicator. It goes against the inside of the hole, or there are curved feelers included for the outside of a round boss. You turn on the spindle at the lowest rpm, say 100rpm, and hold the horizontal rod. This keeps the indicator facing your way while the feeler sweeps around the circumference of the feature you want to center on. As the feeler sweeps around, the needle will "kick" because the spindle axis is not centered. Now adjust the X and Y axis handwheels until the needle kicks as little as possible. That's all there is to it, you are done very quickly. What a nice gadget!
Adjust the axes one at a time and don't even think much about what's needed. Simply turn the wheel and observe whether the needle kicks more or less. Turn it in the direction that kicks less. When you've minimized the kick on one axis, do the other. I circled back a second time around and got to almost no kick at all.
I did not set up the Indicol and DTI to check the result as I was in a hurry, but visually, after I used the boring head to make the shoulder, it looked spot on.
It tool longer to stick the Blake in the R8 collet than it did to adjust the X and Y axes, or so it seemed. Apparently they can also be used to dial in a 4-jaw chuck. I'm going to love having this little gadget around I think!
Here it is in action as I center the spindle over that hole so I can use my boring head to make a shoulder on the hole:
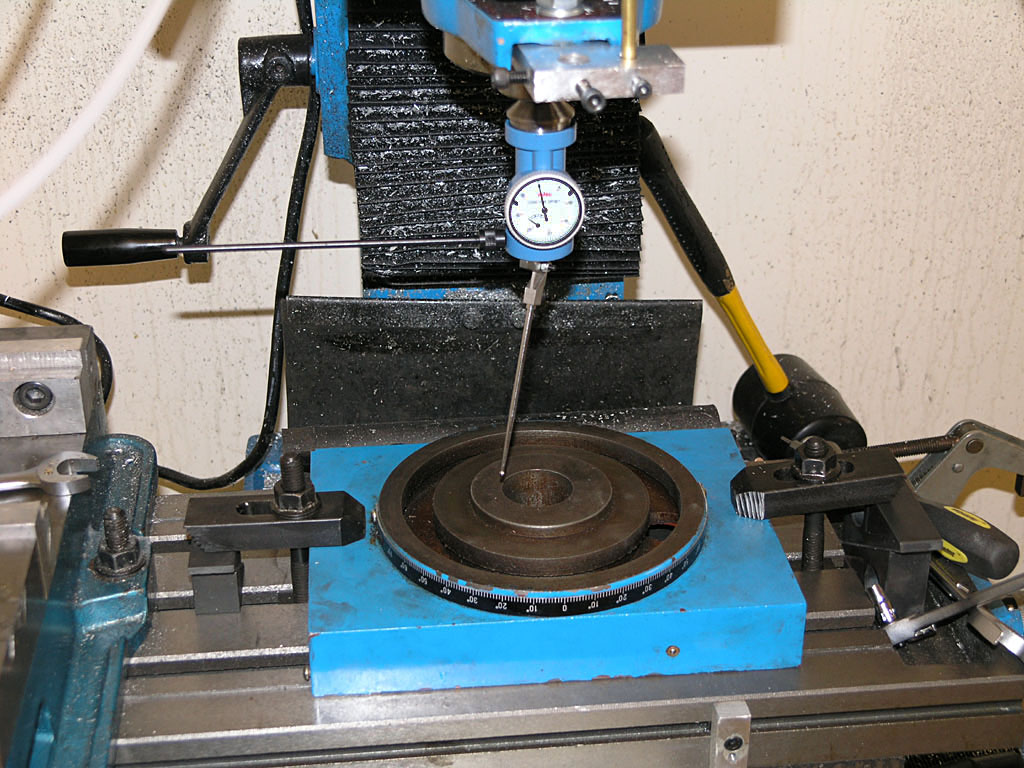
If you've never tried one, they work like this. Picture that long feeler as being sort of like a very exagerated finger from a dial test indicator. It goes against the inside of the hole, or there are curved feelers included for the outside of a round boss. You turn on the spindle at the lowest rpm, say 100rpm, and hold the horizontal rod. This keeps the indicator facing your way while the feeler sweeps around the circumference of the feature you want to center on. As the feeler sweeps around, the needle will "kick" because the spindle axis is not centered. Now adjust the X and Y axis handwheels until the needle kicks as little as possible. That's all there is to it, you are done very quickly. What a nice gadget!
Adjust the axes one at a time and don't even think much about what's needed. Simply turn the wheel and observe whether the needle kicks more or less. Turn it in the direction that kicks less. When you've minimized the kick on one axis, do the other. I circled back a second time around and got to almost no kick at all.
I did not set up the Indicol and DTI to check the result as I was in a hurry, but visually, after I used the boring head to make the shoulder, it looked spot on.
It tool longer to stick the Blake in the R8 collet than it did to adjust the X and Y axes, or so it seemed. Apparently they can also be used to dial in a 4-jaw chuck. I'm going to love having this little gadget around I think!