As I finished up tonight and slurped on a brew..... I looked at the mill and saw something I dont see often in pics that others post.
Magnetic LED lamp (2 actually), very useful all round....
Telescopic magnet.... almost vital for older backs.....
Sticky pin, something I use almost every time I use the machine..... I have the DRO's ordered for the x and y axis and these will probably negate the need for this lil tool. But I like it for its simplicity....
I have the quill DRO already installed and find this invaluable. I have gone for independant read outs, basically the pessimist in me thinks that if one fails them all are lost unless they are individual units, so thats the way I have gone...
The quill is a self contained unit/readout but the x and y axis are remote screens although not as large as I might have liked, but i did compromise on this. Ill post pics when they are installed.
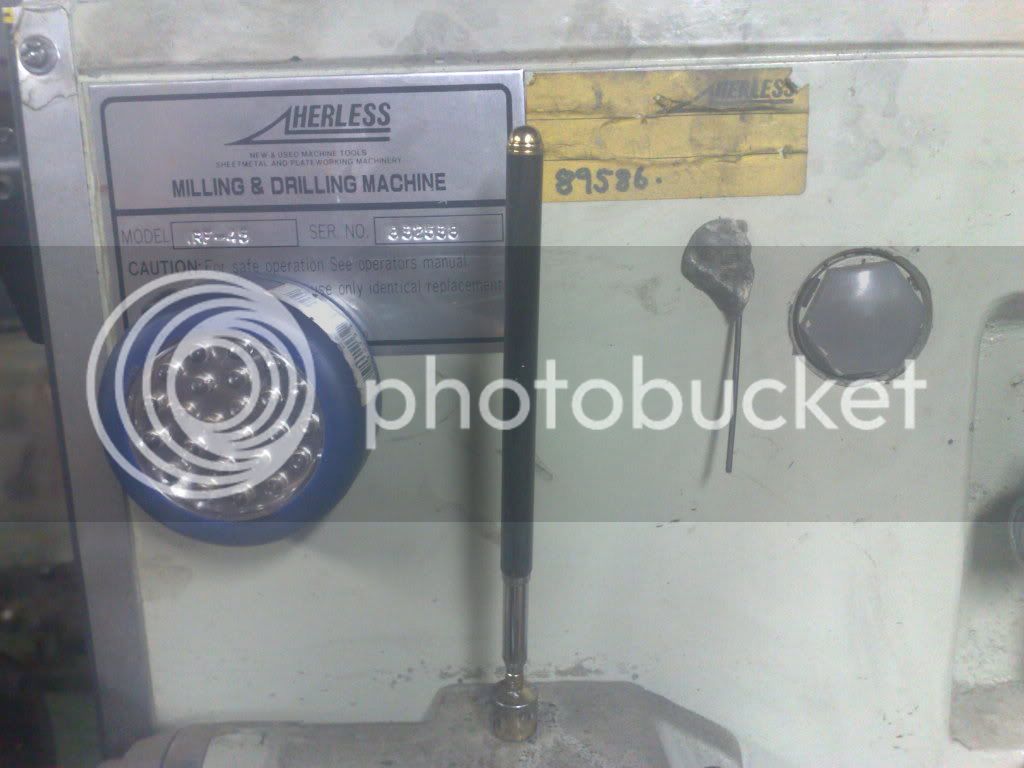
Magnetic LED lamp (2 actually), very useful all round....
Telescopic magnet.... almost vital for older backs.....
Sticky pin, something I use almost every time I use the machine..... I have the DRO's ordered for the x and y axis and these will probably negate the need for this lil tool. But I like it for its simplicity....
I have the quill DRO already installed and find this invaluable. I have gone for independant read outs, basically the pessimist in me thinks that if one fails them all are lost unless they are individual units, so thats the way I have gone...
The quill is a self contained unit/readout but the x and y axis are remote screens although not as large as I might have liked, but i did compromise on this. Ill post pics when they are installed.
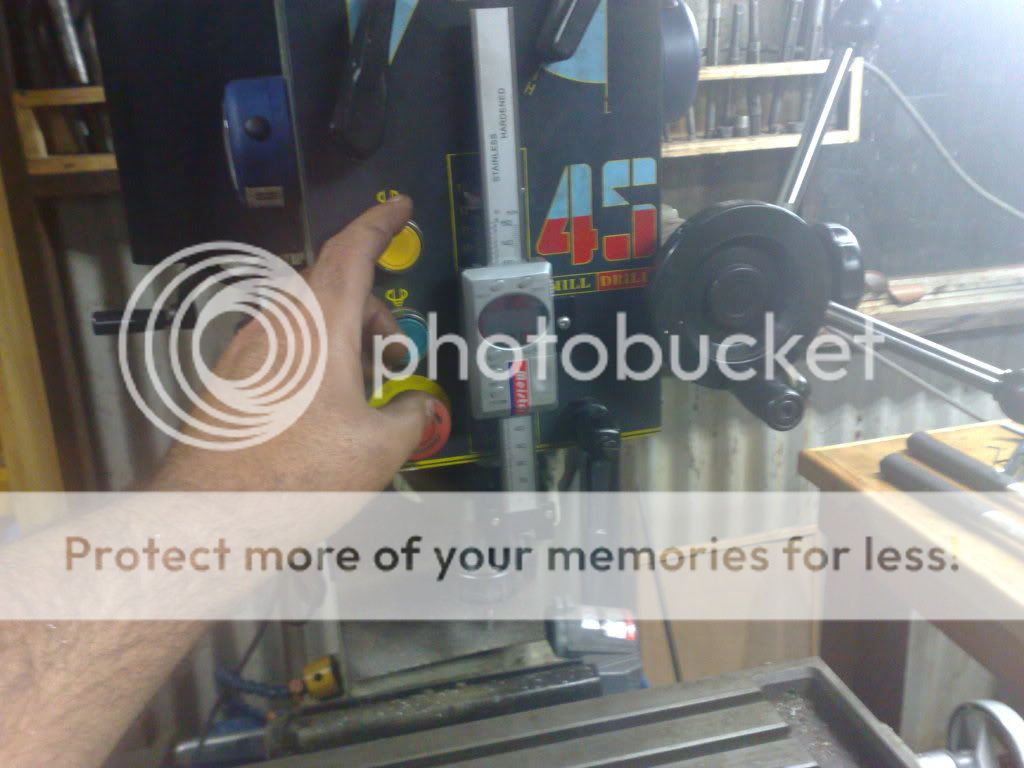