This sort of snuck in under the radar. Nothing was planned but this opportunity came along and away it went......
'This' is a set of angle plate raw castings I saw on Flea-buy. I put in a bid of $20 and damn if I didnt win it. :
It all arrived yesterday, I picked up some suitable sized hi tensile nuts n bolts and after work I jumped in.
Firstly square up the lugs...
Missed a pic here, sorry... bolted my fixed 90Deg angle plate to the mill table, clamped the surface plates and adjusted them to vertical and drilled the bolt holes through.... then bolted it together... the tables came out parallel.. wow... doing something wrong... ;D
This is a p.s. im thinking about a single through bolt with a suitable spacer instead of the tweo nolts. Anyone have any experience here? Just thinking it would be easier to cinch up one bolt than two...
Its loaded onto the surface grinder in the last shot... lights really bad by now....
I dont have a finished shot as it was after 7 when I got the faces flat and square and really dark in this corner of the shop. Will add one tonight when I get home.
Came up really well... its just another piece to the puzzle which is our workshops. Dont know how often Ill use it.. but I cant use it if I havent got it.... if its anything like the old horizontal mill, its done a heap of work since recommissioning...
I will say that working with cast iron isnt my favourite material...
These are 'office' hands.... dont often get like this anymore..
Cheers, Rob T
'This' is a set of angle plate raw castings I saw on Flea-buy. I put in a bid of $20 and damn if I didnt win it. :
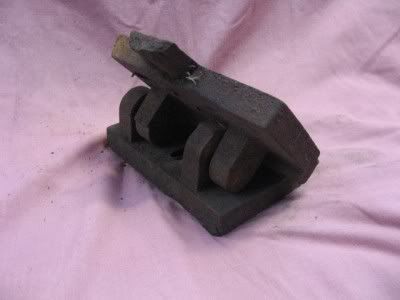
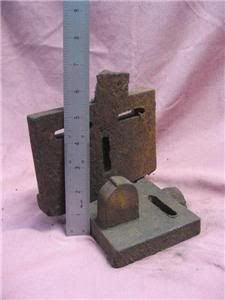
It all arrived yesterday, I picked up some suitable sized hi tensile nuts n bolts and after work I jumped in.
Firstly square up the lugs...
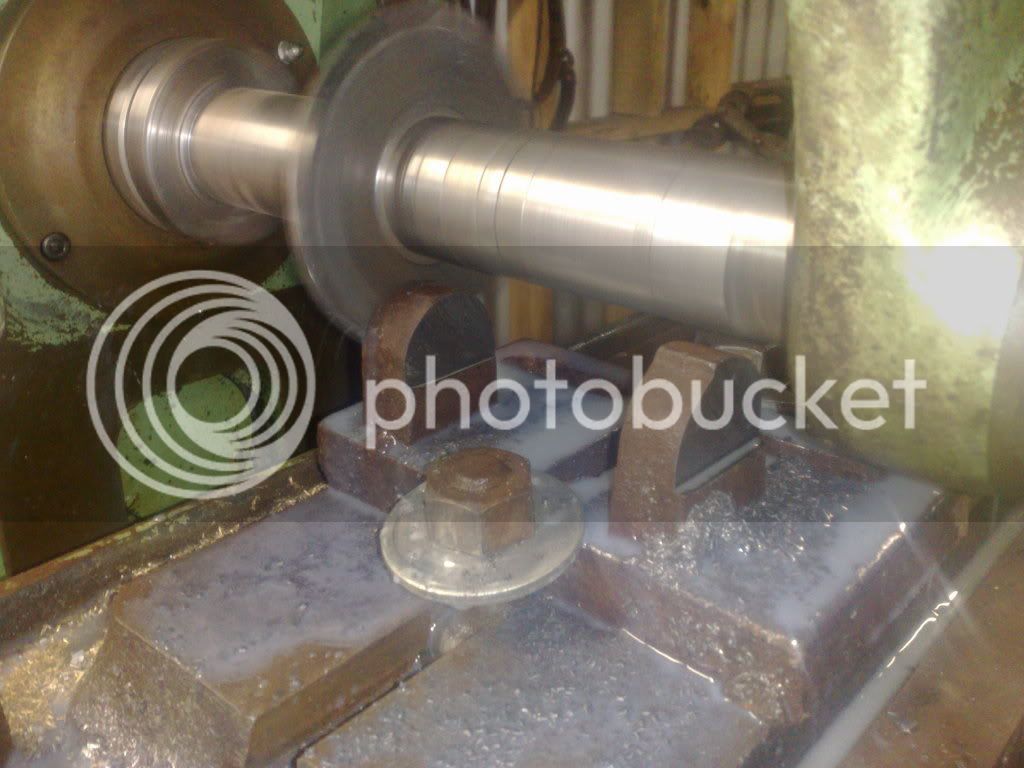
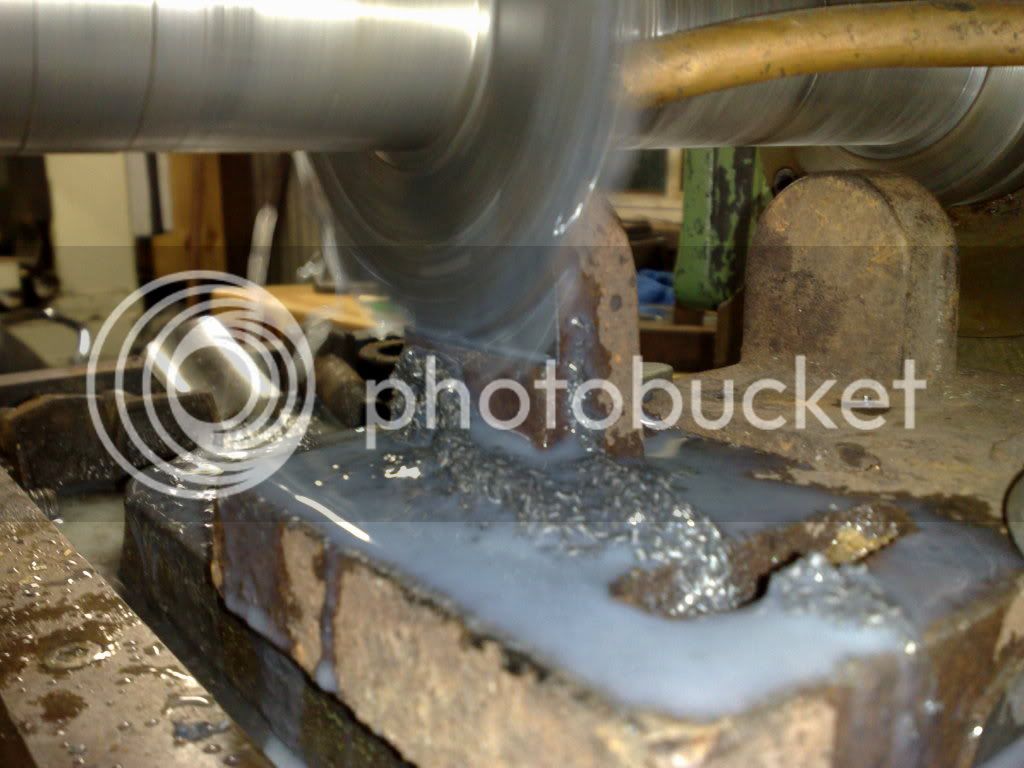
Missed a pic here, sorry... bolted my fixed 90Deg angle plate to the mill table, clamped the surface plates and adjusted them to vertical and drilled the bolt holes through.... then bolted it together... the tables came out parallel.. wow... doing something wrong... ;D
This is a p.s. im thinking about a single through bolt with a suitable spacer instead of the tweo nolts. Anyone have any experience here? Just thinking it would be easier to cinch up one bolt than two...
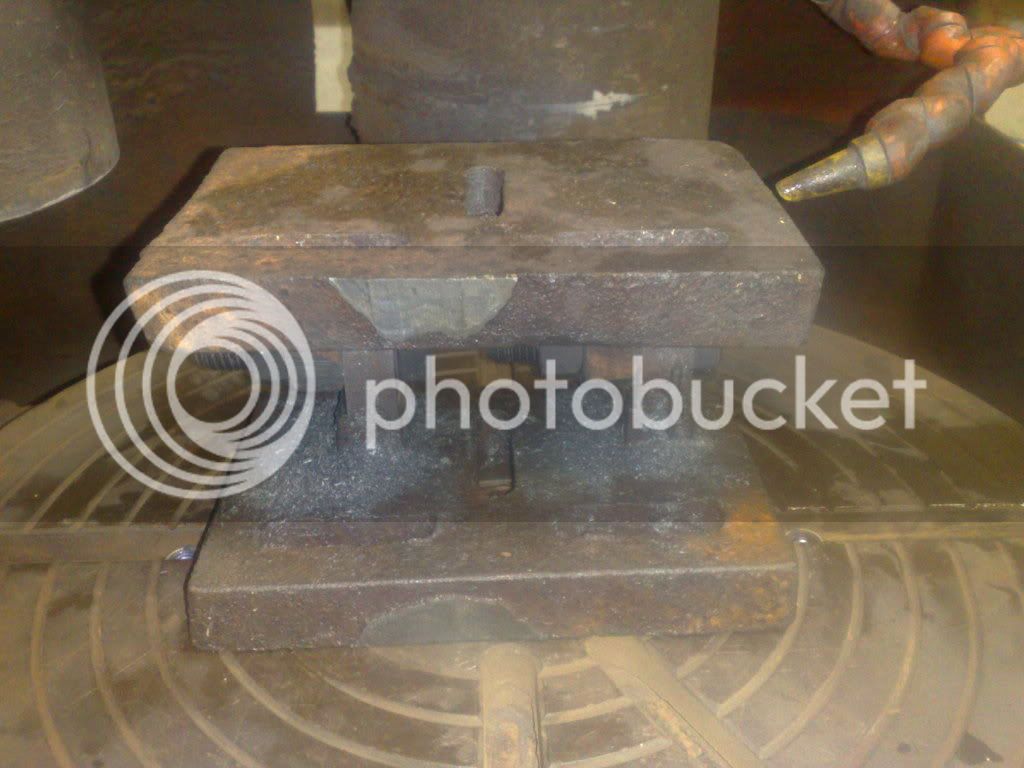
Its loaded onto the surface grinder in the last shot... lights really bad by now....
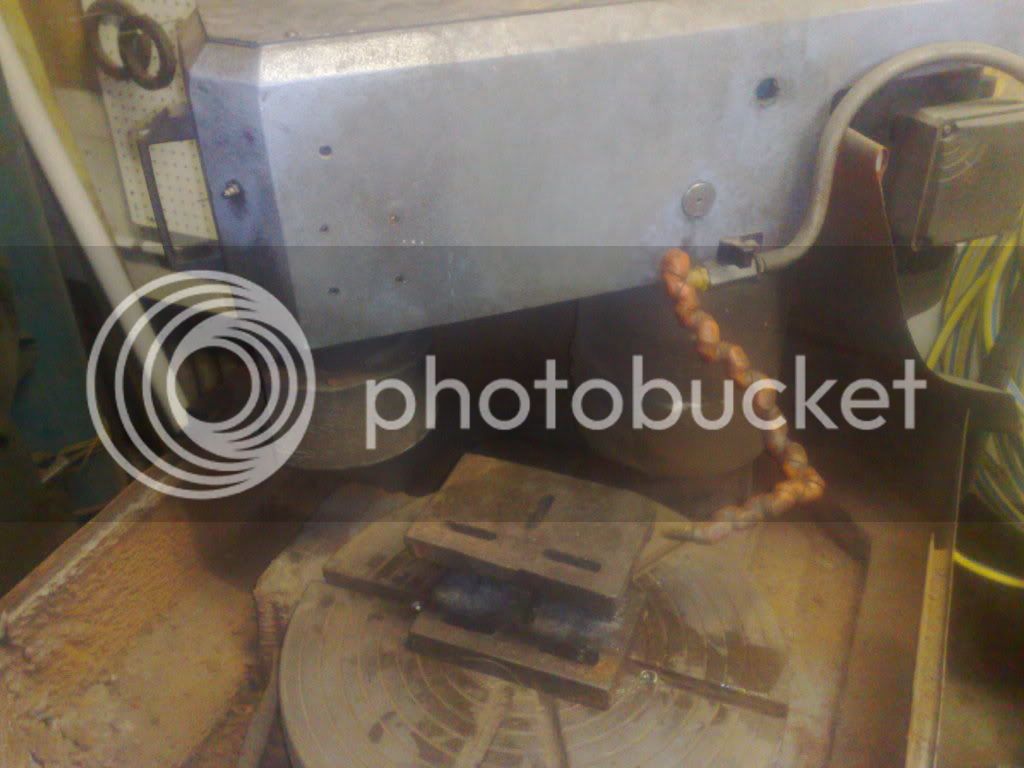
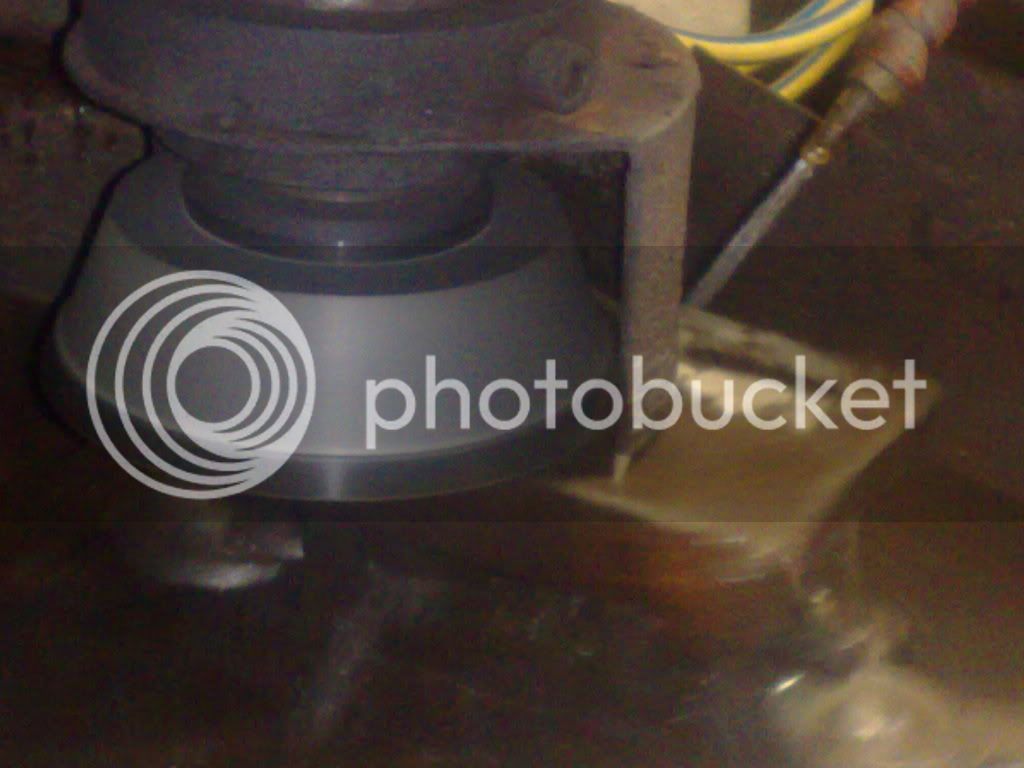
I dont have a finished shot as it was after 7 when I got the faces flat and square and really dark in this corner of the shop. Will add one tonight when I get home.
Came up really well... its just another piece to the puzzle which is our workshops. Dont know how often Ill use it.. but I cant use it if I havent got it.... if its anything like the old horizontal mill, its done a heap of work since recommissioning...
I will say that working with cast iron isnt my favourite material...
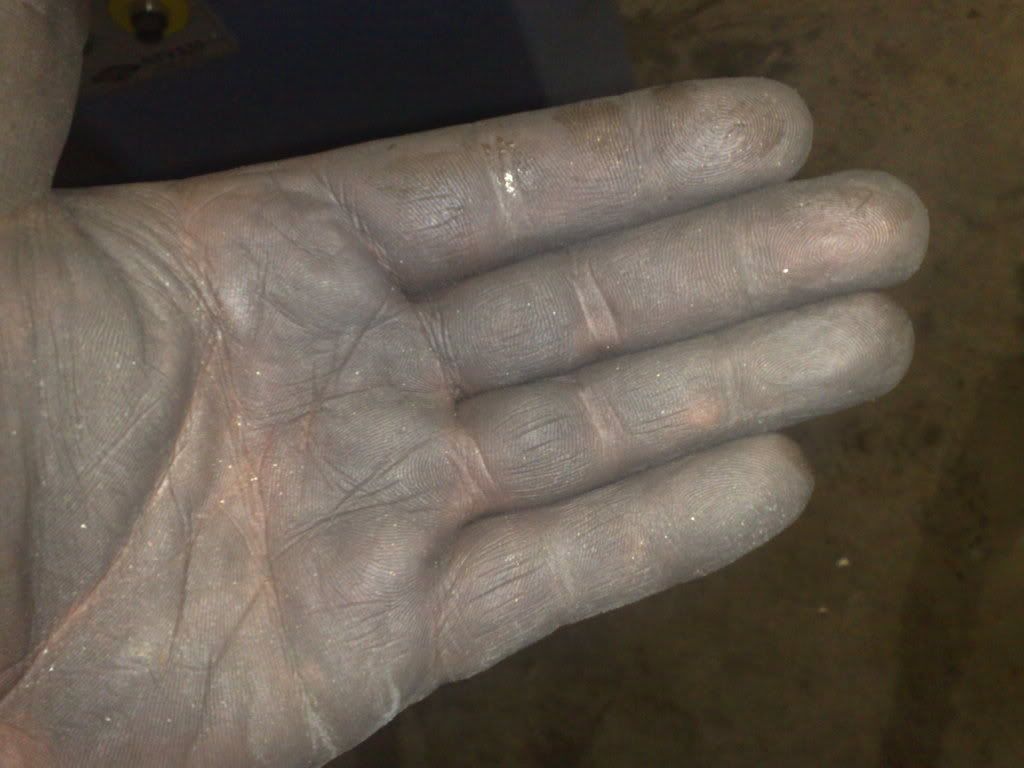
These are 'office' hands.... dont often get like this anymore..
Cheers, Rob T