Divided He ad
Well-Known Member
- Joined
- Mar 21, 2008
- Messages
- 549
- Reaction score
- 2
Some of you may remember the post I deleted a little while ago after some objections to the use of a buffing mop in the lathe chuck?
Well I did listen and have made the necessary adjustments to make it as safe as any buffing wheel. IMO.
Once again I am NOT telling you that this is perfect or totally safe.... You are still working with machinery and that is ALWAYS dangerous.
Well on with the post... Due to some donated parts and a little time in the shop (this is the first time I wanted to polish anything for some time) I made this little set up.... And in my eyes it is far safer to use than with the chuck attached. I can't see a dedicated buffing machine being any safer than this... Feel free to shout out any objections... I'll not remove this post.
MT3 blank....
A bit of free hand shaping, ;D making sure to leave a collar the same size as the thread... A bit safer than turning it all down to 16MM
A little flat to aid drilling.
Drilled and tapped for grubscrew M6x1.0.
drill for pigtail shaft to fit, in this instance 6mm
And you end up with this....
Add a buffing mop and you are away ;D
This not only provides a Great deal more safety but also allows you to get to both sides of the mop easily ;D
Very happy with this mod
Just used it to polish a the mini ball turner ;D
I am thinking about a cover for the threads.... Just a cylinder held in place by the MT3, there is enough of a gap between the arbour and the spindle to accommodate a cover.... Well that's for next time I'm going to polish something ;D
Ralph.
Well I did listen and have made the necessary adjustments to make it as safe as any buffing wheel. IMO.
Once again I am NOT telling you that this is perfect or totally safe.... You are still working with machinery and that is ALWAYS dangerous.
Well on with the post... Due to some donated parts and a little time in the shop (this is the first time I wanted to polish anything for some time) I made this little set up.... And in my eyes it is far safer to use than with the chuck attached. I can't see a dedicated buffing machine being any safer than this... Feel free to shout out any objections... I'll not remove this post.
MT3 blank....
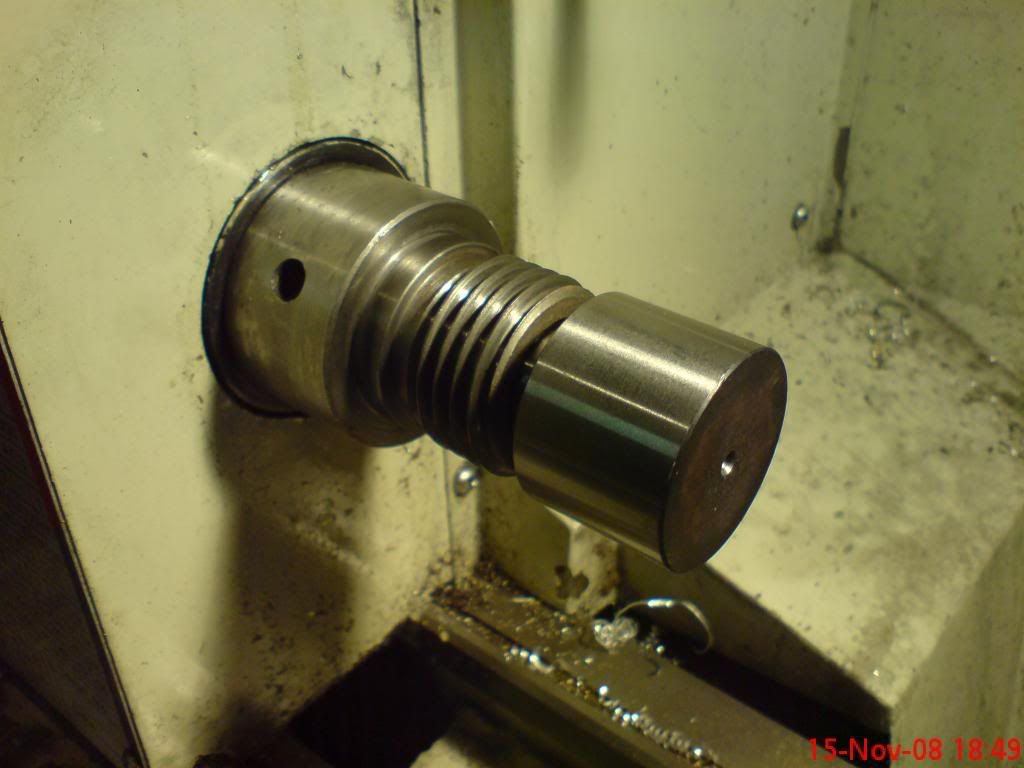
A bit of free hand shaping, ;D making sure to leave a collar the same size as the thread... A bit safer than turning it all down to 16MM
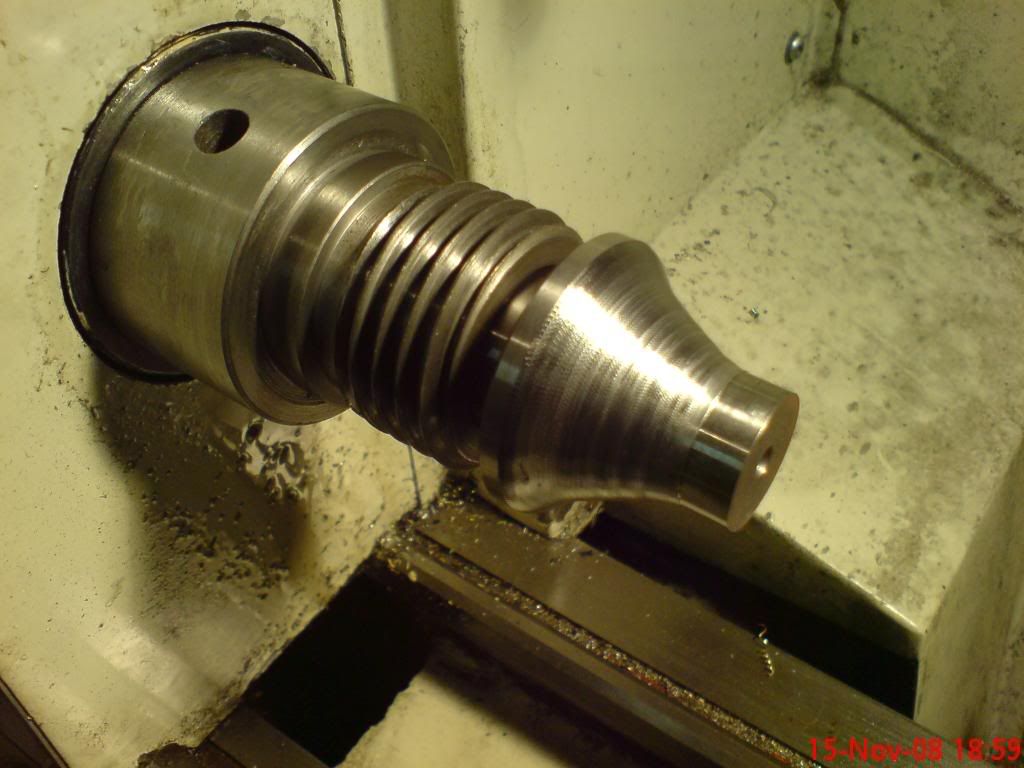
A little flat to aid drilling.
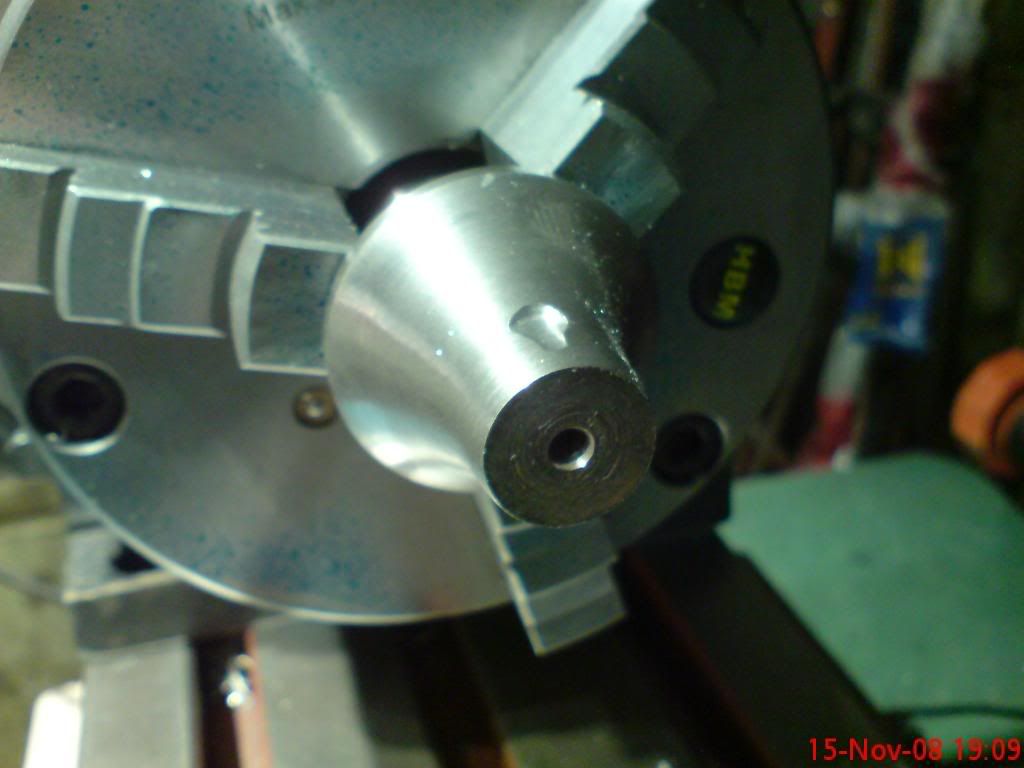
Drilled and tapped for grubscrew M6x1.0.
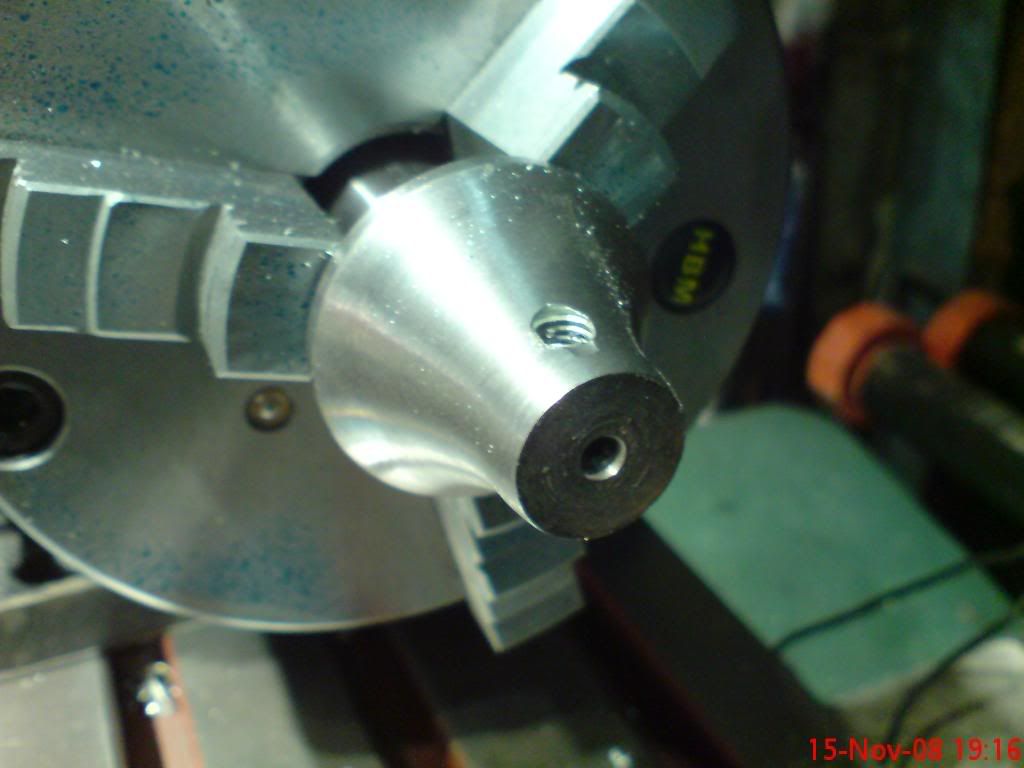
drill for pigtail shaft to fit, in this instance 6mm
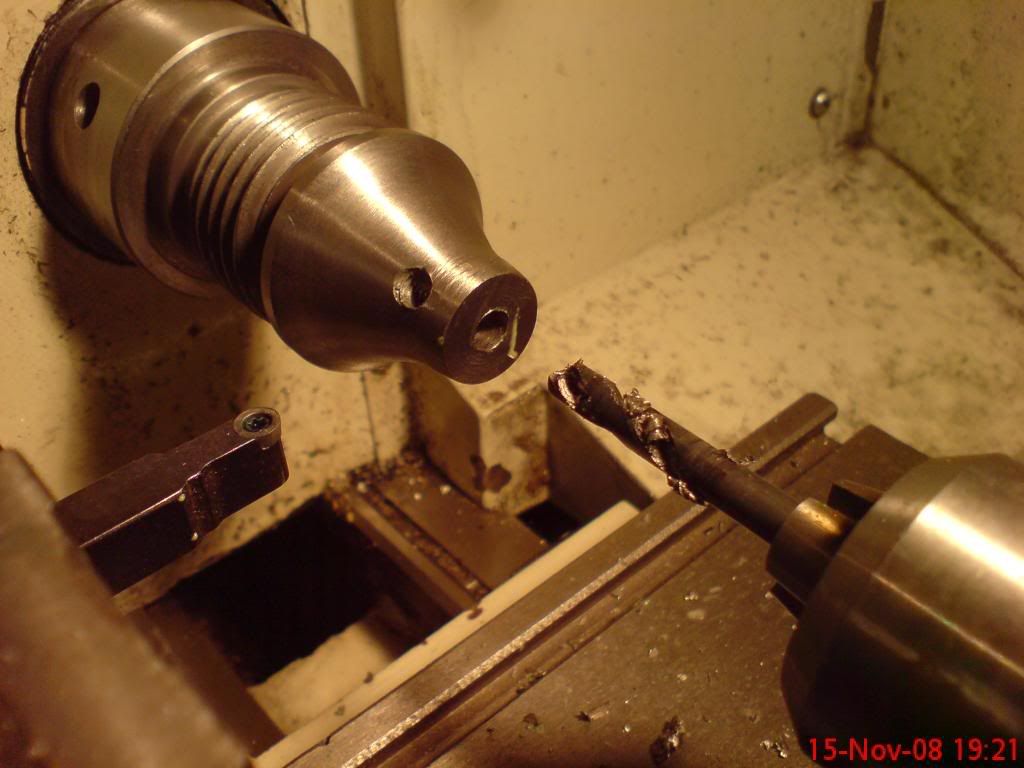
And you end up with this....
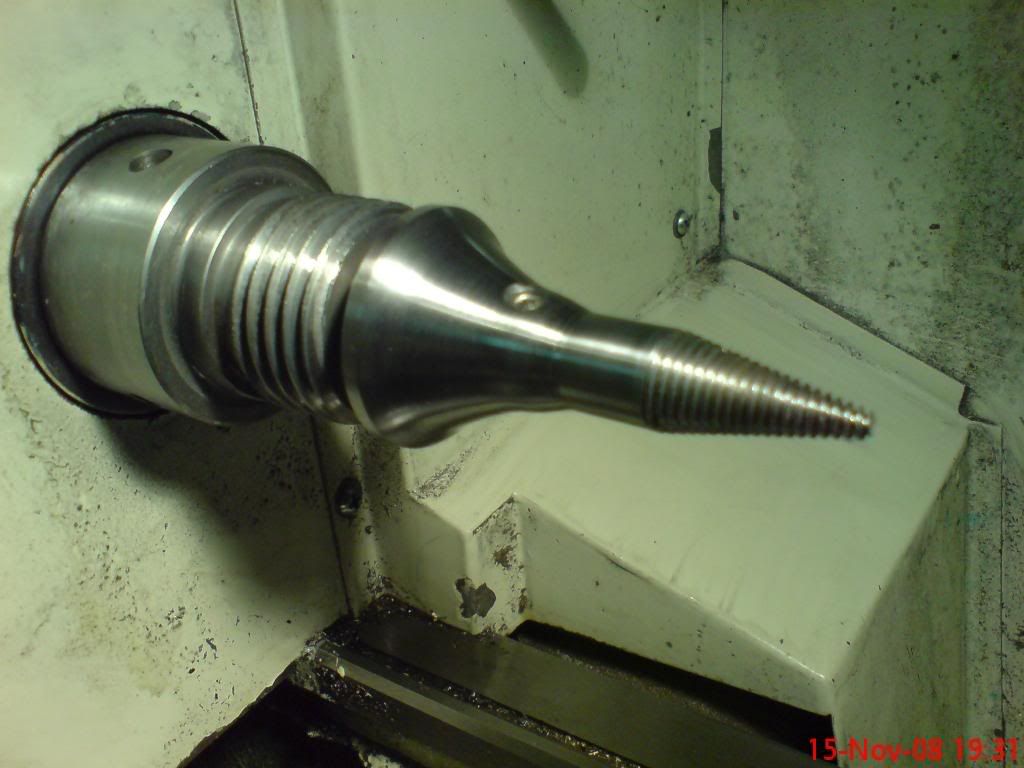
Add a buffing mop and you are away ;D
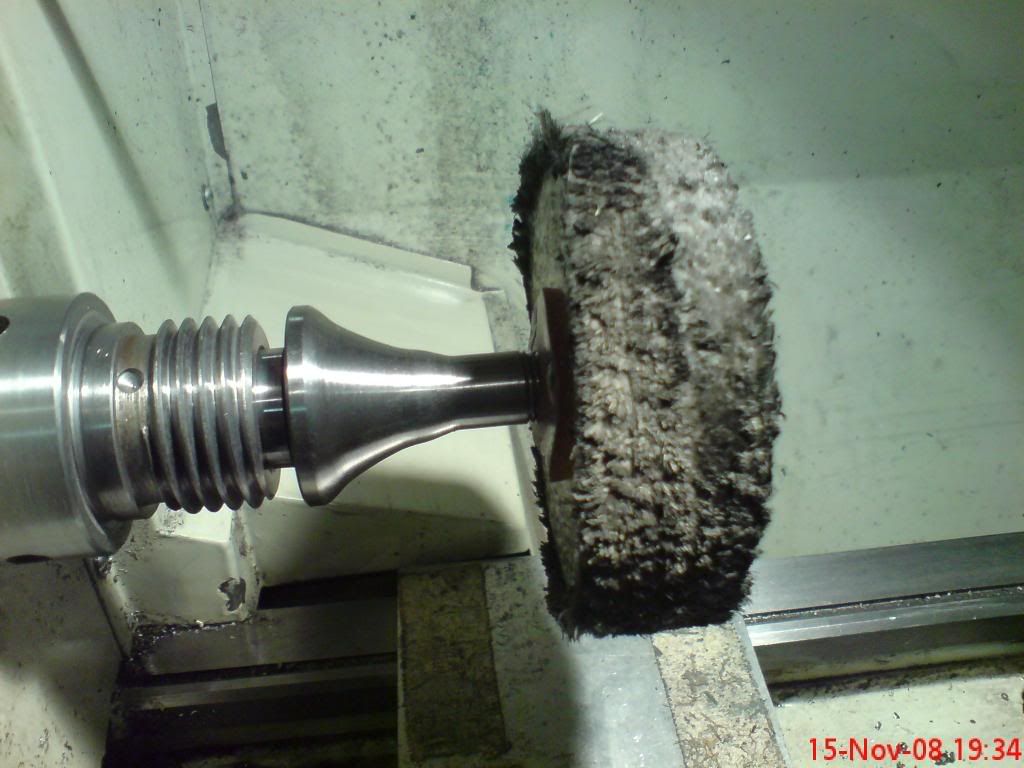
This not only provides a Great deal more safety but also allows you to get to both sides of the mop easily ;D
Very happy with this mod
I am thinking about a cover for the threads.... Just a cylinder held in place by the MT3, there is enough of a gap between the arbour and the spindle to accommodate a cover.... Well that's for next time I'm going to polish something ;D
Ralph.