Ok I am making a crankshaft from 3/8" steel. The end of it needs to be turned down to 1/16", the plans say once you get down to 1/8" to support the end with the tail stock. Well how do I do that?
The orange marks show the travel I would need back and forth so the tail stock is as far left as it can go and fully extended.
I'm sure this is a simple thing, but I can't figure it out.
Thanks
Chris
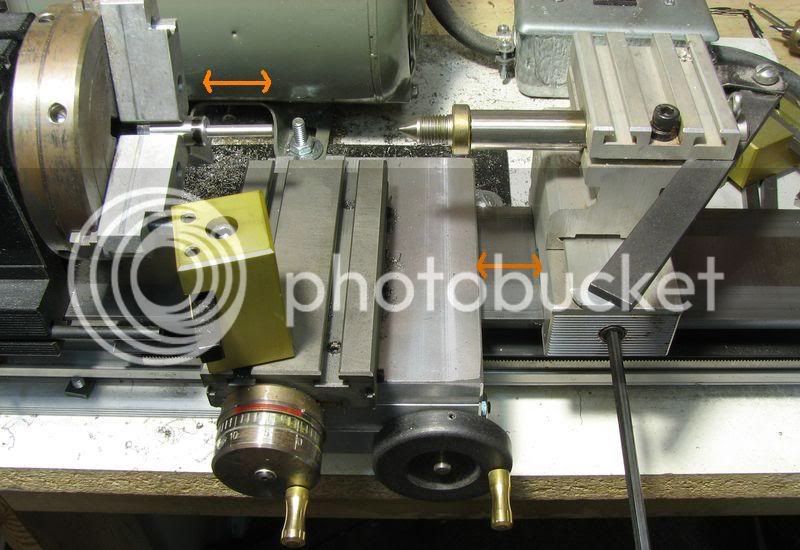
The orange marks show the travel I would need back and forth so the tail stock is as far left as it can go and fully extended.
I'm sure this is a simple thing, but I can't figure it out.
Thanks
Chris