- Joined
- Dec 2, 2008
- Messages
- 971
- Reaction score
- 8
I got out one of my older engines to play with and this is how it started. This is on of my favorite engines for a number of reasons but mainly because it works so well. It is reliably self starting. It turns slowly at almost no PSI. It is well balanced and runs at high speed with little vibration. It is quirky locking. And it seems to produce good torque.
VIDEO
How good? I decided to find out. The tools needed are a non-contact tachometer ($16 from Amazon.com) and a sensitive scale. For about $300 you can get an accurate digital scale or for about $12 you can get an OK spring scale. I went with the spring scale ($12 from an E-bay store). The scale that I got has a capacity range of 0 - .5 Lbs marked in .02lb increments on a scale about 2 inches long. Perfect for the job.
The Prony brake is a simple device made out of a short length 1/4" square red oak. One end is formed into a clamp that is adjusted with a SHC screw and fits around the bare 1/4" engine shaft that extends beyond the flywheel. At a point that is 2 inches from the center of the shaft is pierced by a pin to hold the hangar bracket of the scale. The torque applied by the brake will be directly read from the scale in (inch pounds)/2. The flywheel is 2.5" diameter so it was not practical to set the beam length to 1 inch. The scale is suspended from a shelf above the bench so that the beam of the prony brake is about level. The engine flywheel is wrapped with black tape and a reflective strip for the tachometer is applied.
Before using the brake, it was clamped down hard on a 1/4" shaft in the lathe and run for a few minutes to slightly glaze the wood clamping faces. When it was set up on the engine, the engine shaft was well oiled. With the glazed faces running on the oiled shaft, the load can be applied evenly without the stick/slip oscillation that I first got with the dry surface.
This is the procedure that I used. The engine was run up to maximum speed (about 2400 RPM @ 60 PSI). A little load was applied by turning the clamp screw. after 3 or 4 seconds to be sure that the speed and load were stable, the torque was read from the spring scale and and the RPS were read from the tach. This was repeated, adding to the load, reading the data, until I reached a point where the engine stalled. At about 400 RPM, the load began to oscillate to the point that readings could not be taken. I suspect that this is the point where the different cylinder efficiencies of the 4 cylinder engine were being encountered. More on that later if you are interested.
VIDEO:
I was then interrupted by my supervisor (2yr old great grand daughter) , telling me it was time to feed the horses some carrots.
After completing that chore to her satisfaction, I took the data to a spreadsheet and produced two graphs. The first one shows inch pounds of torque vs RPM and the second shows Mousepower (Horsepower/1000) vs RPM.
Only sixteen data points were used in this example and their is some obvious deviation from a smooth curve. The blue line is a B-spline smoothing of the data. More data points would produce a better result but this is good enough for non-contract work. The shape of the curve is about what I expected. Maximum torque ( .37 INCH POUNDS @ 425 RPM ) at low speed, maximum power (3.5 MP @1250 ) at higher speed.
Some points to note:
As the spring scale stretches, the load is overstated due to the effective shortening of the beam. I may work out a method to level the beam before each reading to eliminate this small error.
Even thought the compressor gauge shows 125 PSI, the gauge at the engine with the throttle wide open falls to 60PSI due to leaks and blowby in the engine. The pistons have no rings and the rotary shaft valve is unsealed.
Flywheel weight and design will have some effect. The engine will run well and reach above 2500 RPM with no flywheel but stalls easily if any load is applied. Tomorrow I will get more data points with this flywheel and also with one of the same diameter bu half the weight.
If you are reading this and there are no pictures or video it is because they are uploading. I will edit this posting when they are available.
Jerry
VIDEO

How good? I decided to find out. The tools needed are a non-contact tachometer ($16 from Amazon.com) and a sensitive scale. For about $300 you can get an accurate digital scale or for about $12 you can get an OK spring scale. I went with the spring scale ($12 from an E-bay store). The scale that I got has a capacity range of 0 - .5 Lbs marked in .02lb increments on a scale about 2 inches long. Perfect for the job.
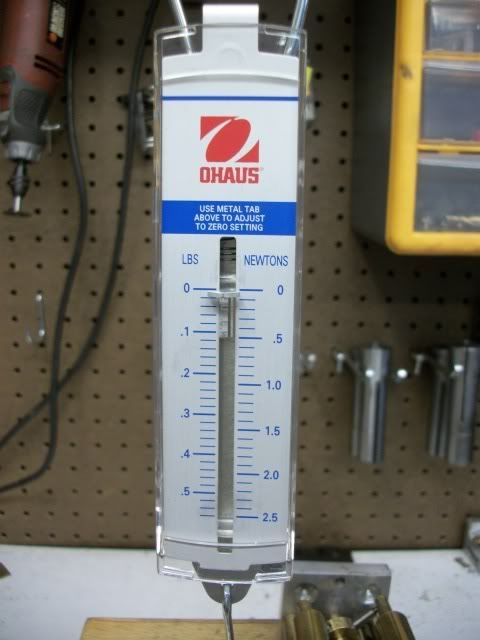
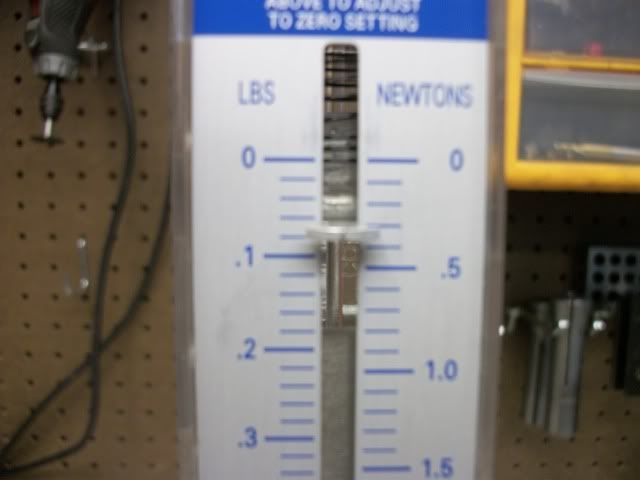
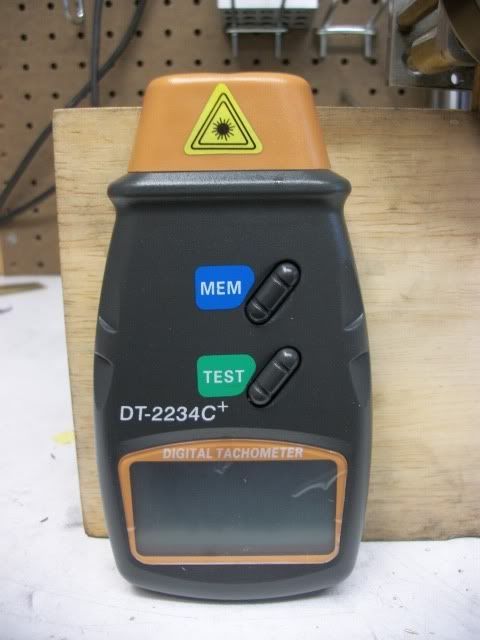
The Prony brake is a simple device made out of a short length 1/4" square red oak. One end is formed into a clamp that is adjusted with a SHC screw and fits around the bare 1/4" engine shaft that extends beyond the flywheel. At a point that is 2 inches from the center of the shaft is pierced by a pin to hold the hangar bracket of the scale. The torque applied by the brake will be directly read from the scale in (inch pounds)/2. The flywheel is 2.5" diameter so it was not practical to set the beam length to 1 inch. The scale is suspended from a shelf above the bench so that the beam of the prony brake is about level. The engine flywheel is wrapped with black tape and a reflective strip for the tachometer is applied.
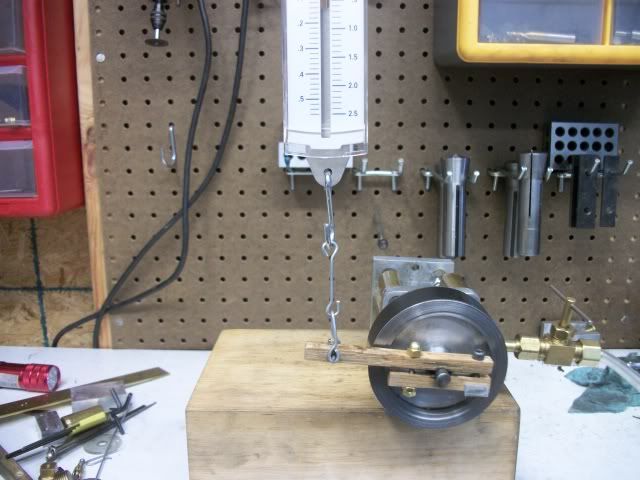
Before using the brake, it was clamped down hard on a 1/4" shaft in the lathe and run for a few minutes to slightly glaze the wood clamping faces. When it was set up on the engine, the engine shaft was well oiled. With the glazed faces running on the oiled shaft, the load can be applied evenly without the stick/slip oscillation that I first got with the dry surface.
This is the procedure that I used. The engine was run up to maximum speed (about 2400 RPM @ 60 PSI). A little load was applied by turning the clamp screw. after 3 or 4 seconds to be sure that the speed and load were stable, the torque was read from the spring scale and and the RPS were read from the tach. This was repeated, adding to the load, reading the data, until I reached a point where the engine stalled. At about 400 RPM, the load began to oscillate to the point that readings could not be taken. I suspect that this is the point where the different cylinder efficiencies of the 4 cylinder engine were being encountered. More on that later if you are interested.
VIDEO:
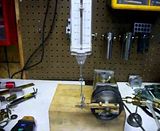
I was then interrupted by my supervisor (2yr old great grand daughter) , telling me it was time to feed the horses some carrots.
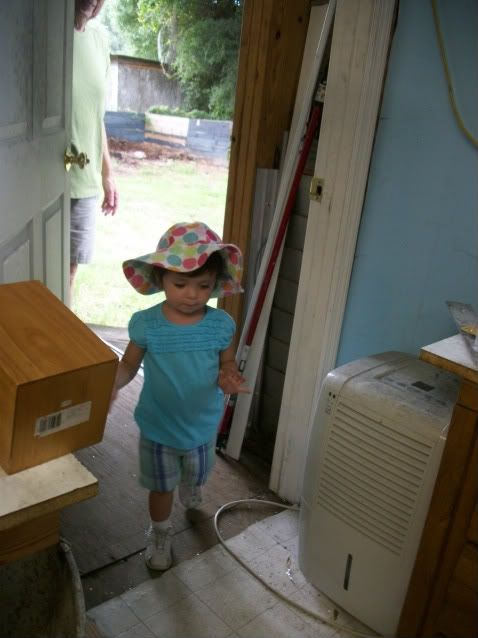
After completing that chore to her satisfaction, I took the data to a spreadsheet and produced two graphs. The first one shows inch pounds of torque vs RPM and the second shows Mousepower (Horsepower/1000) vs RPM.
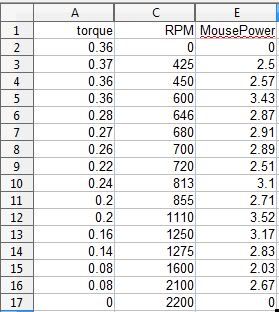
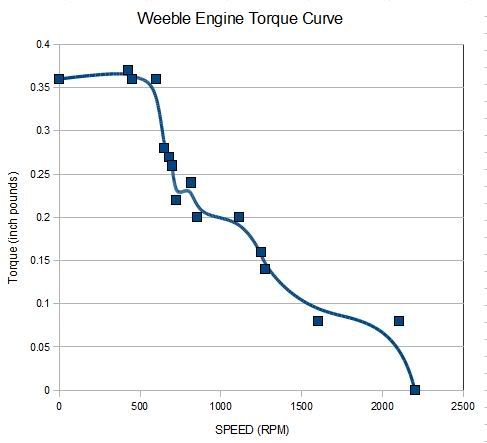
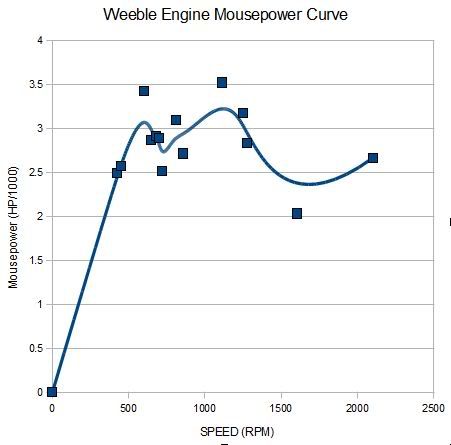
Only sixteen data points were used in this example and their is some obvious deviation from a smooth curve. The blue line is a B-spline smoothing of the data. More data points would produce a better result but this is good enough for non-contract work. The shape of the curve is about what I expected. Maximum torque ( .37 INCH POUNDS @ 425 RPM ) at low speed, maximum power (3.5 MP @1250 ) at higher speed.
Some points to note:
As the spring scale stretches, the load is overstated due to the effective shortening of the beam. I may work out a method to level the beam before each reading to eliminate this small error.
Even thought the compressor gauge shows 125 PSI, the gauge at the engine with the throttle wide open falls to 60PSI due to leaks and blowby in the engine. The pistons have no rings and the rotary shaft valve is unsealed.
Flywheel weight and design will have some effect. The engine will run well and reach above 2500 RPM with no flywheel but stalls easily if any load is applied. Tomorrow I will get more data points with this flywheel and also with one of the same diameter bu half the weight.
If you are reading this and there are no pictures or video it is because they are uploading. I will edit this posting when they are available.
Jerry