BobWarfield
Well-Known Member
- Joined
- Dec 27, 2007
- Messages
- 1,151
- Reaction score
- 1
I use these little HSS steel parting blades:
They're made on a surface grinder, though I buy mine on eBay from seller samsws, and are usually listed as "Cut-Off Parting & Grooving Mini Lathe Tool". The price for 3 was $16, and I've found they work great. You can just pop them into a regular toolholder. Not as heavy duty as the Aloris above, but they do make a much finer cut, so I use them for smaller diameters.
While I love the little parting blades mentioned above, I find they benefit from a little "tuning up." Here's how I do the tune up:
First, use the radius on the edge of your grinding wheel to put a little positive rake in the blade. This greatly reduces chatter on a lot of materials. Easy does it, don't take too much off!
Next, take on of those inexpensive pocket diamond hones and use it to make the tool really sharp. I QCTP holder with the tool on its side on a flat surface, and stand the hone up on it's side. A couple of swipes as shown are all it takes to make the blade really sharp!
This last tip is not really necessary for parting, but I somethings use my parting blade as a turning tool, for example on my Verburg Steam Engine Team Build connecting rods. A radius like this is essential for such cuts. Put the radius on the side you'll be moving into the cut. The radius shown gives you a tool that can take shallow turning cuts moving from tailstock to spindle...
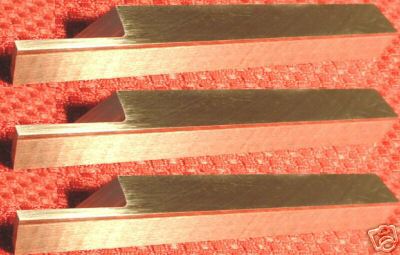
They're made on a surface grinder, though I buy mine on eBay from seller samsws, and are usually listed as "Cut-Off Parting & Grooving Mini Lathe Tool". The price for 3 was $16, and I've found they work great. You can just pop them into a regular toolholder. Not as heavy duty as the Aloris above, but they do make a much finer cut, so I use them for smaller diameters.
While I love the little parting blades mentioned above, I find they benefit from a little "tuning up." Here's how I do the tune up:
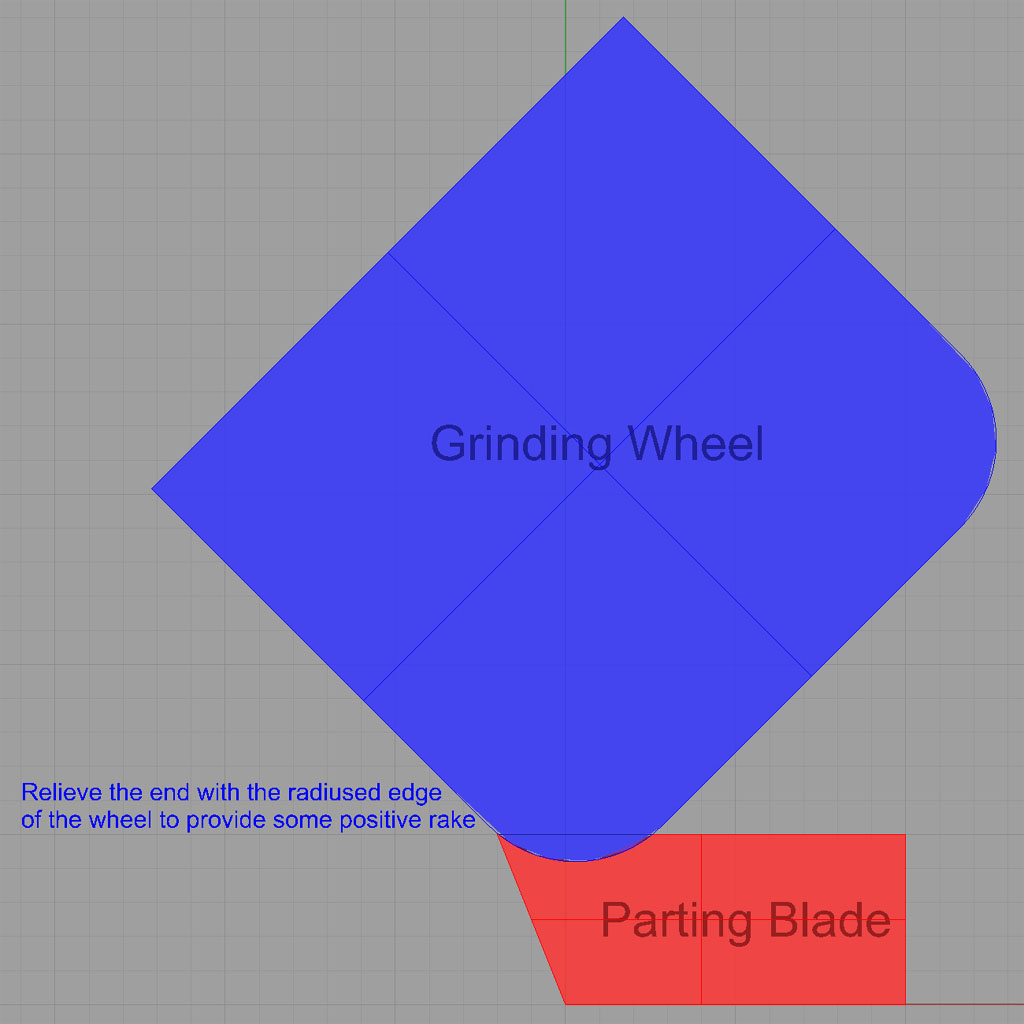
First, use the radius on the edge of your grinding wheel to put a little positive rake in the blade. This greatly reduces chatter on a lot of materials. Easy does it, don't take too much off!

Next, take on of those inexpensive pocket diamond hones and use it to make the tool really sharp. I QCTP holder with the tool on its side on a flat surface, and stand the hone up on it's side. A couple of swipes as shown are all it takes to make the blade really sharp!
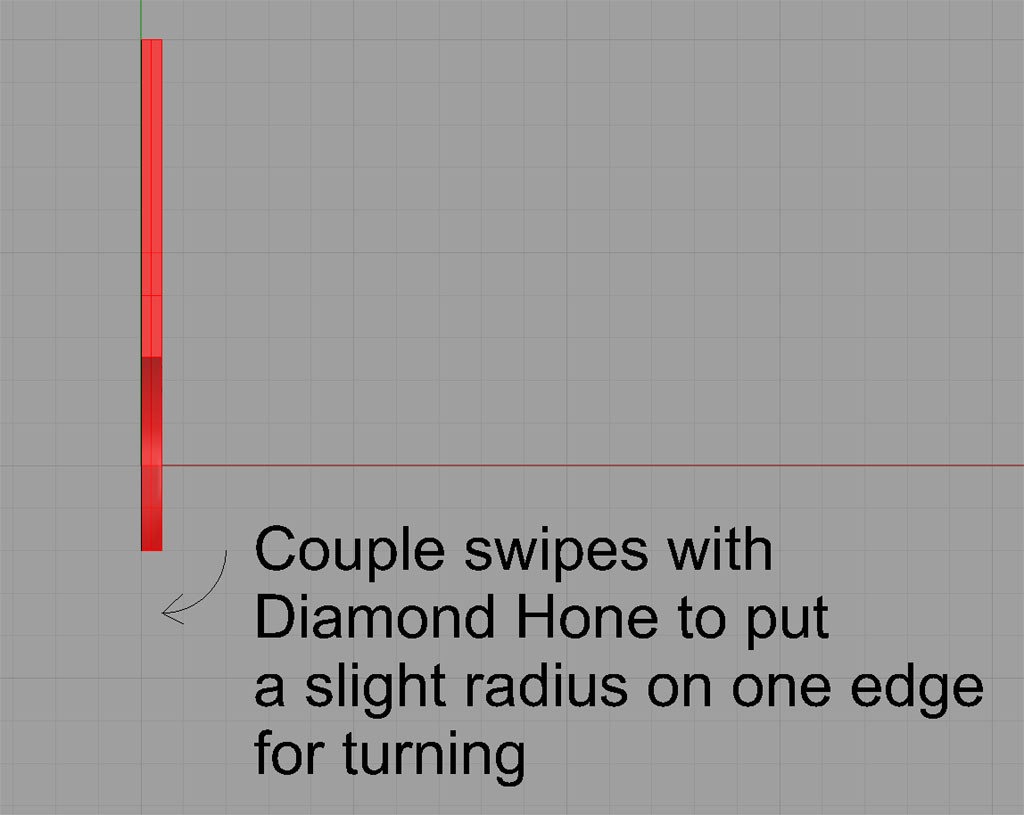
This last tip is not really necessary for parting, but I somethings use my parting blade as a turning tool, for example on my Verburg Steam Engine Team Build connecting rods. A radius like this is essential for such cuts. Put the radius on the side you'll be moving into the cut. The radius shown gives you a tool that can take shallow turning cuts moving from tailstock to spindle...