Well actually my mill isn't an X2 it's a Hafco HM-10 but its exactly the same as an X2 mill.
This is the belt drive kit you get from Little Machine Shop
Here are all the parts straight out of the box.
My mill before I touched it.
Spanner nut removed
Screws removed that holds the cast iron plate to the mill
Motor and cast iron plate removed.
Next the 4 screws are removed that holds cast iron plate to motor and the plate is set aside.
Now the plastic gear is removed and so is it's key as neither are required any more.
Next we remove the retaining clip and the the motor gear. This was a tight fit and required levering off.
Note the key is still in place as this one is still needed.
Next a little plastic sleeve is fitted to the shaft that had the plastic gear on it. This is to just stop it from falling down, if you decide to remove the gears from the gear box this isn't needed.
Next the steel spacer sleeve is removed that was under the spanner nut.
This was also a tight fit and took some effort to get off.
Thats enough pulling apart, its now time to put it back together.
The new base plate is put on the mill and screwed in place.
Now the big pulley is fitted.
The little pulley to the motor.
The motor mount to the motor.
Mine has blind screw holes and the screws were about 2mm too long so I just cut and filed them shorter. I then read the next paragraph that said this may happen and if it does just use the old screws. :
Put the belt in place and fit the motor mount and all done.
This is one of the rare times when after you finish the job you are allowed to have a small pile of 'spare parts' left over. :big:
Job for the next night.
I've got to say the instructions were well written, the parts fitted perfectly and it wasn't that hard to do. It took me about an hour and if I hadn't been taking photos and stopping to change the music I was playing in my workshop I could of probably done this in under 30 minutes.
The mill also runs considerably quieter and you leave the gearbox in neutral is you don't remove the lower gears. I'm very happy with this mod.
This is the belt drive kit you get from Little Machine Shop
Here are all the parts straight out of the box.
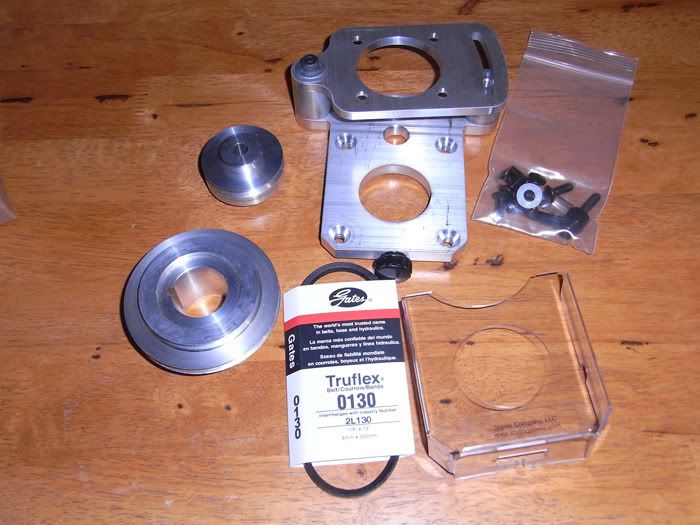
My mill before I touched it.
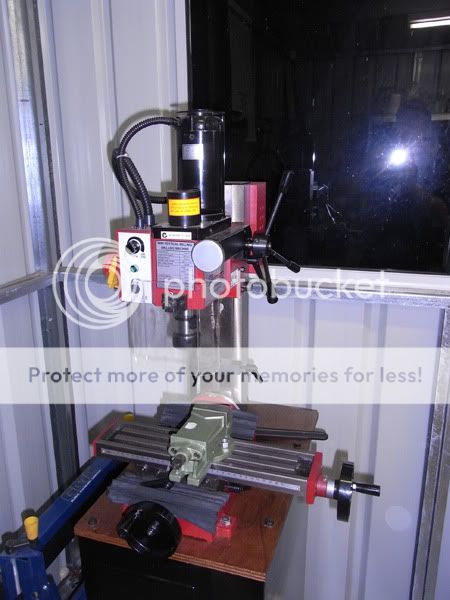
Spanner nut removed

Screws removed that holds the cast iron plate to the mill

Motor and cast iron plate removed.
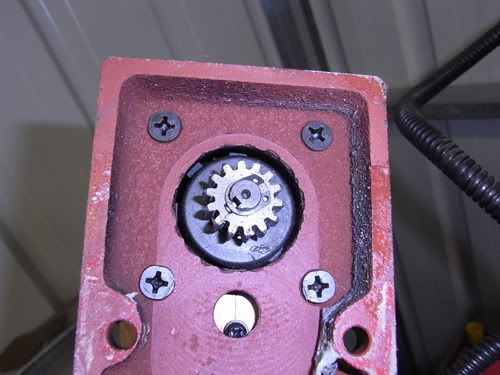
Next the 4 screws are removed that holds cast iron plate to motor and the plate is set aside.

Now the plastic gear is removed and so is it's key as neither are required any more.
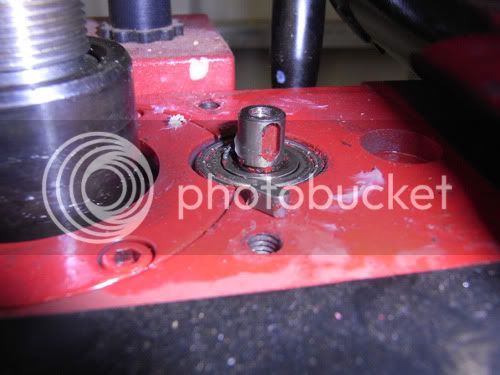
Next we remove the retaining clip and the the motor gear. This was a tight fit and required levering off.

Note the key is still in place as this one is still needed.
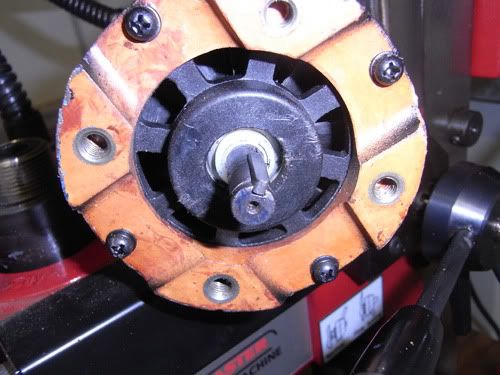
Next a little plastic sleeve is fitted to the shaft that had the plastic gear on it. This is to just stop it from falling down, if you decide to remove the gears from the gear box this isn't needed.
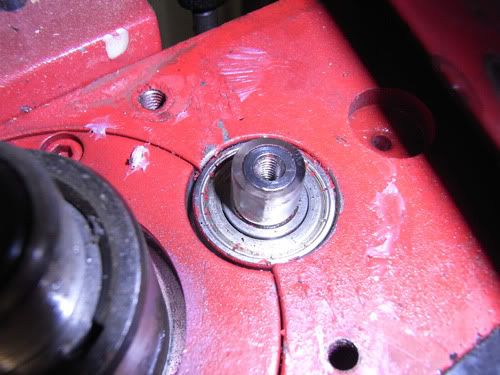
Next the steel spacer sleeve is removed that was under the spanner nut.
This was also a tight fit and took some effort to get off.
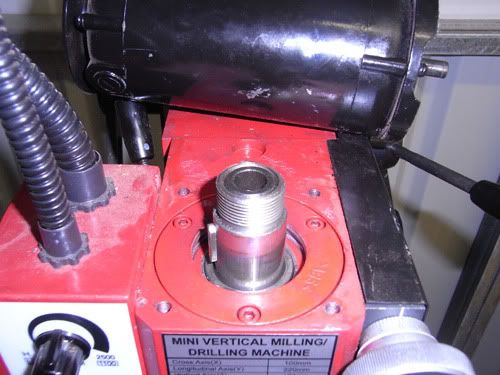
Thats enough pulling apart, its now time to put it back together.
The new base plate is put on the mill and screwed in place.
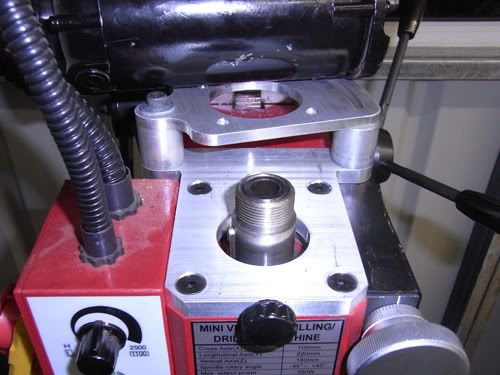
Now the big pulley is fitted.
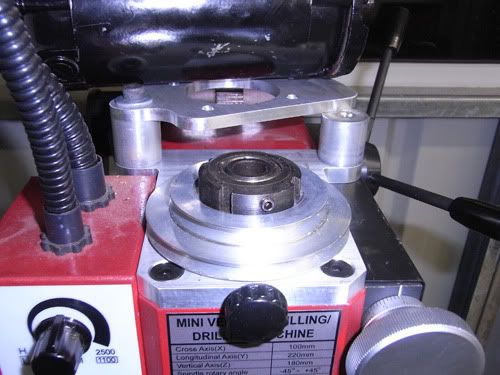
The little pulley to the motor.
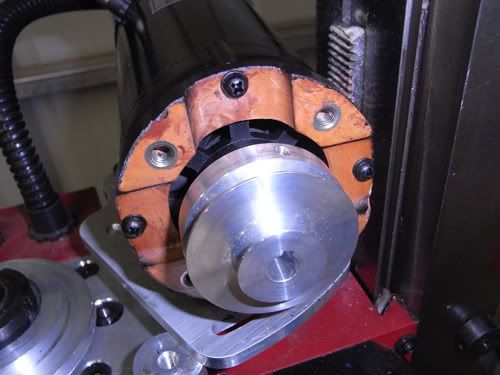
The motor mount to the motor.
Mine has blind screw holes and the screws were about 2mm too long so I just cut and filed them shorter. I then read the next paragraph that said this may happen and if it does just use the old screws. :

Put the belt in place and fit the motor mount and all done.

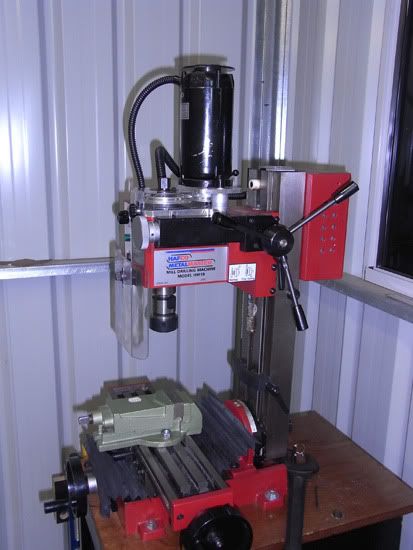
This is one of the rare times when after you finish the job you are allowed to have a small pile of 'spare parts' left over. :big:
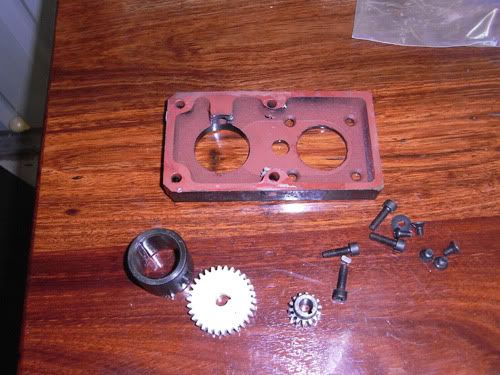
Job for the next night.

I've got to say the instructions were well written, the parts fitted perfectly and it wasn't that hard to do. It took me about an hour and if I hadn't been taking photos and stopping to change the music I was playing in my workshop I could of probably done this in under 30 minutes.
The mill also runs considerably quieter and you leave the gearbox in neutral is you don't remove the lower gears. I'm very happy with this mod.