toolznthings
Project of the Month Winner
Hi All,
Started another build with a scaled up version of the Fancy Vertical. I increased the size by a scale of three times which makes the overall height with the base about 8 1/2" tall. The crank shaft axle and the wrist pin were sized to .500 and .250 instead of .562 and .281. The air passages were drilled to 1/8". Everything else worked out at the 3x scaling.
The main body was turned from 1144 stressproof with the largest diameter being 2.250" diameter. After completing the lathe work I rough milled the flat on the body leaving grind stock.
I made a setup with a vise on the surface grinder to finish the flat on the body.
This left me with a smooth and flat surface for the cylinder
The finished flat on the main body .....
Started another build with a scaled up version of the Fancy Vertical. I increased the size by a scale of three times which makes the overall height with the base about 8 1/2" tall. The crank shaft axle and the wrist pin were sized to .500 and .250 instead of .562 and .281. The air passages were drilled to 1/8". Everything else worked out at the 3x scaling.
The main body was turned from 1144 stressproof with the largest diameter being 2.250" diameter. After completing the lathe work I rough milled the flat on the body leaving grind stock.
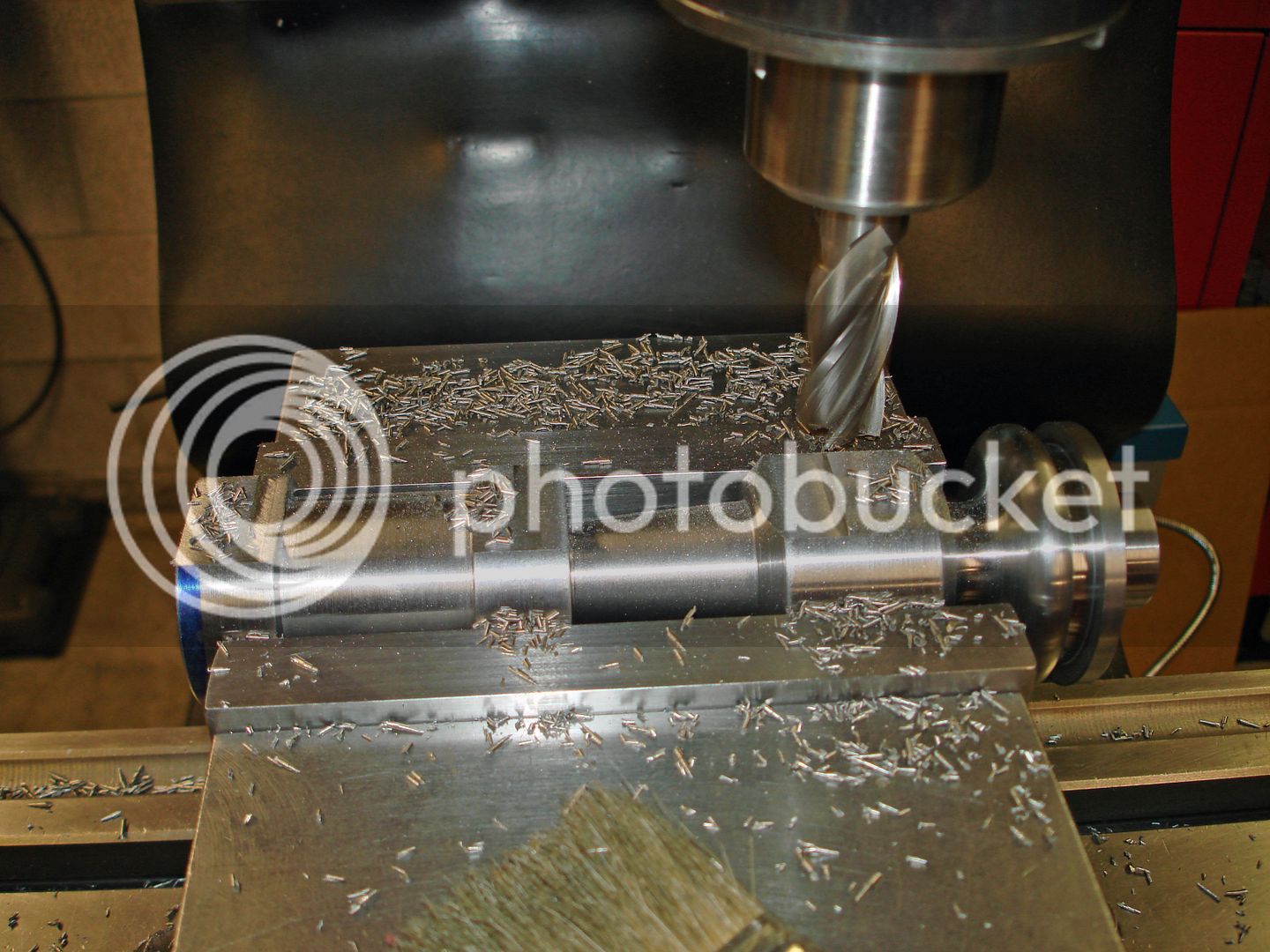
I made a setup with a vise on the surface grinder to finish the flat on the body.
This left me with a smooth and flat surface for the cylinder

The finished flat on the main body .....
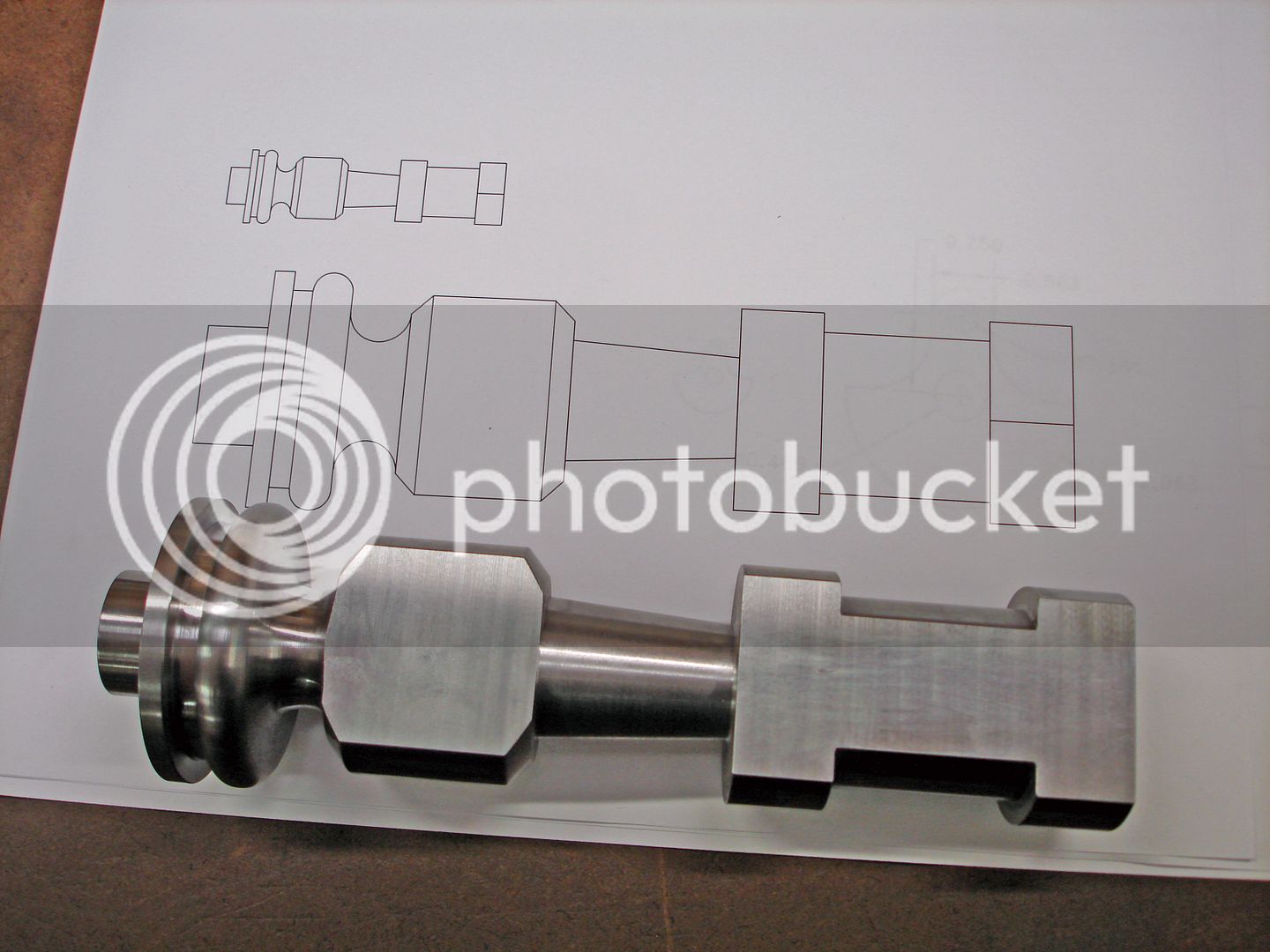