Heffalump
Well-Known Member
- Joined
- Jan 18, 2014
- Messages
- 75
- Reaction score
- 15
Hiya Chaps,
This is going to be the first thing I've built since college, and I'll be re-learning how to machine as I go along.
I'm going to be building the simple oscillating engine found here: http://www.steves-workshop.co.uk/steammodels/simpleoscil/simpleoscil.htm
I started first by making the base plate. As this was the least critical part I thought it would be a good one to get my eye in on.
To start with I found a random piece of Ally sheet lying around and got it clamped down on the mill bed.
Here's the blank cut to size
And the stub drill bit set to 0,0 (DRO making life too easy)
Then finally the two holes through which I'll attach the frame.
It was fun trying to remember how everything works!
In hindsight, I should have protected the workpiece from the clamps, and I shouldn't have used a file to deburr the edges, so it is quite a messy piece now, but still fit for purpose.
Thanks for looking
This is going to be the first thing I've built since college, and I'll be re-learning how to machine as I go along.
I'm going to be building the simple oscillating engine found here: http://www.steves-workshop.co.uk/steammodels/simpleoscil/simpleoscil.htm
I started first by making the base plate. As this was the least critical part I thought it would be a good one to get my eye in on.
To start with I found a random piece of Ally sheet lying around and got it clamped down on the mill bed.
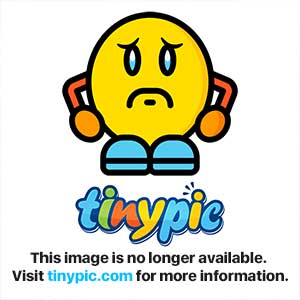
Here's the blank cut to size
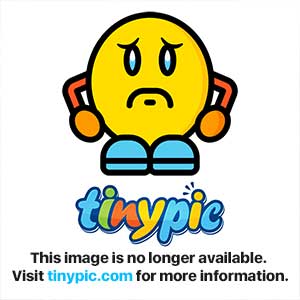
And the stub drill bit set to 0,0 (DRO making life too easy)
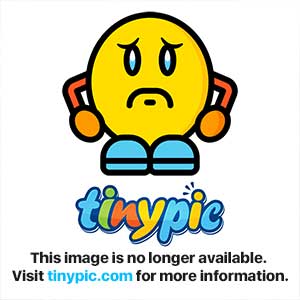
Then finally the two holes through which I'll attach the frame.

It was fun trying to remember how everything works!
In hindsight, I should have protected the workpiece from the clamps, and I shouldn't have used a file to deburr the edges, so it is quite a messy piece now, but still fit for purpose.
Thanks for looking