Metal butcher was asking about a built up flywheel. I didn't want to take over his thread, so decided to do a quick post on how I think it could be done with no silver soldering, threading, nor press fits. If I am way out to lunch on this, well, correct me, but I think this is pretty valid. Step one involves turning a thick plate as shown (picture is a half section to show more plainly.)
---Brian
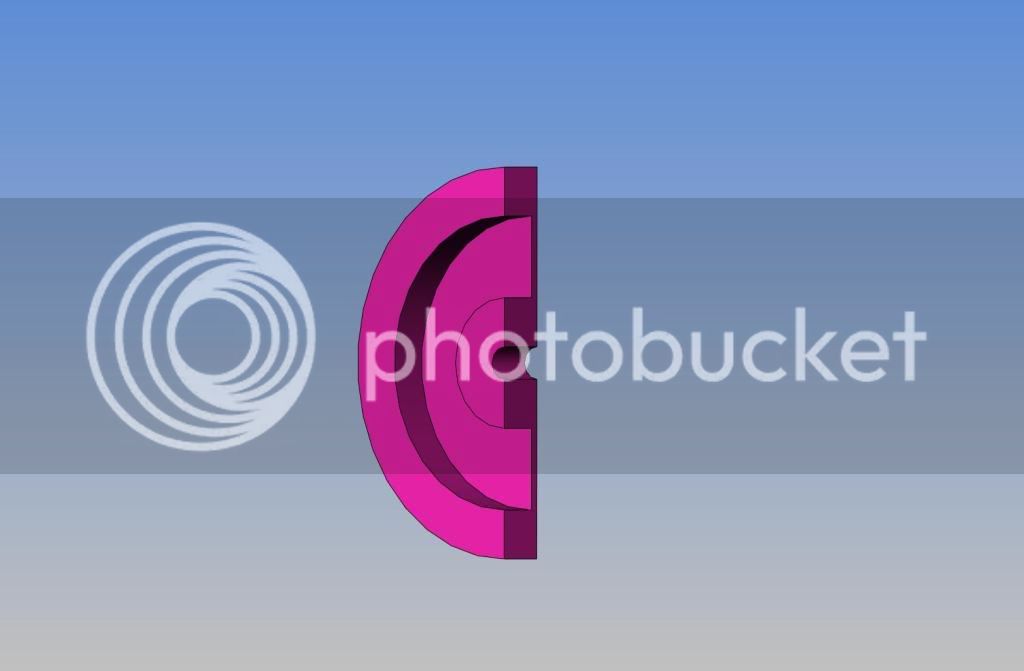