Gentlemen
This little critter is creating untold frustration for me; it is the slide ram bearing holder on my Atlas 7B shaper. This is the plate thats bolted to the gear wheel. I had a slight knock while the machine was reciprocating so I dug this block out and found that the hardened boss had worked its way loose, so I ground off the steel that was holding it and cleaned it up then seated it back and while holding it square and under pressure from clamps I back welded it.
The repair did not work. The weld cooled and now its not square. So I want to machine it on the face plate of my lathe but alas the boss is hardened and thats my dilemma.
Can I, and how would I anneal this in one piece? I would rather keep it in one piece as that it would only take one set up to machine and re-harden. If I were to grind off the boss again it would need to be machined then I would have to repair the base plate, center and locate the boss affix it somehow, as you can see its would be a messy deal.
This plate has a flat surface on the back to which is perpendicular to the ram bed on top, and the boss diameter has a tolerance of about .001 +/- The base plate is not hard its just regular cold rolled steel. Would through the heating process the base plate warp? Then when heating the boss back and hardening it would it affect the base plate? How do I just harden the boss and not the plate blow torch, fire, oven? . Tools I have at my disposal are Oxy-acetylene rig, open pit fire, an oven.
Remember when giving your thoughts please be quite graphic and detailed in your explanations as I have never hardened, case hardened or tempered anything in my life. Whatever we come up with I will post as a project.
Many thanks in advance. Anthony
This little critter is creating untold frustration for me; it is the slide ram bearing holder on my Atlas 7B shaper. This is the plate thats bolted to the gear wheel. I had a slight knock while the machine was reciprocating so I dug this block out and found that the hardened boss had worked its way loose, so I ground off the steel that was holding it and cleaned it up then seated it back and while holding it square and under pressure from clamps I back welded it.
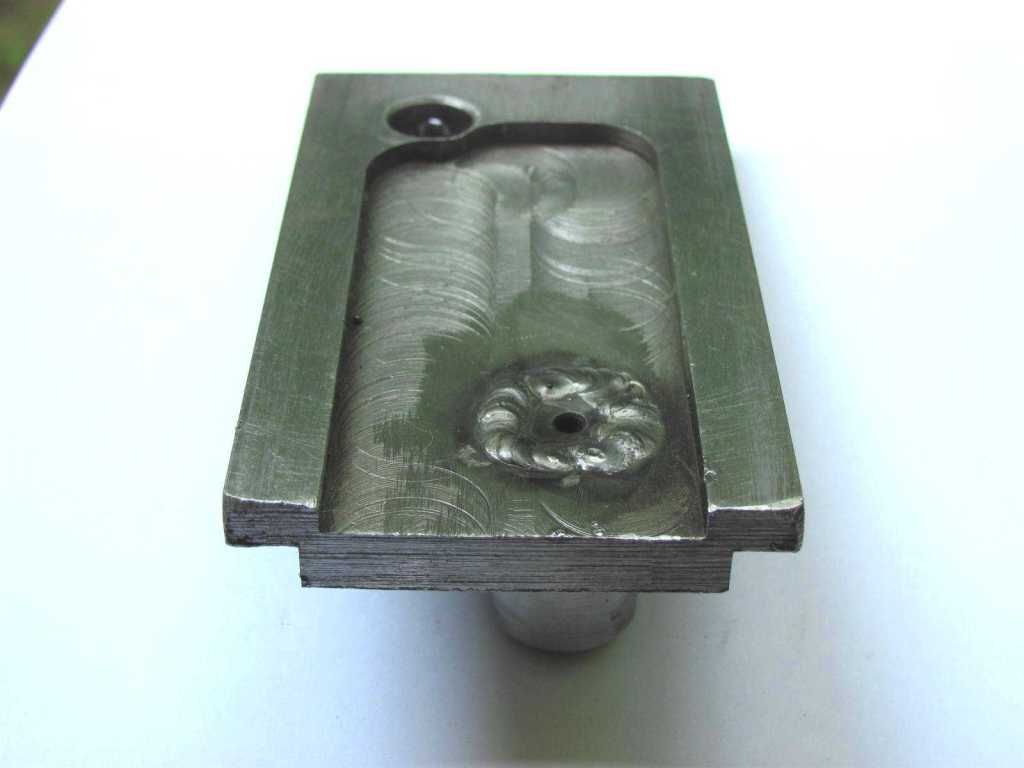
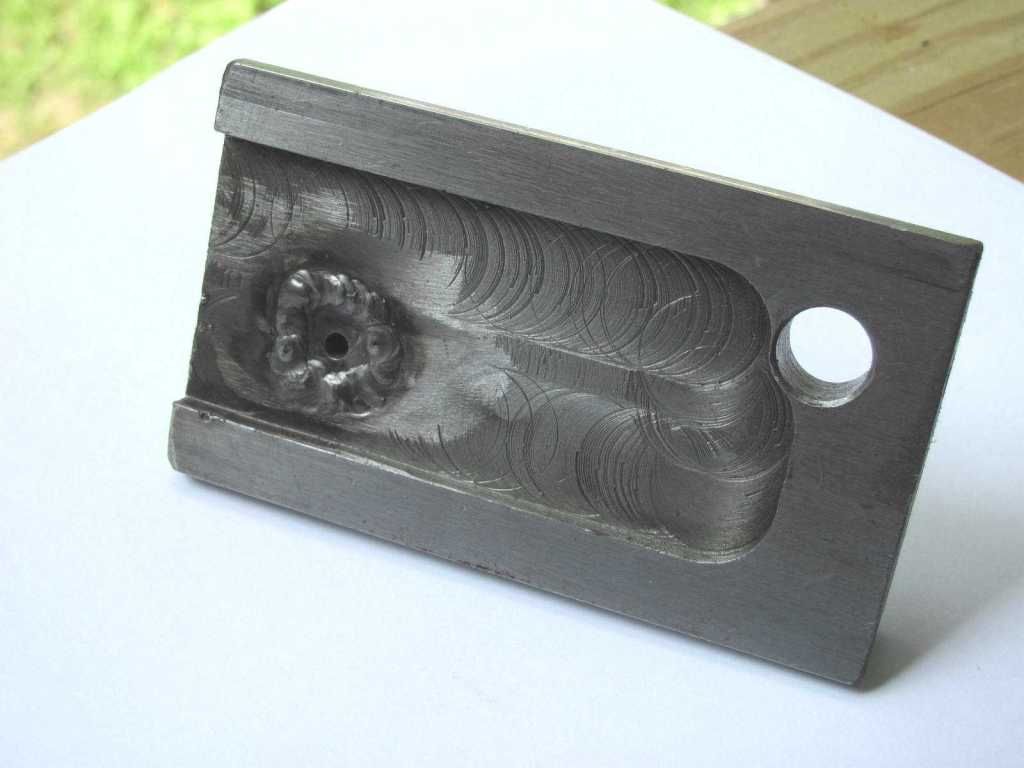
The repair did not work. The weld cooled and now its not square. So I want to machine it on the face plate of my lathe but alas the boss is hardened and thats my dilemma.
Can I, and how would I anneal this in one piece? I would rather keep it in one piece as that it would only take one set up to machine and re-harden. If I were to grind off the boss again it would need to be machined then I would have to repair the base plate, center and locate the boss affix it somehow, as you can see its would be a messy deal.
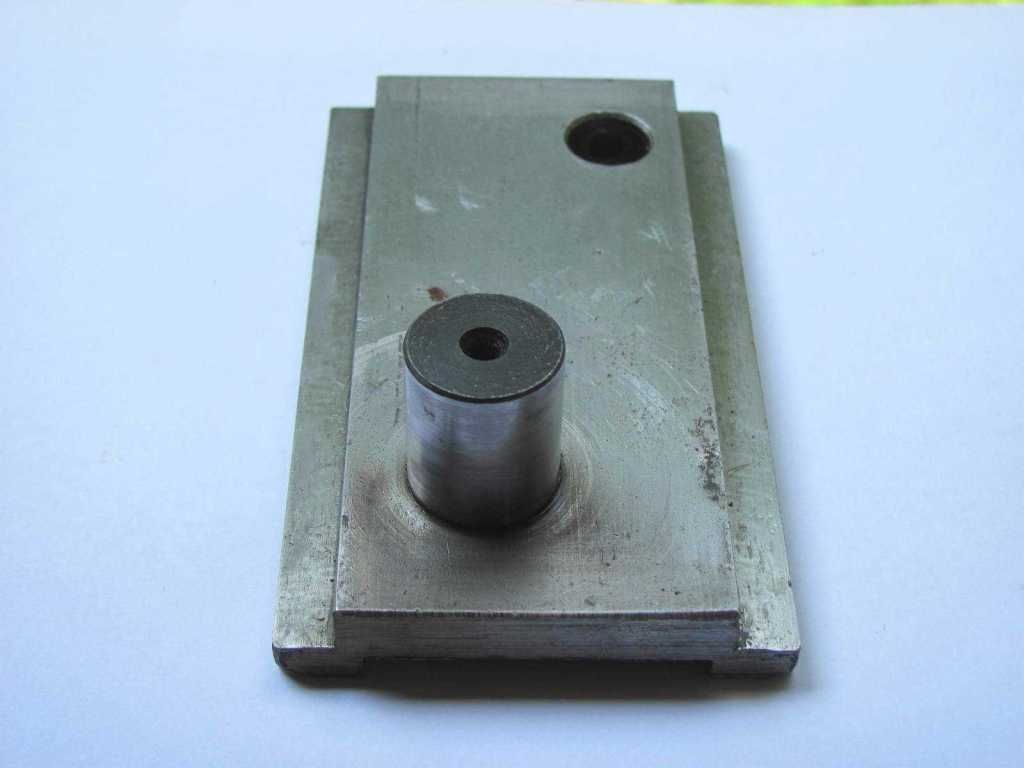
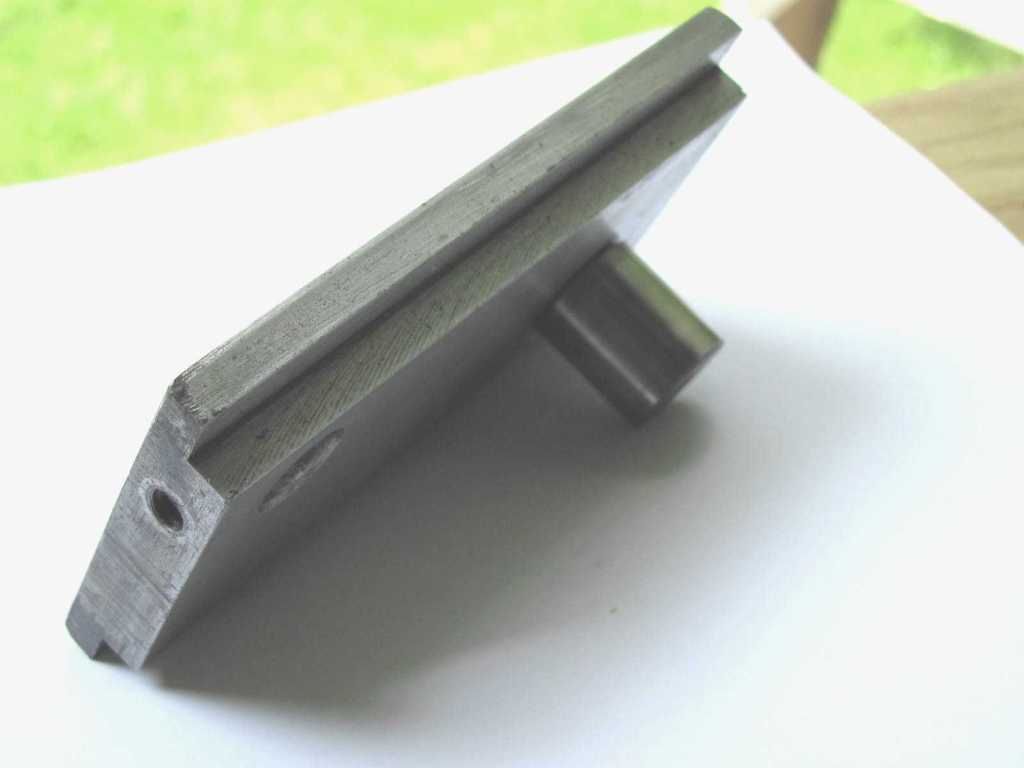

This plate has a flat surface on the back to which is perpendicular to the ram bed on top, and the boss diameter has a tolerance of about .001 +/- The base plate is not hard its just regular cold rolled steel. Would through the heating process the base plate warp? Then when heating the boss back and hardening it would it affect the base plate? How do I just harden the boss and not the plate blow torch, fire, oven? . Tools I have at my disposal are Oxy-acetylene rig, open pit fire, an oven.
Remember when giving your thoughts please be quite graphic and detailed in your explanations as I have never hardened, case hardened or tempered anything in my life. Whatever we come up with I will post as a project.
Many thanks in advance. Anthony