Hi, all
Well this is my first post here and I thought I'd intro myself. Thanks to BobW's cookbook i found this site. Although machining is second to woodworking for me, this site really peaked my interest in model engineering. Thanks, Rak. I'm sort of like a BobW except on a much let's say leaner budget. I have a 1960's southbend 9a with some tooling and a wells index milling maching. I used/bought these to build an ali extruded frame cnc gantry router and have a full compliment cabinet shop. My dad's business is stamping so I've got access to press brakes, punch presses and a B&S grinder.
So now on to the meat of the post. I found this stirling on the garrett-wade catalog and it looked like a good place to start. So my question to everyone how would you go about designing this from a pic. So here if this works is the pic, the base is 4.25"x6.25", and that's the only scale that I have. I like the twin.
So, instead of a team build how about a team design based on the pic. I'm clueless about how the stirlings work, I'm still studying the basic of them online. How do you design the drive mechanisms and cams etc. Hopefully Bog will see this and maybe have a few moments while he's out of the shop to sketch up some idears.
Maybe this too ambitious a project to start out here, but I like starting in the deep end, sink or swim...you usually learn more along the way.
Thanks everyone
Brian
Well this is my first post here and I thought I'd intro myself. Thanks to BobW's cookbook i found this site. Although machining is second to woodworking for me, this site really peaked my interest in model engineering. Thanks, Rak. I'm sort of like a BobW except on a much let's say leaner budget. I have a 1960's southbend 9a with some tooling and a wells index milling maching. I used/bought these to build an ali extruded frame cnc gantry router and have a full compliment cabinet shop. My dad's business is stamping so I've got access to press brakes, punch presses and a B&S grinder.
So now on to the meat of the post. I found this stirling on the garrett-wade catalog and it looked like a good place to start. So my question to everyone how would you go about designing this from a pic. So here if this works is the pic, the base is 4.25"x6.25", and that's the only scale that I have. I like the twin.
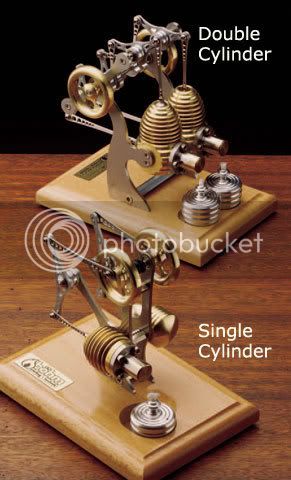
So, instead of a team build how about a team design based on the pic. I'm clueless about how the stirlings work, I'm still studying the basic of them online. How do you design the drive mechanisms and cams etc. Hopefully Bog will see this and maybe have a few moments while he's out of the shop to sketch up some idears.
Maybe this too ambitious a project to start out here, but I like starting in the deep end, sink or swim...you usually learn more along the way.
Thanks everyone
Brian