TopEndScraper
Member
- Joined
- Jul 23, 2013
- Messages
- 18
- Reaction score
- 10
im Just wondering if any members are from Darwin or the Northern Territory , Australia
Ive started to draw up the " Kelly & lewis , 15" duplex pump " from the Darwin WW2 oil storage tunnels , and just seing if any one is interested in making one ( or 2 )
Im drawing them in CAD , and have a CNC machine to make the patterns , and have the furnace / sand to cast the peaces
I was looking at making 6 of them , the set has 2 identical pumps , 1 set for the Tunnels , one set for the Qantas Hanger , and one set for me
These are the pumps , they were made in the late 1920's in Melbourne by Kelly&Lewis ( still trading ) and the photo is of the Darwin oil storage pump shed , and how they were set up , there still there in the building , but decommissioned ,
The only set of plans i could fine are a bit hard too read the measurements but easy enough to scale off what can be read , Ive emailed Kelly & lewis to see if they have a better set of plans showing the valve lay out inside the pump head , but i can always go see the port authority as the pumps are still in position
the scale i was going to use , was based on the bolt size , so drawing it to take 2mm bolts so i dont have to modify the plans too much and change the way they look , wall thickness is always a problem when scaling but should be able to hide those internally , scale should end up 10:1 , so a 13/16bolt ends up 2mm
so if anyone is interested , keep in touch
cheers ken
Ive started to draw up the " Kelly & lewis , 15" duplex pump " from the Darwin WW2 oil storage tunnels , and just seing if any one is interested in making one ( or 2 )
Im drawing them in CAD , and have a CNC machine to make the patterns , and have the furnace / sand to cast the peaces
I was looking at making 6 of them , the set has 2 identical pumps , 1 set for the Tunnels , one set for the Qantas Hanger , and one set for me
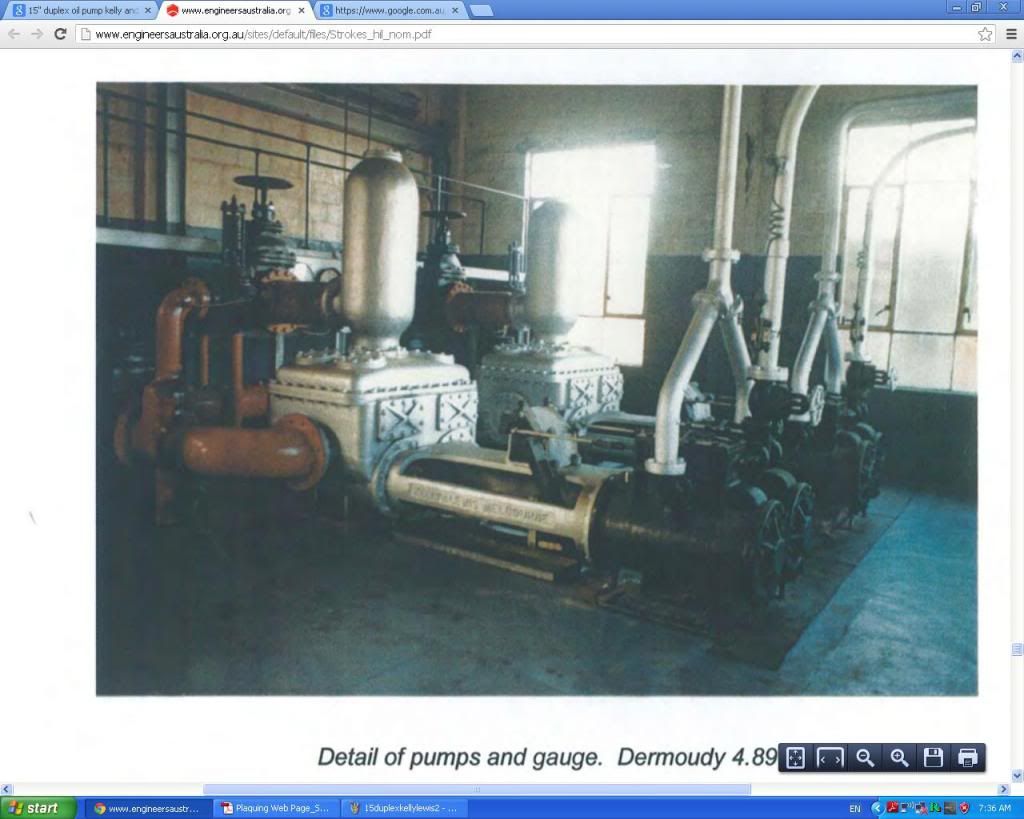
These are the pumps , they were made in the late 1920's in Melbourne by Kelly&Lewis ( still trading ) and the photo is of the Darwin oil storage pump shed , and how they were set up , there still there in the building , but decommissioned ,
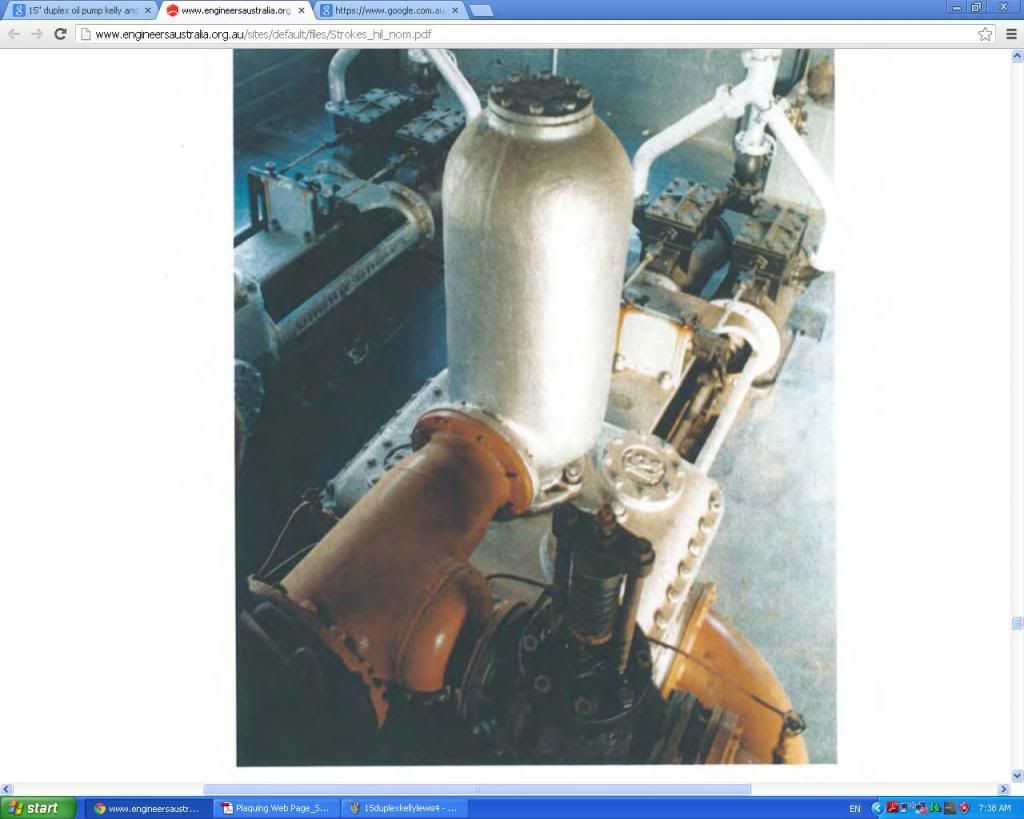
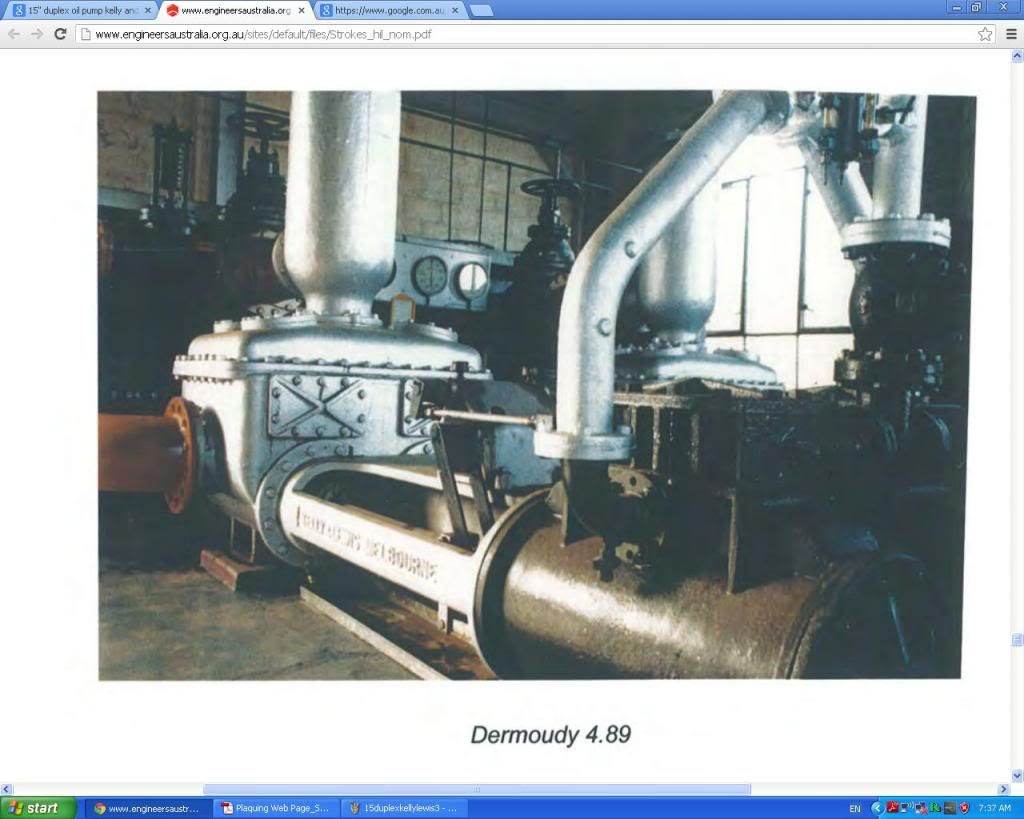
The only set of plans i could fine are a bit hard too read the measurements but easy enough to scale off what can be read , Ive emailed Kelly & lewis to see if they have a better set of plans showing the valve lay out inside the pump head , but i can always go see the port authority as the pumps are still in position
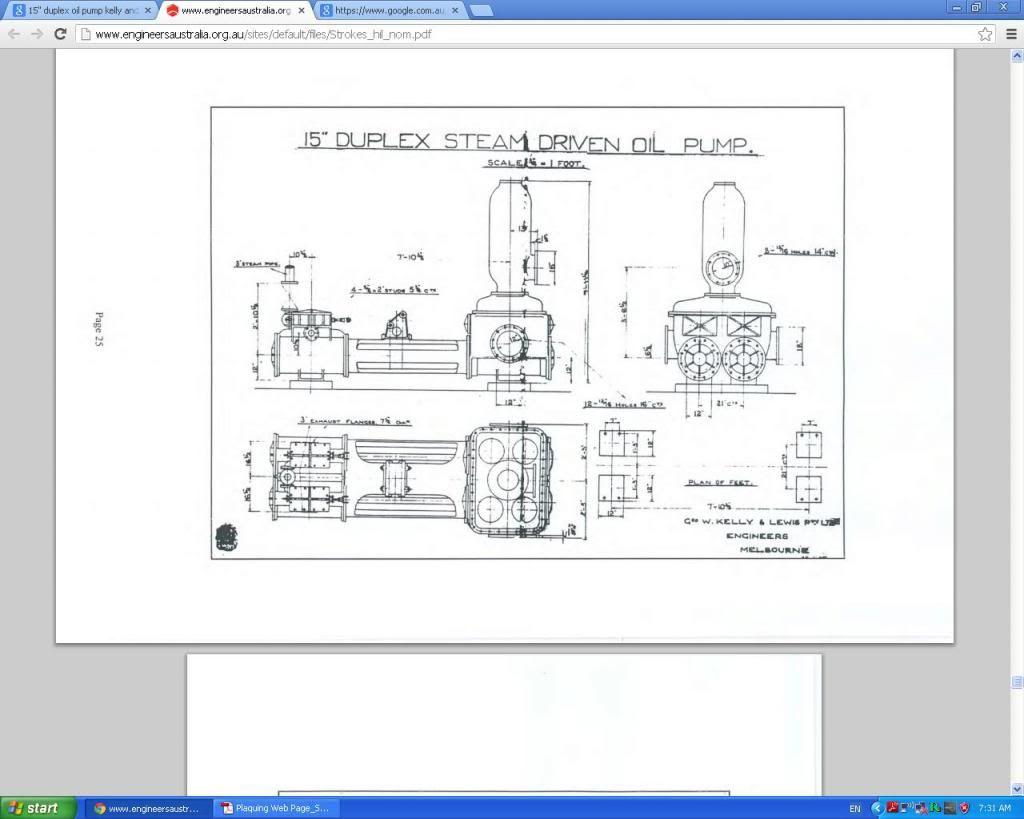
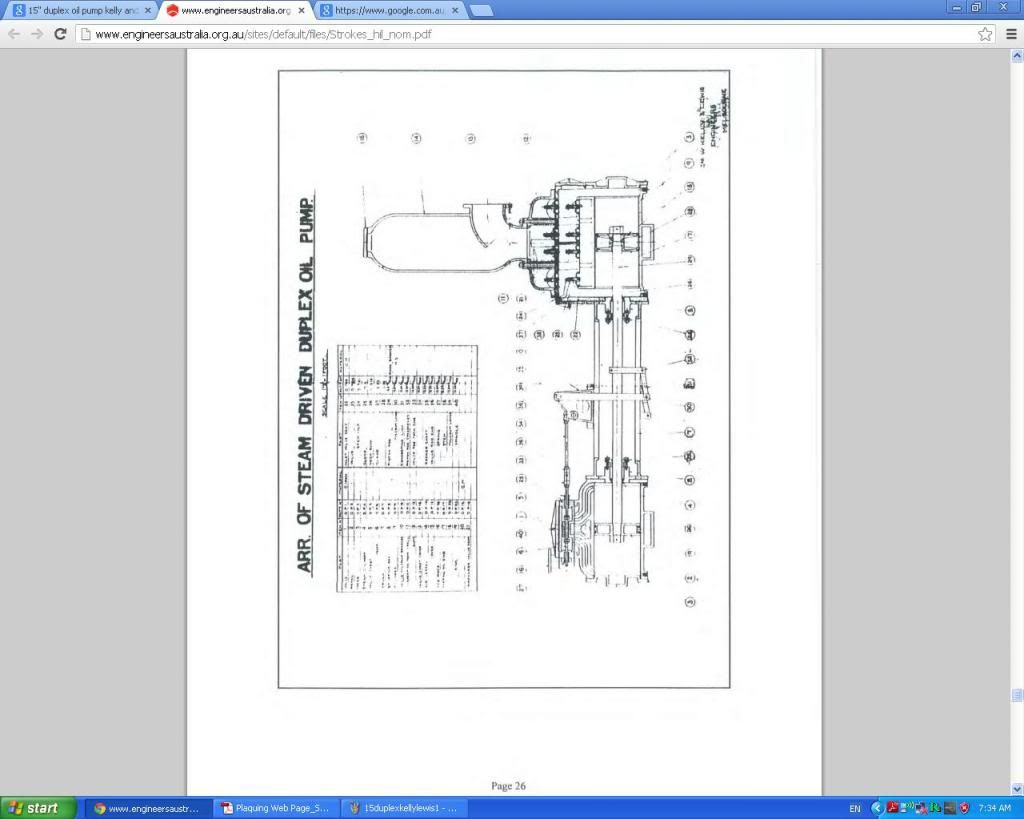
the scale i was going to use , was based on the bolt size , so drawing it to take 2mm bolts so i dont have to modify the plans too much and change the way they look , wall thickness is always a problem when scaling but should be able to hide those internally , scale should end up 10:1 , so a 13/16bolt ends up 2mm
so if anyone is interested , keep in touch
cheers ken