- Joined
- Jan 17, 2009
- Messages
- 887
- Reaction score
- 81
I've not bin Idle these last couple of weeks I've bin doing a bit of research on an engine that caught my eye. Its a bit of a strange beast it has a rotary action that I can best describe as a captive eccentric. The original was first displayed at the great exhibition and was shown powering some textile machinery, as far as I can find out only two were made, though there is very little documentary evidence for the second.
I've got enough of the drawing done to show you an assembly, but I still need to do more detailing of the parts, but its enough to give you an idea of how it will look.
I'll slowly work on the drawing and start to get material together ready to make a start and cut metal in the new year.
Stew
I've got enough of the drawing done to show you an assembly, but I still need to do more detailing of the parts, but its enough to give you an idea of how it will look.
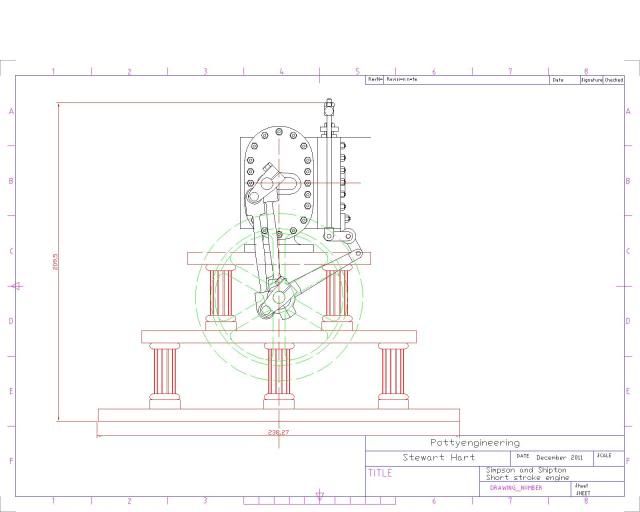
I'll slowly work on the drawing and start to get material together ready to make a start and cut metal in the new year.
Stew