I need to make a flywheel for my Popcorn engine, and although I probably could make one with "wiggly" spokes, I have decided on a somewhat different approach. I have designed a "built up" flywheel in which one could use just about any kind of spokes they could dream up, and requires no soldering nor fasteners. I'm not 100% sure this will turn out okay, but we will go along for the ride and find out!!! The two models posted here show it "together" and "exploded" to give some idea of the construction method. The spokes are assembled to the hub with Loctite, the hub and spokes are then layed in the milled pockets in the outer rim, then the inner rim is Loctited into the outer rim, capturing the spokes in place. This means that the spokes can be an entirely different metal than either the hub or outer rim.
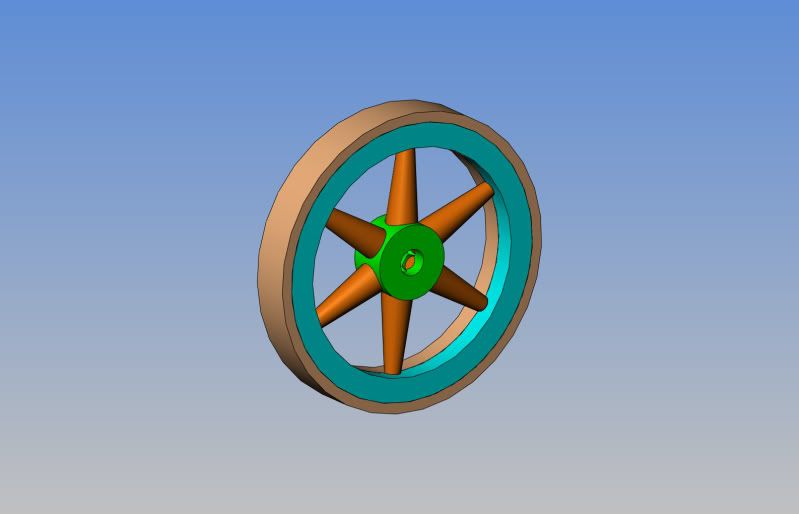
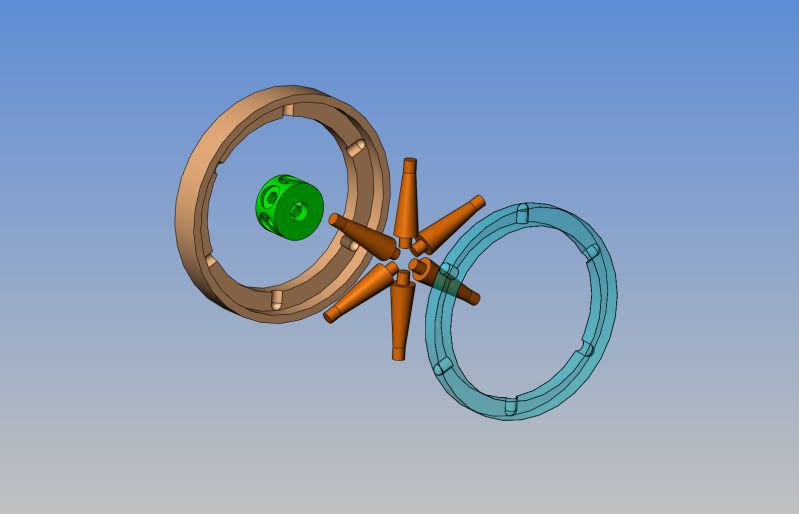