- Joined
- Dec 28, 2008
- Messages
- 1,731
- Reaction score
- 9
Hi guys. With vacation over and other duties finished and out of the way, I'm ready and back in the shop. To start off my season I will begin by building 5 versions of I.C. engines designed by the late Hamilton Upshur. After a month of poking around for information and gathering up most of the supplies I'm starting my build's even though their are still a few problems such as the flywheels to overcome.
I purchased a set of plans from Hamilton's daughter, and when they arrived I knew this was going to be a great project for me. Not only are the hand drawn plans easy on my eyes, they make visualizing each part very simple. I always say that if I can visualize a part in my mind than the rest is easy. Another nice feature of this plan set is that multiple versions can be built, and the plan set include building notes and construction options for parts such as the piston and crank shaft. Below is a list of the building options that I see.
1) Horizontal water cooled 4 stroke
2) Horizontal water cooled hit-n-miss
3) F Head horizontal 4 stroke
4) F Head horizontal hit-n-miss
5) Horizontal air cooled 4 stroke
6) Horizontal air cooled hit-n-miss
7) Vertical air cooled 4 stroke
8) Vertical air cooled hit-n-miss
9) Vertical F Head 4 stroke
10) Vertical F Head hit-n-miss
You can also build customized versions of any, or all of the above!
I think you can see why I'm so happy with these plans. Not free ($13.50), but a good value for the money spent
Upshur Engine Works link: http://hamiltonupshur.tripod.com/
In the picture below, 20 aluminum frame plates for the 5 engines have been rough cut, milled square, and milled to final dimensions.
With snacks on hand, I'm ready for the final inspection of the frame plates. ("Honey" had to go back to the store and buy more candy... twice!) The stuff tastes Really good this year! ;D
-MB
I purchased a set of plans from Hamilton's daughter, and when they arrived I knew this was going to be a great project for me. Not only are the hand drawn plans easy on my eyes, they make visualizing each part very simple. I always say that if I can visualize a part in my mind than the rest is easy. Another nice feature of this plan set is that multiple versions can be built, and the plan set include building notes and construction options for parts such as the piston and crank shaft. Below is a list of the building options that I see.
1) Horizontal water cooled 4 stroke
2) Horizontal water cooled hit-n-miss
3) F Head horizontal 4 stroke
4) F Head horizontal hit-n-miss
5) Horizontal air cooled 4 stroke
6) Horizontal air cooled hit-n-miss
7) Vertical air cooled 4 stroke
8) Vertical air cooled hit-n-miss
9) Vertical F Head 4 stroke
10) Vertical F Head hit-n-miss
You can also build customized versions of any, or all of the above!
I think you can see why I'm so happy with these plans. Not free ($13.50), but a good value for the money spent
Upshur Engine Works link: http://hamiltonupshur.tripod.com/
In the picture below, 20 aluminum frame plates for the 5 engines have been rough cut, milled square, and milled to final dimensions.
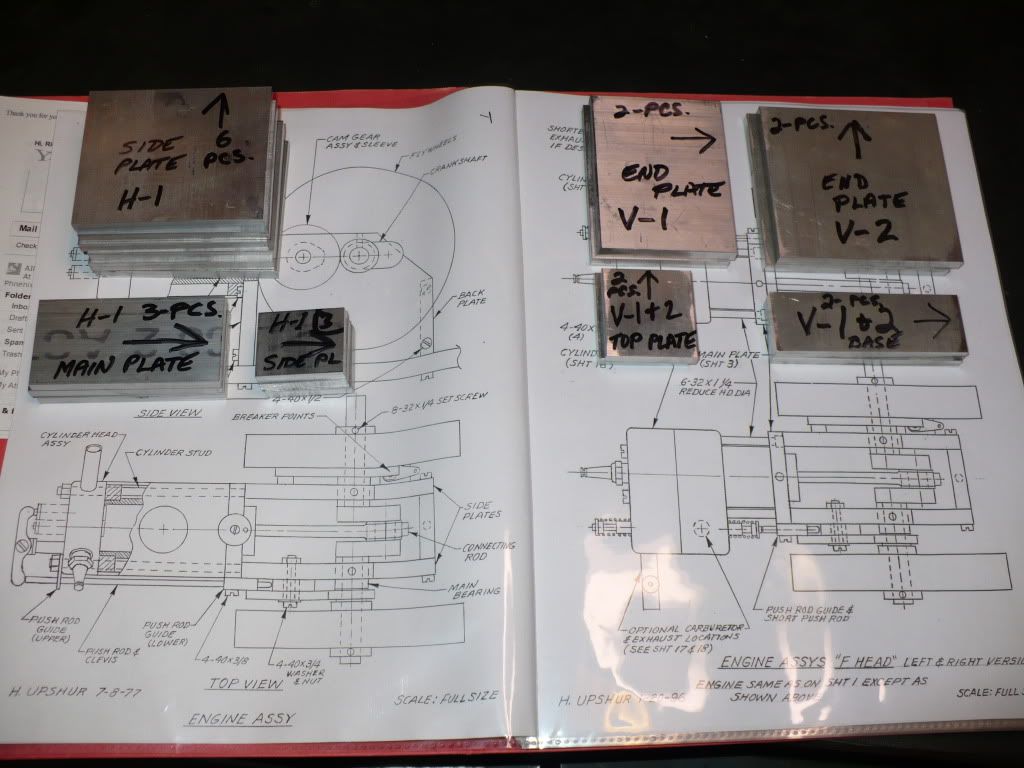
With snacks on hand, I'm ready for the final inspection of the frame plates. ("Honey" had to go back to the store and buy more candy... twice!) The stuff tastes Really good this year! ;D
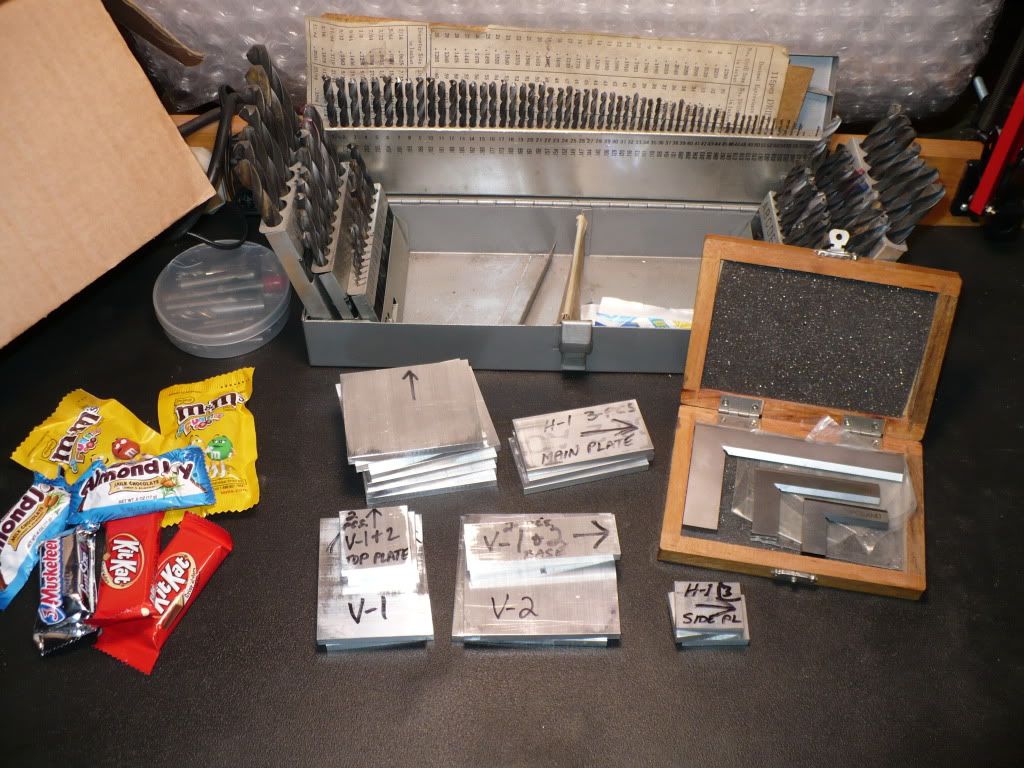
-MB